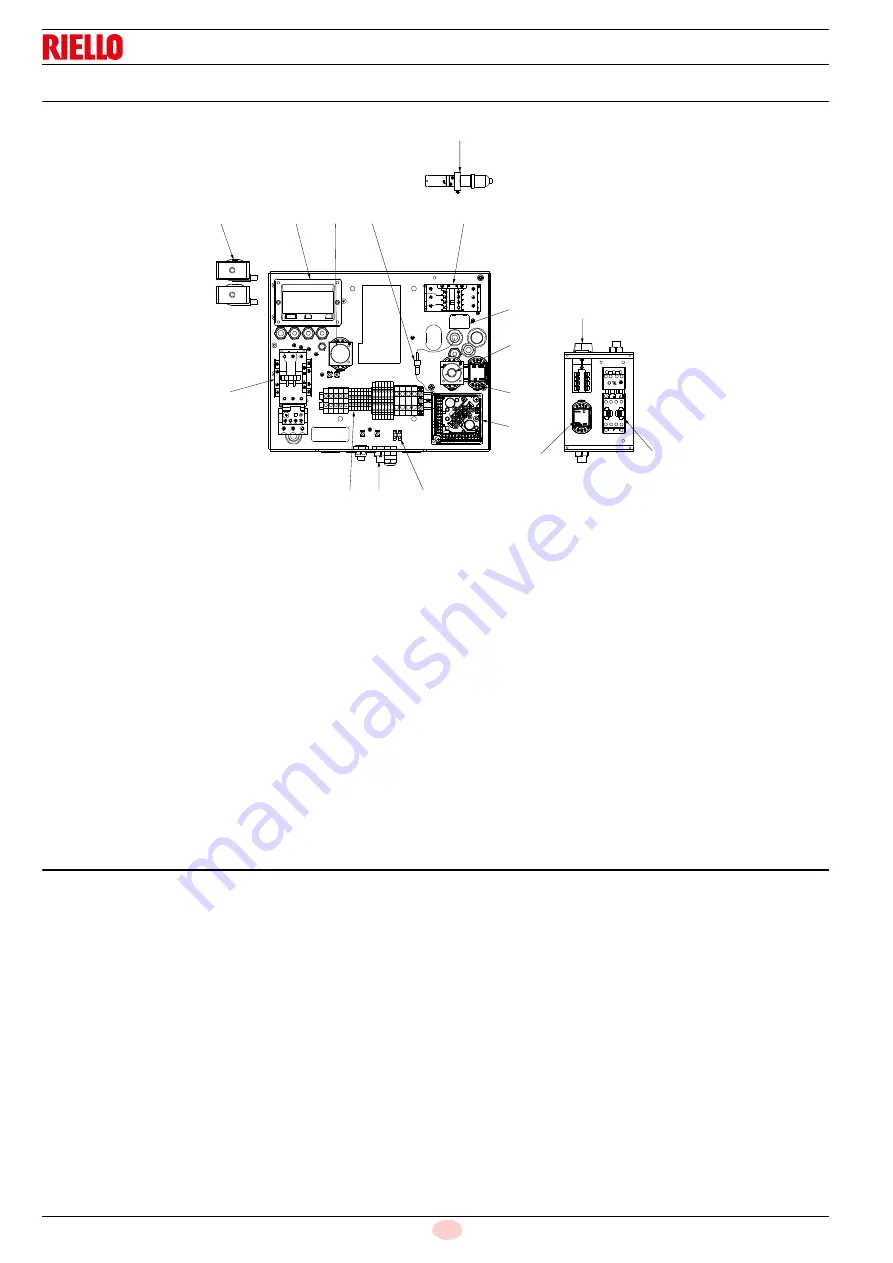
20176605
12
GB
Technical description of the burner
4.10
Electrical panel description
1
Contactor and thermal relay for fan motor (only for direct
start-up)
2
Contactor and thermal relay for pump motor
3
Plug-socket on servomotor cable
4
Resistors contactor
5
Terminal board
6
Relay
7
Time relay
8
Relay
9
Electronic thermostat
10 Control box base
11 Flame sensor
12 Coils for oil valves
13 Suppressor (only for ENNE/EMME 3000-4500 models)
14 Cable grommets for external wirings (to be carried out by
the installer)
15 Ignition transformer
16 Selector switch
OIL-0-GAS
17 Terminal board
4.11
Burner equipment
Seal for gas train . . . . . . . . . . . . . . . . . . . . . . . . . . . . . . . . No. 1
Extensions . . . . . . . . . . . . . . . . . . . . . . . . . . . . . . . . . . . . . No. 2
Screws . . . . . . . . . . . . . . . . . . . . . . . . . . . . . . . . . . . . . . . No. 12
Insulating flange gasket . . . . . . . . . . . . . . . . . . . . . . . . . . . No. 1
Flexible hoses . . . . . . . . . . . . . . . . . . . . . . . . . . . . . . . . . . No. 2
Nipples . . . . . . . . . . . . . . . . . . . . . . . . . . . . . . . . . . . . . . . . No. 2
Cable grommets. . . . . . . . . . . . . . . . . . . . . . . . . . . . . . . . . No. 4
Washers . . . . . . . . . . . . . . . . . . . . . . . . . . . . . . . . . . . . . . . No. 8
Instruction. . . . . . . . . . . . . . . . . . . . . . . . . . . . . . . . . . . . . . No. 1
Spare parts list . . . . . . . . . . . . . . . . . . . . . . . . . . . . . . . . . . No. 1
12
15
1
14
5
10
6
7
13
3
9
4
16
8
2
11
17
Fig. 5
20181970
Summary of Contents for ENNE/EMME 1400
Page 2: ...Translation of the original instructions...
Page 60: ...20176605 58 GB Appendix Electrical panel layout 0 1 1 1 ENNE EMME 1400 2000...
Page 61: ...59 20176605 GB Appendix Electrical panel layout 0 1 1 1 ENNE EMME 3000...
Page 63: ...61 20176605 GB Appendix Electrical panel layout 0 1 2 2 2 0 ENNE EMME 1400 2000...
Page 64: ...20176605 62 GB Appendix Electrical panel layout 0 1 2 2 2 0 ENNE EMME 3000...
Page 65: ...63 20176605 GB Appendix Electrical panel layout 0 1 1 1 ENNE EMME 4500...
Page 66: ...20176605 64 GB Appendix Electrical panel layout 0 ENNE EMME 1400 2000...
Page 67: ...65 20176605 GB Appendix Electrical panel layout 0 ENNE EMME 3000...
Page 68: ...20176605 66 GB Appendix Electrical panel layout 0 1 2 2 2 0 ENNE EMME 4500...
Page 72: ...20176605 70 GB Appendix Electrical panel layout 0 ENNE EMME 4500...