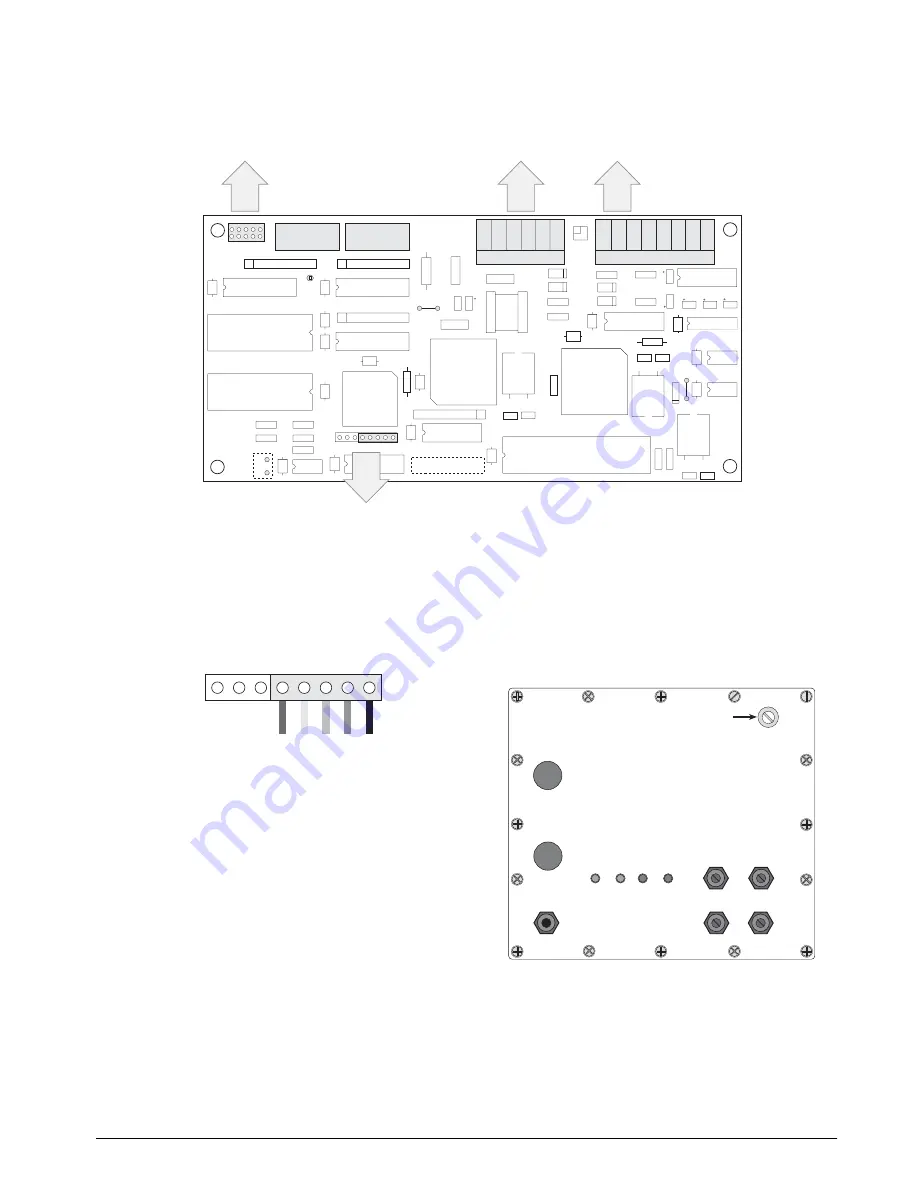
Installation
3
Figure 2-1. Remote I/O Interface Board
16. Plug LED annunciator cable plug into
connector J3 on the Remote I/O Interface
board. Ensure the black wire of the 5-pin
cable plug is attached to pin 1 on the J3
connector (see Figure 2-2).
Figure 2-2. LED Cable Plug on J3 Connector
17. Feed Allen-Bradley network cable through
cord grip. Allow enough cable for routing
along inside of enclosure to J5 connector on
the Remote I/O Interface board. Connect
Allen-Bradley network cables into connector
J5 on the Remote I/O Interface board as
described in Section 2.2.4 on page 6.
18. Use three cable ties to secure the LED and
Allen-Bradley network cables to the cable tie
mounts attached in step 9.
19. Set termination resistance (jumper JU-1) as
described in Section 2.2.2 on page 6.
20. Set DIP switches as described in Section 2.3
2.1.4
Reassemble Enclosure
21. Position the backplate over the enclosure and
reinstall the backplate screws. Use the torque
pattern shown in Figure 2-3 to prevent
distorting the backplate gasket. Torque screws
to 15 in-lb (1.7 N-m).
Figure 2-3. IQ plus 510/710/Remote I/O Backplate
C11
C10
R6
R5
X2
X3
U7
C20
D1
U15
C6
C26
C25
C15
C14
C13
C12
U9
C16
1
J4
R11
R17
D2
D3
R12
R14
D4
D5
T1
1
J6
J5
1
R18
R13
C28
C27
U13
C9
C8
U14
C23
C4
X1
U10
C18
U16
U17
C17
J2
C19
U1
C29
JU1
SW1
SW2
1
1
RSIP2
RSIP1
RSIP3
U12
J1
C24
U11
C7
C5
C3
U6
U2
C1
C22
U5
C2
U4
R8
R7
R16
R3
R1
U3
J3
C21
R15
R9
2
3
1
P / N
R10
1
2
10
9
LED CONNECTOR
1
82
Ω
150
Ω
3
2
4
U8
C30
R4
R2
GND
GND
5V TEST
1
1
1
1
RS-232 TxD
RS-232 RxD
RS-232 GND
N/C
20mA +IN
20mA –IN
20mA +OUT
20mA –OUT
CLEAR
BLUE
SHIELD
CLEAR
BLUE
SHIELD
RESET
Power supply connection to
J15 on indicator CPU board
Allen-Bradley Network
connections
Indicator connections
to J4 on indicator CPU board
DIP switches
Backplate LED connections
J3
LED CONNECTOR
1
BLACK
GREEN
RED
YELLOW
ORANGE
S e t u p s w i t c h a c c e s s s c r e w
Fillister head screws
1
To r q u e b a c k p l a t e s c r e w s
t o 1 0 i n - l b ( 1 . 1 3 N - m )
2
3
4
5
6
7
8
9
10
11
16
12
13
14
15
TxD
RxD
RIO
POWER
DISCONTINUED