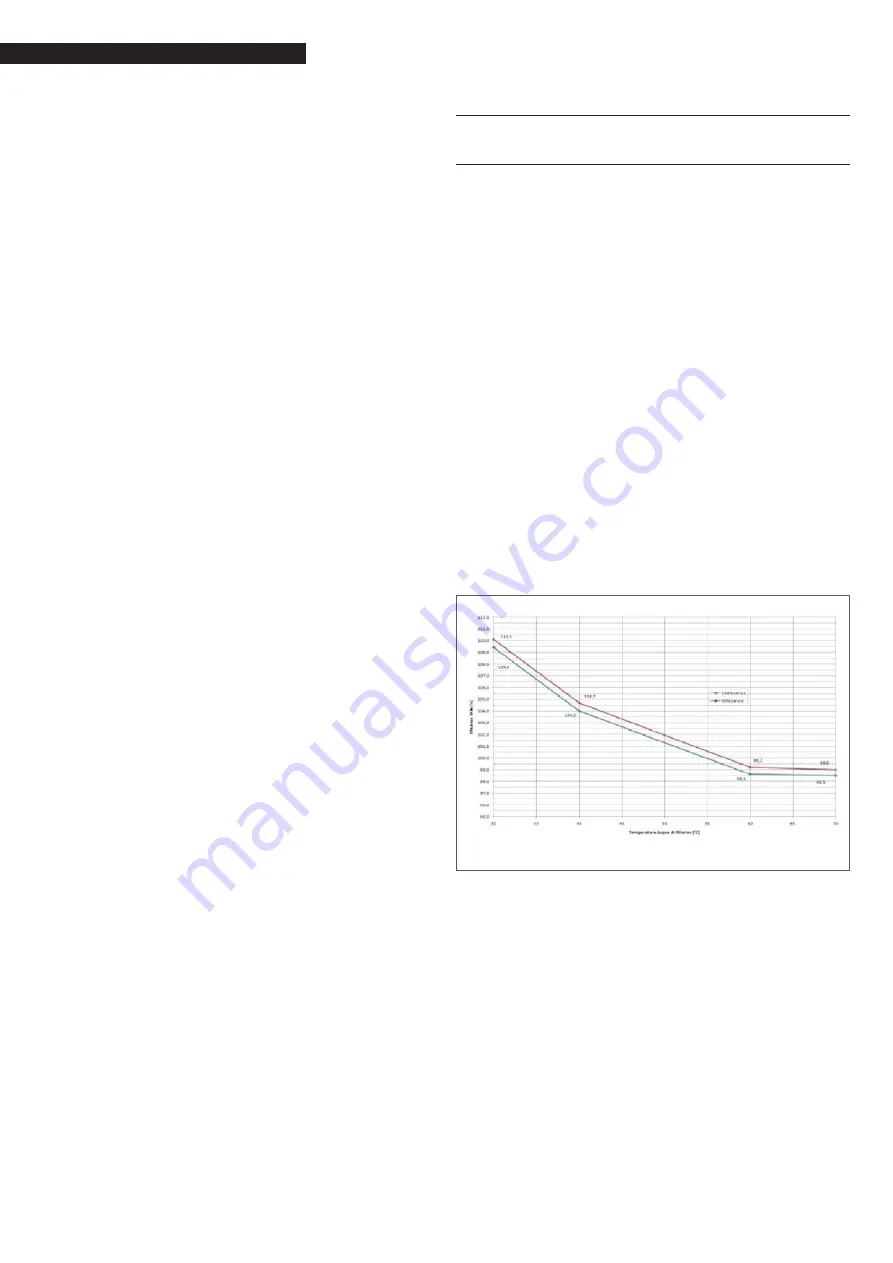
4
TECHNICAL FEATURES
0
It is forbidden to use electrical devices or equipment, such
as switches, appliances, etc. if there is a smell of gas or un-
burnt products. If so:
− ventilate the room, opening doors and windows;
− close the gas valve at the mains;
− immediately call in the Technical Assistance Service or
professionally qualified personnel.
