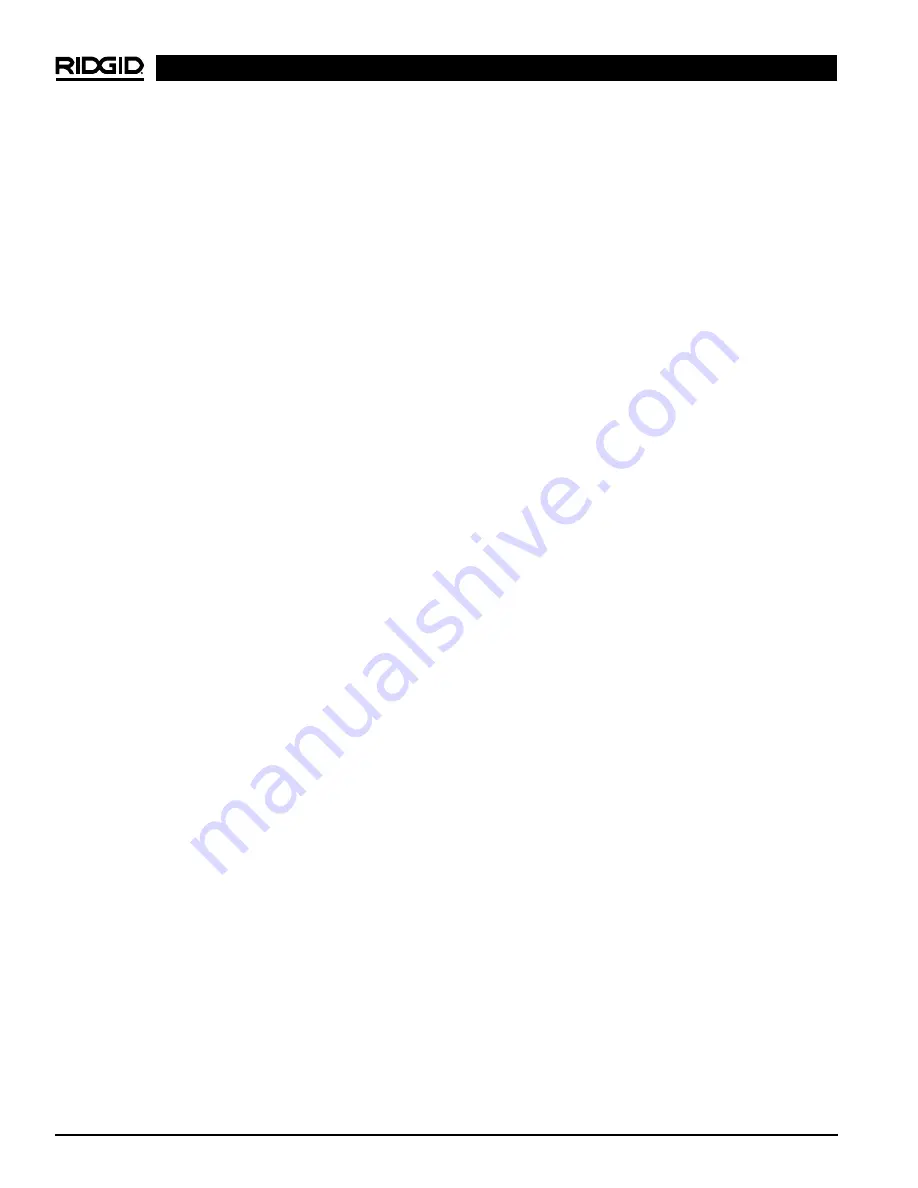
Service and Repair
The above section “Cleaning and Maintaining this Tool”
will take care of most of the service needs of this tool
with the exception of main bearing replacement. Any
problems not addressed by the “Cleaning and
Maintaining this Tool” section or replacement of this
bearing should only be handled by an authorized
RIDGID service technician.
If any maintenance is required other than that outlined, the
tool should be sent to a RIDGID Independent Authorized
Center or returned to the factory. All repairs made by
Ridge service facilities are warranted against defects in
material and workmanship.
RT3422 Tapping Tool
Ridge Tool Company
12