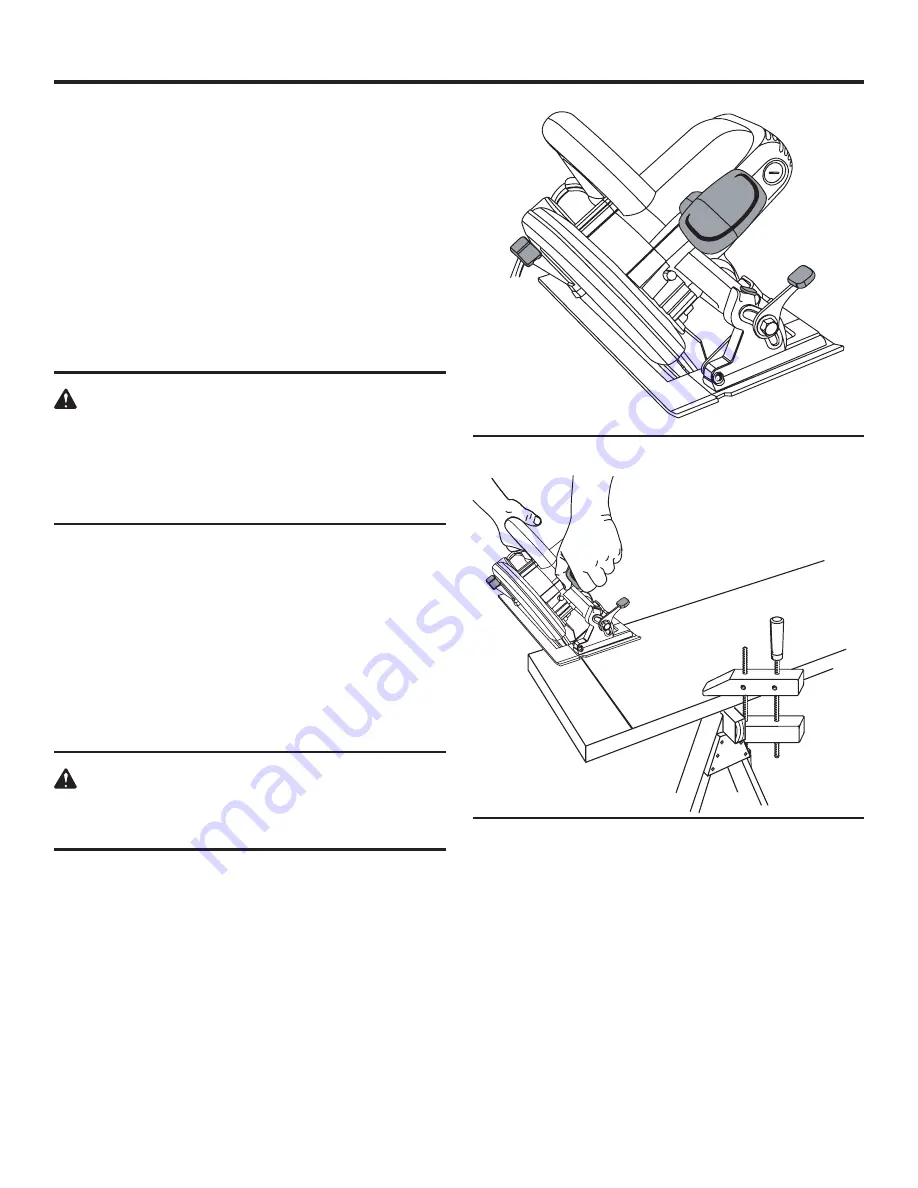
17
BEVEL CUTTING
See Figures 17 and 18.
To make the best possible cut, follow these helpful hints.
Align the line of cut with the inner blade guide notch on
the base when making 45
°
bevel cuts.
Make a trial cut in scrap material along a guideline to
determine how much you should offset the guideline on
the cutting material.
Adjust the angle of the cut to any desired setting between
zero and 51.5
°
. Refer to "TO ADJUST BEVEL SETTING"
next.
NOTE:
Pull the adjustment lever all the way up to set the
angle at 51.5
°
.
WARNING:
The tool should never be connected to a power
supply when you are assembling parts, making
adjustments, cleaning, performing maintenance, or
when the tool is not in use. Disconnecting the tool
will prevent accidental starting that could cause
serious injury.
TO ADJUST BEVEL SETTING
See Figure 17.
Follow these directions to adjust the bevel setting.
Unplug the saw.
Pull the bevel adjustment lever upward until the motor
housing moves freely.
Raise motor housing end of saw until you reach the de-
sired angle setting on bevel scale.
Press downward on the bevel adjustment lever until the
motor housing is securely locked in place.
WARNING:
Attempting a bevel cut without having the bevel
adjustment lever securely locked in place can
result in serious injury.
TO BEVEL CUT
See Figure 18.
Follow these directions to bevel cut.
Hold the saw firmly with both hands as shown.
Rest the front edge of the base on the workpiece.
Start the saw and let the blade reach full speed.
Guide the saw into the workpiece and make the cut.
Release the trigger and allow the blade to come to a
complete stop.
Lift the saw from the workpiece.
OPERATION
Fig. 18
Fig. 17