0
It is forbidden to touch the heating unit with bare feet or
parts of the body wet.
0
It is forbidden to start on any technical or cleaning jobs be-
fore disconnecting the heating unit from the power mains.
0
It is forbidden to alter the safety and adjustment devices
without permission and instructions from the heating unit
manufacturer.
0
It is forbidden to obstruct the condensate drain.
0
It is forbidden to pull, detach, twist the wiring coming out of
the heating unit, even if unplugged from the power supply.
0
It is forbidden to obstruct or reduce the size of air vents.
0
It is forbidden to expose the boiler to atmospheric agents (if
it is not a specific unit for outdoors).
0
It is forbidden to leave containers or flammable substances
in the premises where the boiler is installed.
0
Do not dispose of packaging material into the environment,
or leave it within the reach of children, since it can become
a potential hazard. Dispose of packaging material in com-
pliance with applicable legislation.
0
The user is forbidden to open the cupboard containing the
heating unit. Any jobs on the inside of the latter must be
done by the Technical Assistance Service or by qualified per-
sonnel.
0
It is forbidden to discard the product as household waste.
At the end of its service life, it can be consigned to specif-
ic selected waste centres provided by the local authorities
or else to dealers providing this service. Disposing of a do-
mestic appliance separately will prevent possible harmful
consequences for environment and health derived from
inappropriate disposal, likewise making it possible to recu-
perate the materials it is made of with substantial savings in
energy and resources.
3
TECHNICAL FEATURES
3.1
Main features
Condexa Pro3 IN-EXT
is a condensing, modular, pre-mixed,
blown, thermal group; it is made up of a series of
Condexa Pro3
IN-EXT
thermal elements installed in battery.
A unit is made of N° 2, 3 or 4 heat exchangers, each with a mod-
ulating power from 23 ti 115 kW; equipped with climatic regula-
tion and RS485 connection. Each device can be serially matched
up with same tipe units up to a total installed power of 3680
kW (eight
Condexa Pro3 IN-EXT
equal to a total of di 32 heat
exchangers).
9
In case of installation of more than 32 unit (up to 60 unit)
please contact
R
Technical Assistance Service.
It is possible to connect up two thermal groups (with a total of 8
heat exchangers) directly using the internal 5” hydraulic mani-
folds and the internal 3” gas manifold.
The efficiency of the generators reaches 109% based on the low-
er heat potential of natural gas (Hi) making it possible to use a
flue manifold entirely made of plastic (PP). The system also en-
ables continual modulation of the gas and combustion air flow.
The
Condexa Pro3 IN-EXT
heating unit is the optimum as far as
operating costs (up to 109% efficiency per Hi, see Figure 1) reli-
ability and flexibility. In fact, thanks to the new heat exchang-
er with improved power, to the new electronic management,
to the modularity and versatility, it is possible to make a rapid
connection to any kind of heating system and storage hot water
production.
Figure 1
The insertion of a single thermal element in cascade, over the
traditional rotation of the ignition, can take place with
variable
factor of heating power load
, so that when a certain power
percentage of the first element is reached (e.g. 30%), the suc-
cessive element already starts with the same load factor. This
latter feature allows to share the power supplied inside more
than one heat exchangers with a power/exchange surface ratio
which is particularly favourable for condensation latent heat.
Summary of Contents for Condexa Pro3 230 IN V02
Page 1: ...cod 20060249 rev 10 12 2015 Condexa Pro3 230 345 460 IN EXT EN INSTALLATION INSTRUCTIONS...
Page 36: ...36 WIRING DIAGRAMS 12 WIRING DIAGRAMS...
Page 37: ...37 WIRING DIAGRAMS Valvola 2 vie Circolatore...
Page 42: ...42 WATER IN CENTRAL HEATING SYSTEMS...