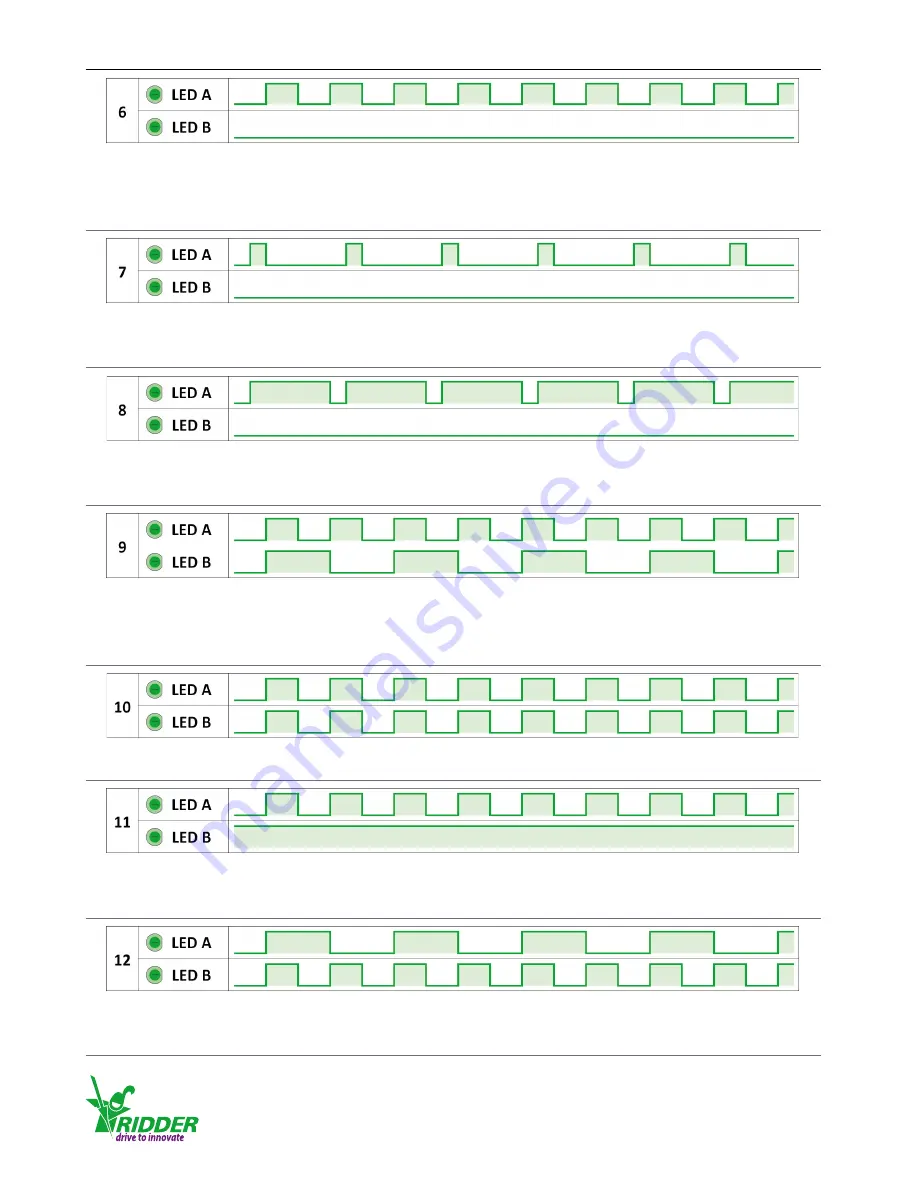
Ridder Drive Systems
T
+31 (0)341 416 854
F
+31 (0)341 416 611
I
www.ridder.com
22
Blink code / Meaning
● Operating mode: A mechanical overload has been detected. The RLD80 can no longer be
operated in the rotational direction where the overload has occurred. However, you can
reverse the rotational direction of the RLD80.
● Operating mode: 10 minor mechanical overloads have been detected. This has caused the
RLD80 to stop. Disconnect the supply voltage to reset the RLD80.
● Operating mode: 10 major mechanical overloads have been detected. This has caused the
RLD80 to stop. Disconnect the supply voltage to reset the RLD80.
● Operating mode: End positions A and B have not been taught in yet.
● Teach-in mode: End position B (the RLD80 is in this end position) has been programmed; end
position A has not yet been programmed.
● Teach-in mode: End positions A and B have not been taught in yet.
● Teach-in mode: End position B (the RLD80 is not in this end position) has been programmed;
end position A has not yet been programmed.
● Teach-in mode: End position A (the RLD80 is in this end position) has been programmed; end
position B has not yet been programmed.
Summary of Contents for LogicDrive RLD80
Page 28: ...www ridder com...