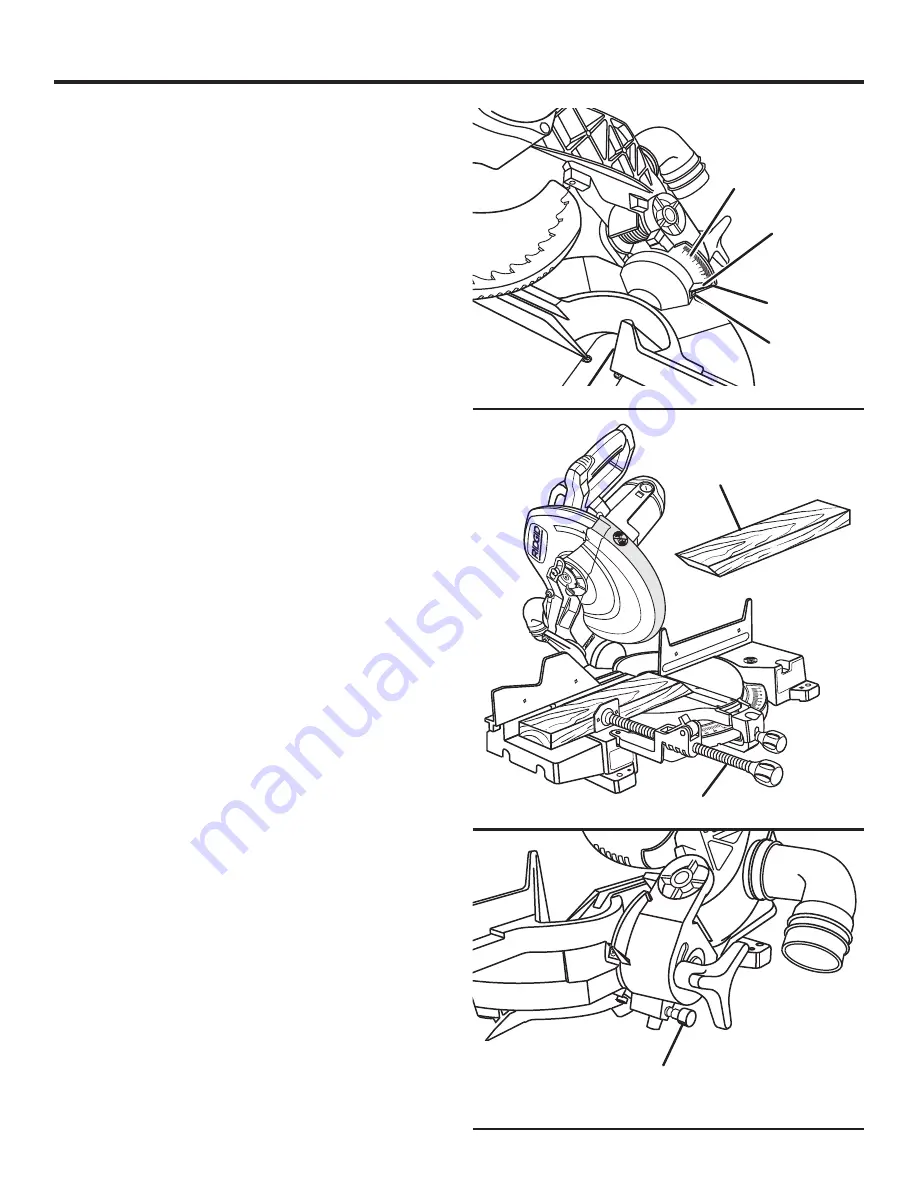
4
TO BEVEL CUT
See Figures 27 - 29.
A bevel cut is made by cutting across the grain of the
workpiece with the blade angled to the workpiece. A straight
bevel cut is made with the miter table set at the zero degree
position and the blade set at an angle between -
°
and 47
°
.
NOTE:
It may be necessary to adjust the sliding miter fence
to assure proper clearance prior to making the cut.
Pull out the lock pin and lift saw arm to its full height.
Loosen the miter lock handle. Rotate the miter lock han-
dle approximately one-half turn to the left to loosen.
Press the miter lock plate down with your thumb and
hold.
Rotate the miter table until the pointer aligns with zero
on the miter scale.
Release the miter lock plate.
NOTE:
You can quickly locate zero by releasing the lock
plate as you rotate the control arm. The lock plate will seat
itself in one of the built-in positive stop notches, located
in the miter table frame.
Tighten the miter lock handle securely.
Loosen the bevel lock knob and move the saw arm to
the left to the desired bevel angle.
Bevel angles can be set from -
°
to 47
°
.
Once the saw arm has been set at the desired angle,
securely tighten the bevel lock knob.
Place the workpiece flat on the miter table with one edge
securely against the fence. If the board is warped, place
the convex side against the fence. If the concave edge
of a board is placed against the fence, the board could
collapse on the blade at the end of the cut, jamming the
blade.
See Figures 34 - 35.
When cutting long pieces of lumber or molding, support
the opposite end of the stock with a roller stand or with
a work surface level with the saw table.
See Figure 32.
Align the cutting line on the workpiece with the edge of
saw blade.
Grasp the stock firmly with one hand and secure it against
the fence. Use the work clamp or a C-clamp to secure
the workpiece when possible.
See Figure 30.
Before turning on the saw, perform a dry run of the cutting
operation just to make sure that no problems will occur
when the cut is made.
Grasp the saw handle firmly. Depress the switch lock
with thumb then squeeze the switch trigger. Allow several
seconds for the blade to reach maximum speed.
Fig. 9
bevel
scale
scale
inDicator
Fig. 7
Fig. 8
OPERATION
®
bevel cut
worK claMp
bevel
stop pin
0
15
30
CM
45
inDicator
point
inDicator
screw