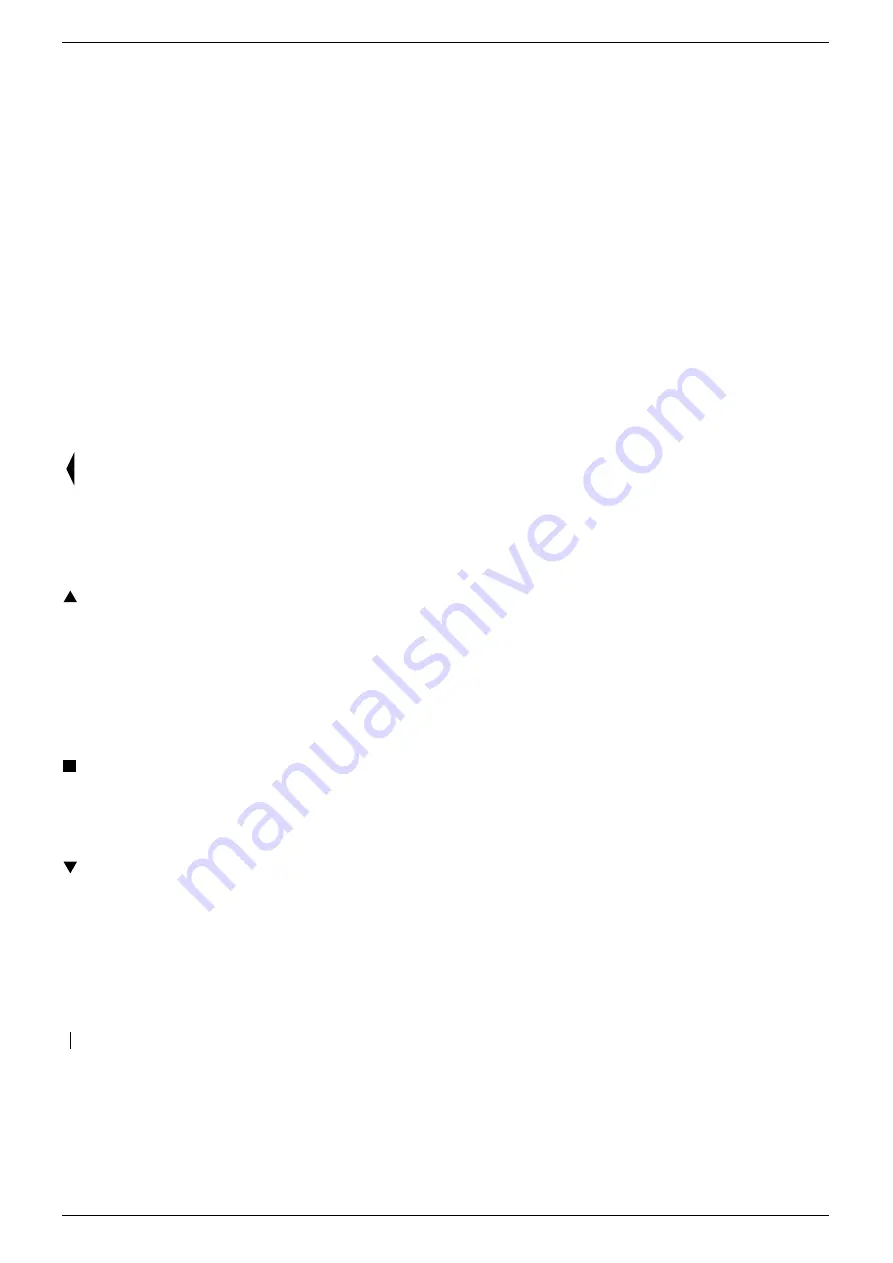
25
OIL OPERATION
At the first ignition, when there is the passage from the first to the second flame, there is a strong decrease of fuel-
pressure owing to the filling of second nozzle pipe. This decrease can cause the burn-out of the burner.
GAS COMBUSTION CHECKS
CO
2
It is better to set the burner with CO
2
not higer than 10% (gas with Pci 8.600 kcal/m
3
). So you avoid that a little unset-
ting (for example draft variation) causes combustion with few air and with the production of CO.
CO
It must be not higher than 100 mg/kWh.
BURNER STARTING DIFFICULTIES AND THEIR CAUSES (GAS)
The control box is fitted with a disk which rotates during the start-up program and can be seen through the release
inspection window. When the burner does not start or stops because of a fault, the symbol which appears in the
inspection window indicates the type of interruption fault.
The control box does not start when the thermostats close:
• there is no gas:
• the min. gas pressure switch does not close the contact: it is incorrectly adjusted;
• the air pressure switch is set in operating position;
• the fuse of the control box has blown;
• the servomotor does not close the circuit, terminals 11 and 8 of the control box.
Halt after start-up:
• the servomotor does not close the circuit, terminals 9 and 8 of the control box.
Lock halt:
The air pressure switch does not effect a selection because of:
• a faulty contact;
• insufficient air pressure.
Lock halt:
Malfunctions of the flame detection circuit:
• photocell exhausted;
• fault internal amplifier.
Pre-ventilation halt:
• the servomotor does not close the circuit, terminals 10 and 8 of the control box.
Lock halt, no flame signal:
• photocell exhausted;
• photocell connection to the control box is interrupted;
• insufficient electrical detection current (min. 70 µA).
Lock halt in operation because of:
• no flame signal;
• no air pressure.
P
1
Summary of Contents for GI/EMME 300
Page 51: ......