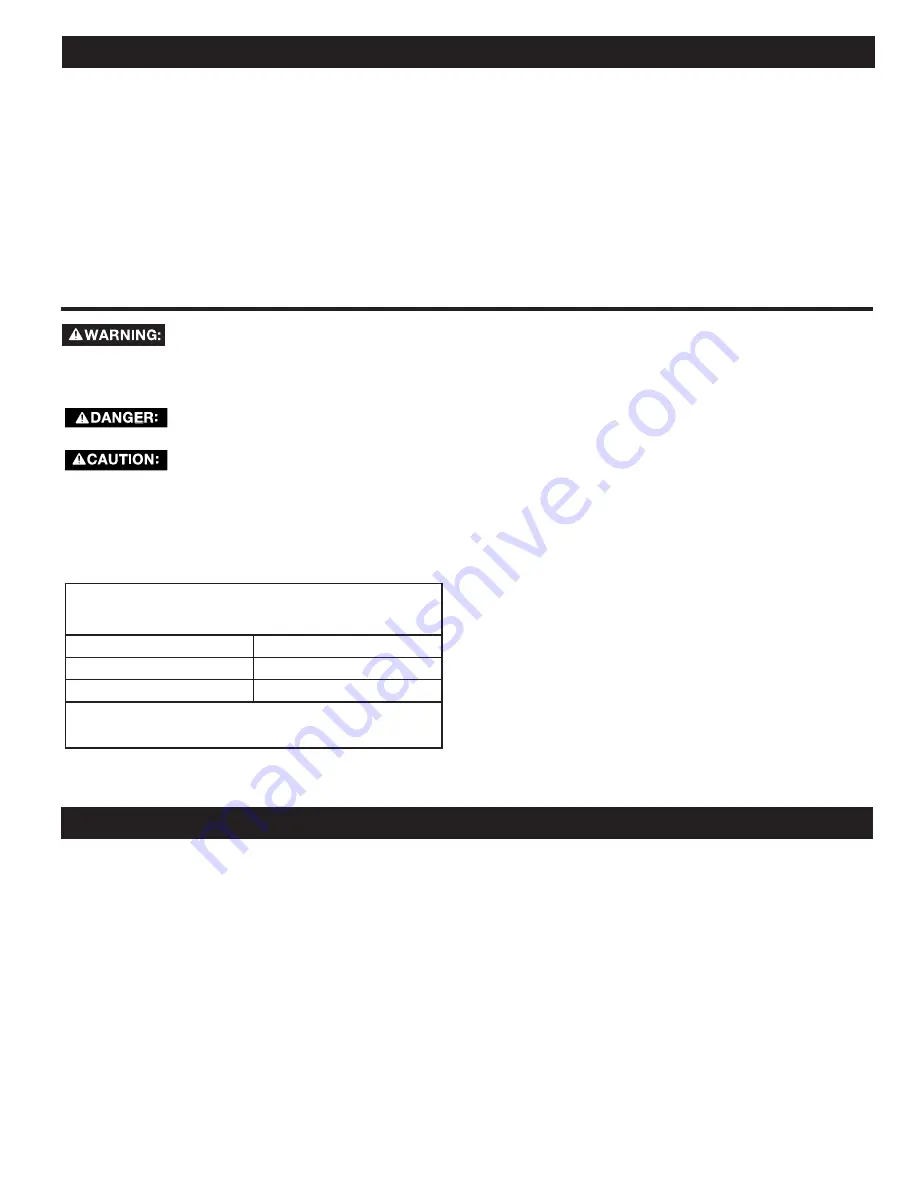
POWER CONNECTIONS
POWER SOURCE
This saw is equipped with a 15-amp motor for use with a 120-
volt, 60-HZ alternating current.
For voltage, the wiring in a shop is as important as the motor’s
rating. A line intended only for lights may not be able to properly
carry the current needed for a power tool motor; wire that is
heavy enough for a short distance may be too light for a greater
distance; and a line that can support one power tool may not be
able to support two or three. A separate electrical circuit should
be used for your machines. This circuit should not be less than
#12 wire and should be protected with a 20-amp time lag fuse
and/or circuit breaker. If an extension cord is used, use only
3-wire extension cords which have 3-prong grounding-type
plugs and matching receptacle which will accept the machine’s
plug. Before connecting the machine to the power line, make
sure the switch(es) is in the “OFF” position and be sure that the
electric current is of the same characteristics as indicated on the
machine. A substantial voltage drop will cause a loss of power
and overheat the motor. It may also damage the machine.
DO NOT EXPOSE THE MACHINE TO RAIN OR OPERATE THE MACHINE IN DAMP LOCATIONS.
EXTENSION CORDS
** Ampere rating (on tool data label)
12A- 16A
Cord Length
Wire Size
25'
14 AWG
50'
12 AWG
** Used on 12 gauge - 20 amp circuit
NOTE: AWG = American Wire Gauge
KEEP
the extension cord clear of the work area. Position the cord so it will not get caught on lumber, tools or other
obstructions
•
Use proper extension cords. Make sure your extension cord is a 3-wire extension cord which has a 3-prong grounding type plug and
matching receptacle which will accept the machine’s plug. When using an extension cord, be sure to use one heavy enough to carry
the current of the machine. An undersized cord will cause a drop in line voltage, resulting in loss of power and overheating. The
table below shows the maximum gauge to use depending on the cord length. If in doubt, use the next heavier gauge. The smaller
the gauge number, the heavier the cord. ONLY round, jacketed cords listed by Underwriter’s Laboratories (UL) should be used.
NEVER
use a damaged extension cord. Check extension cords before each use. If damaged, replace immediately.
Touching the damaged area could cause electrical shock resulting in serious injury.
• Prior to tool assembly and use, read this manual thoroughly
to familiarize yourself with proper assembly, maintenance and
safety procedures.
Check shipping carton and machine for damage before unpacking.
Carefully remove components in top foam layer. Remove the top
layer of foam then remove all components in the bottom layer of
foam. Lay out all parts on a piece of cardboard or other clean,
flat surface. Two or more people are needed to lift the saw out of
the carton. ALWAYS check for and remove protective shipping
materials around motors and moving parts. DO NOT discard
shipping carton and packing materials until you have carefully
inspected the contents, assembled the machine and are satisfied
that it operates correctly.
Compare package contents to Component Parts List and
Hardware Package List prior to assembly to make sure all items
are present. Carefully inspect parts to make sure no damage
occurred during shipping. If any parts are missing, damaged or
pre-assembled, do not assemble. Instead, call RIDGID
®
Customer
Service at (toll free) 1-888-359-4778.
After assembly remove any protective materials and coatings from
all of the parts and the table saw. The protective coatings can be
removed by spraying WD-40
®
on them and wiping them off with a
soft cloth. This may need to be redone several times before all of
the protective coatings are removed completely.
UNPACKING
9