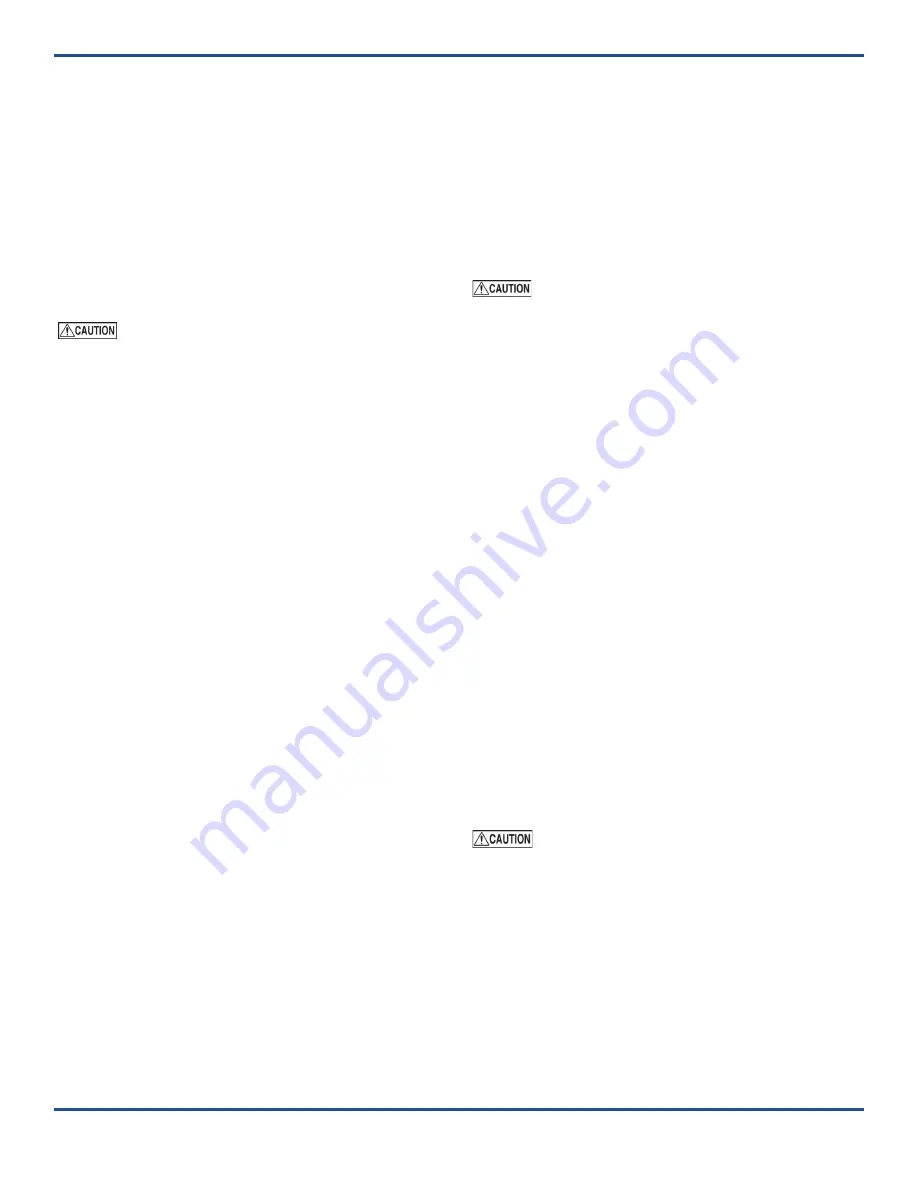
ENG Page 6
215T-Trailer-ISM-RevC-06-06-18
Mounting the suspension to the frame
Refer to the engineering drawing for the range of ride
heights available and clearance requirements .
The suspension installer has the final responsibility
of attaching the suspension to the vehicle frame.
Weld-On Installation Procedure
Recommended locations of customer-furnished filler
plates and supporting crossmembers for the hang-
ers and air spring mounting plates are shown on the
engineering drawing.
Welding method must use a minimum weld
tensile strength of 70,000 psi, per AWS specifications.
1.
Mark desired location of the hangers and filler
plates on the frame. Hangers must be installed
parallel to each other for proper axle alignment.
2. Mark the desired location of the air spring
mounting plates and filler plates on the frame.
NOTE: Protect other chassis components from
weld spatter during installation, if necessary.
3.
Install filler plates for the hangers and air spring
mounting plates on the frame. Weld filler plates
to crossmembers with ¼” fillet welds down the
length of the crossmember.
4.
Weld the hangers to the frame/filler plates with
1/4” fillet welds completely around the hangers.
Stop the welds 1/2” from the corners and edges.
5. Weld the air spring mounting plates to the frame/
filler plates with 3/16” fillet welds.
6.
Attach a crossmember or diagonal brace to the
front of the hangers with 1/4” fillet welds.
Bolt-On Installation
Before installation, check to make sure that wires,
hoses or other components will not be affected by
drilling into the frame rail.
•
Bolts/nuts for attaching the suspension to the
vehicle are supplied by the installer. Grade 8 bolts
and flanged lock nuts or lock nuts with hardened
washers are recommended.
• Bolt holes are not provided in the air spring
mounting plates. Clamp mounting plates and
filler plates, if used, in place and drill (minimum)
two bolt holes in each mounting plate for installa-
tion onto the chassis.
Shock Absorber Kit (Optional)
The shock absorber can be installed after the suspen-
sion has been assembled and mounted on the vehicle.
Installation Procedure
Refer to the shock kit engineering drawing for the
correct mounting locations and installation angles for
the upper and lower mounting brackets on individu-
al RCA-215 suspension models.
Welding method for lower mounting bracket
must use a minimum weld tensile strength of 70,000
psi, per AWS specifications.
1. Disconnect and remove the load springs from the
suspension assembly. Protect the lift springs from
welding spatter.
2. Remove the upper air spring mounting brackets.
3. Weld replacement upper air spring mounting
brackets provided in shock absorber kit to frame
crossmember with 3/16” fillet weld.
4. Measure the shock absorber to axle (lower)
mounting bracket location from the edge of the
axle seat, not from the axle weld. Clamp the
bracket into place. Use a 5/16” fillet weld to weld
the lower mounting bracket to the axle at the
forward and rear edge only. Do not weld perpen-
dicular to the axle centerline.
5.
Attach the shock absorbers to mounting brackets.
with supplied HHCS and lock nut. Torque lock
nut to 160-200 ft-lb (
217-271 N-m)
.
6.
Install load springs. Torque to specifications (Ap
-
pendix). Connect load springs to air system.
7. Raise and lower suspension to make sure that
shock absorbers clear air spring mounting plates
and that shock absorbers do not overextend.
Failure to torque bolts/nuts of suspension
components to specifications can result in failure of
the suspension and void the warranty.