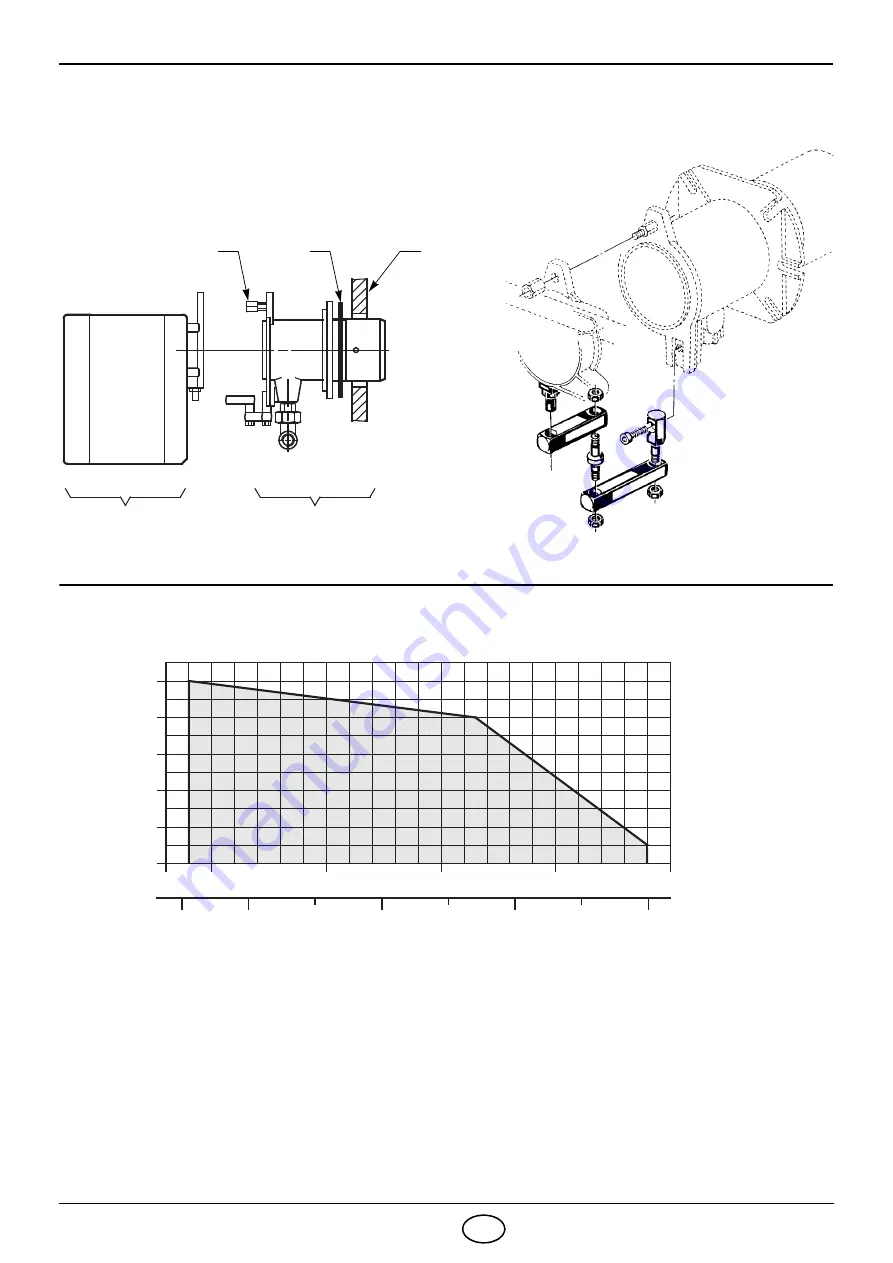
20037556
3
GB
BOILER FIXING
FIRING RATE
TEST BOILER
The firing rate has been defined according to EN 676 standard.
COMMERCIAL BOILERS
The burner-boiler matching is assured if the boiler conforms to EN 303 and the combustion chamber
dimensions are similar to those shown in the diagram EN 676.
For applications where the boiler does not conform to EN 303, or where the combustion chamber
is much smaller than the dimensions given in EN 676, please consult the manufacturers.
Separate the combustion head from the burner body
by removing the nut (1) and pulling back the group
(A)
.
Fix the group
(B)
to the boiler plate (2), inserting the
supplied insulating gasket (3).
1
3
2
A
B
D5067
HINGE ASSEMBLY
S7392
Pressure i
n combus
tion
ch
amber – m
bar
Thermal power
D5135
0.8
0.2
0.4
0.6
20,000
30,000
40,000
50,000
kcal/h
1.0
15,000
0
20
40
30
50
60
kW
16