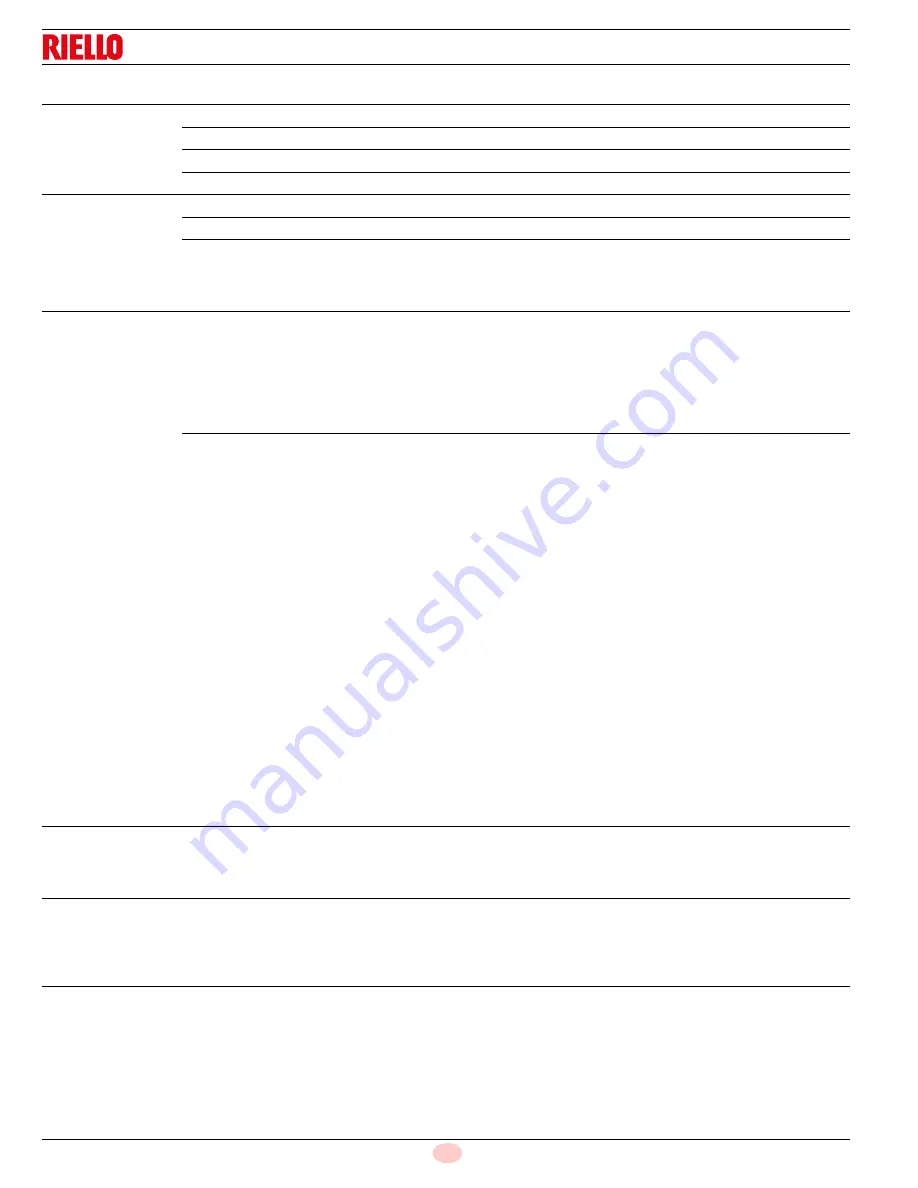
20044359
12
GB
Technical description of the burner
Technical data
LMV37.4... basic unit Mains voltage
AC 120 V -15 % / +10 %
Mains frequency
50 / 60 Hz ±6 %
Power consumption
< 30 W (typically)
Safety class
I, with parts according to II and III to DIN EN 60730-1
Terminal loading
‘Inputs’
Unit fuse F1 (internally)
6.3 AT
Perm. mains primary fuse (externally)
Max. 16 AT
Undervoltage
•
Safety shutdown from operating position
at mains voltage
•
Restart on rise in mains voltage
Approx. AC 93 V
Approx. AC 96 V
Terminal loading
‘Outputs’
Total contact loading:
•
Nominal voltage
•
Unit input current (safety loop) from:
- Fan motor contactor
- Ignition transformer
- Valves
- Oil pump / magnetic clutch
AC 120 V, 50 / 60 Hz
Max. 5 A
Individual contact loading:
Fan motor contactor
•
Nominal voltage
•
Nominal current
•
Power factor
AC 120 V, 50 / 60 Hz
1.6 A pilot duty load declaration to UL372
cos
> 0.4
Alarm output
•
Nominal voltage
•
Nominal current
•
Power factor
AC 120 V, 50 / 60 Hz
1 A
cos
> 0.4
Ignition transformer
•
Nominal voltage
•
Nominal current
•
Power factor
AC 120 V, 50 / 60 Hz
1.6 A pilot duty load declaration to UL372 or 250 VA ignition
load declaration to UL372
cos
> 0.2
Fuel valves
•
Nominal voltage
•
Nominal current
•
Power factor
AC 120 V, 50 / 60 Hz
1.6 A pilot duty load declaration to UL372
cos
> 0.4
Operation display
•
Nominal voltage
•
Nominal current
•
Power factor
AC 120 V, 50 / 60 Hz
0.5 A
cos
> 0.4
Cable lengths
Mains line
Display, BCI
External lockout reset button
Max. 100 m (100 pF/m)
For used outside the burner cover or the control panel:
Max. 3 m (100 pF/m)
Max. 20 m (100 pF/m)
Environmental
conditions
Operation
Climatic conditions
Mechanical conditions
Temperature range
Humidity
DIN EN 60721-3-3
Class 3K3
Class 3M3
-20...+60 °C
< 95 % r.h.