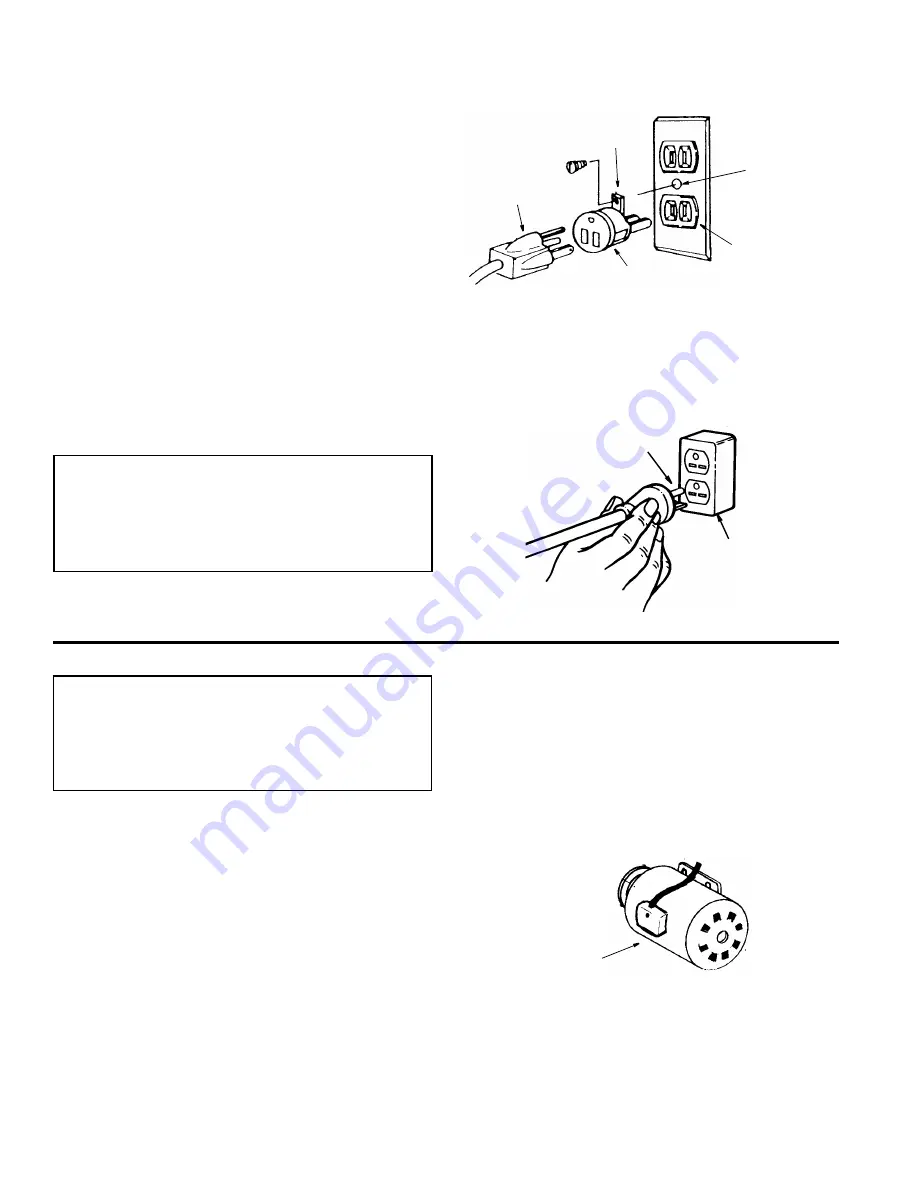
8
Motor Specifications and Electrical Requirements (continued)
Do not modify the plug provided. If it will not fit the outlet,
have the proper outlet installed by a qualified electrician.
A temporary adapter may be used to connect this plug to
a 2-pole outlet, as shown. This temporary adapter should
be used only until a properly grounded outlet can be
installed by a qualified electrician. The green colored
rigid ear, lug and the like, extension from the adapter
must be connected to a permanent ground such as a
properly grounded outlet box.
Improper connection of the equipment grounding con-
ductor can result in a risk of electric shock. The conduc-
tor with insulation having an outer surface that is green
with or without yellow stripes is the equipment grounding
conductor. If repair or replacement of the electric cord or
plug is necessary, do not connect the equipment-ground-
ing conductor to a live terminal.
If the grounding instructions are not completely under-
stood, or if you are in doubt as to whether the tool is prop-
erly grounded check with a qualified electrician or service
personnel.
WARNING: If not properly grounded, this tool can
cause an electrical shock, particularly when used
in damp locations, in proximity to plumbing, or out
of doors. If an electrical shock occurs there is the
potential of a secondary hazard, such as your
hands contacting the knives.
110-120 Volt, 60 Hz. Tool Connections
NOTE: The adapter illustrated is for use only if you already
have a properly grounded 2-prong outlet.
NOTE: In Canada the use of a temporary adapter is not
permitted by the Canadian electrical code.
220-240 Volt, 60 Hz. Tool Connections
Changing Motor Voltage
WARNING: If not properly grounded, this tool can
cause an electrical shock, particularly when used
in damp locations, in proximity to plumbing, or out
of doors. If an electrical shock occurs there is the
potential of a secondary hazard, such as your
hands contacting the knives.
NOTE: The jointer is prewired at the factory for 120V
operation. Use the following procedure to change motor
voltage. To change to 240V application an additional wire
nut is supplied from the factory. This part is included in
the loose parts.
1. Open the motor junction box cover located on the side
of the motor.
2. Cut off the 120 volt power cord plug and replace it with
a (3 blade) 240 volt 15 amp U.L. listed plug. (See illus-
tration of 240V plug & receptacle.) Connect the power
cord white and black leads, respectively, to the “hot”
plug blade terminals and connect the power cord
green grounding wire to the plug ground prong termi-
nal.
3. Remove and discard the electrical tape from the wire
nuts. Remove wire nuts.
4. Reconnect the leads as shown in the “Wiring Diagram”
section at the rear of manual.
5. Reinstall the wire nuts and wrap with two layers of new
U.L. listed electrical tape per wire nut.
6. Recheck your wiring to the wiring diagrams. Do this so
you can be sure that the wiring is correct.
7. Reinstall the junction box cover.
3-Prong
Adapter
2-Prong
Outlet
Make Sure This
Is Connected
Ground
Plug
Green
to a Known
Grounding Lug
Grounding
Prong
Grounded
Outlet Box
Junction
Box Cover