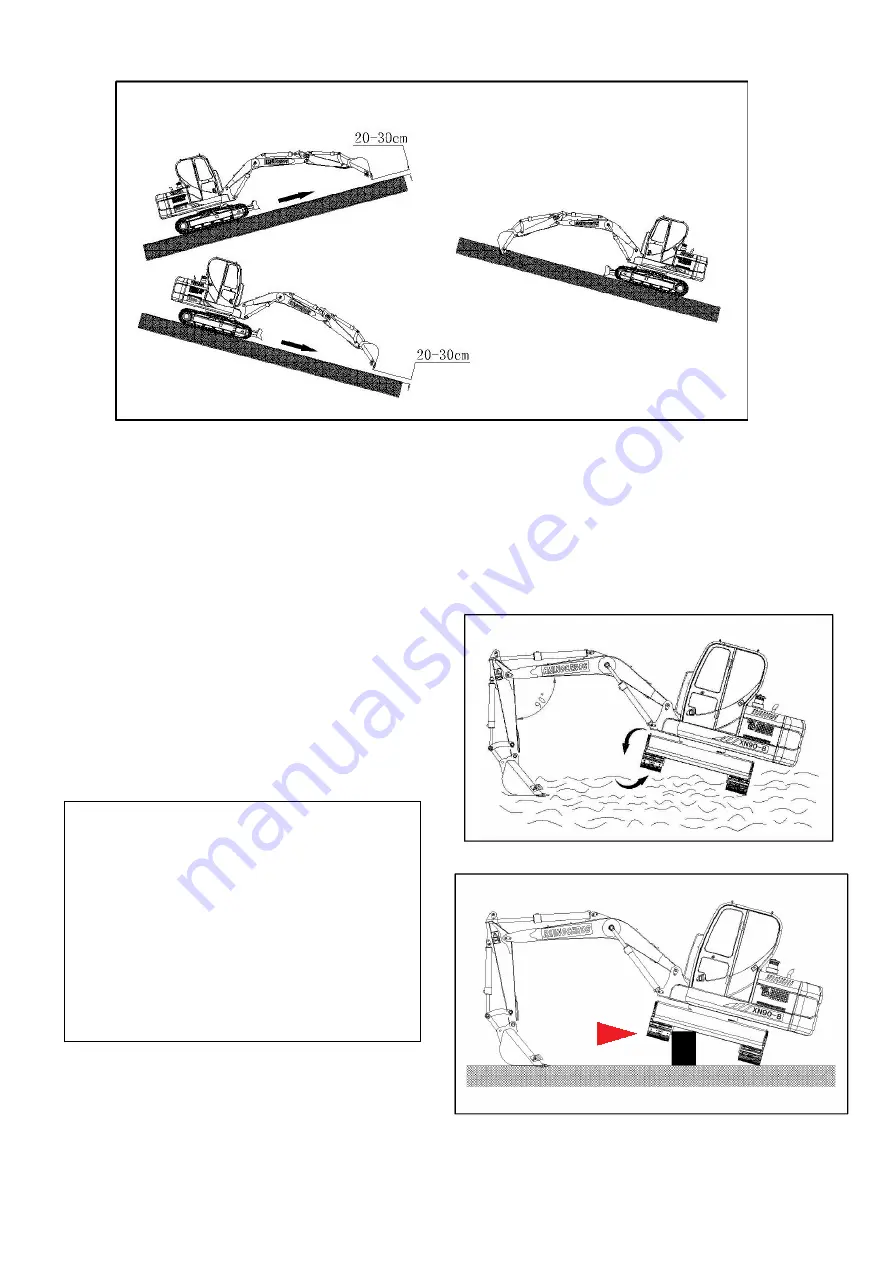
Fig 3-31
8. Walking along the slope, do not walk across the slope.(Fig 3-31),pull out of the bucket
rod, lowering the boom,keep the bucket a 300mm distance from the ground, if the machine
sliding or unstable, put down the bucket to keep control.If the engine stopped, low down
the bucket,make sure all handle at the middle position before restart the engine.
9. If there is dust or sands on the trak shoe,
lift the two track shoes and turn to clear it.
Make sure the sludge is cleared.
( Fig3-32 Fig 3-33)
Fig 3-32
Fig 3-33
▲ WARNING
If to support any part of the excavator by
boom or arm, swing the bucket to make sure
the under part of the bucket touch ground, and
the angle between boom and arm should be
90 degree
。
48
Summary of Contents for XN80-E
Page 20: ...12 Radio Refer to the sound...
Page 44: ......
Page 45: ......
Page 46: ...X N 9 0 8 X N 9 0 8 X N 9 0 8...
Page 51: ...X N 9 0 8 X N 9 0 8 X N 9 0 8 X N 9 0 8 X N 9 0 8 X N 9 0 8 X N 9 0 8 X N 9 0 8 X N 9 0 8...
Page 53: ...X N 9 0 8 X N 9 0 8 X N 9 0 8 X N 9 0 8 X N 9 0 8 X N 9 0 8...
Page 54: ...X N 9 0 8 X N 9 0 8 X N 9 0 8...
Page 55: ...X N 9 0 8 X N 9 0 8 X N 9 0 8 X N 9 0 8 X N 9 0 8 X N 9 0 8...
Page 56: ...X N 9 0 8 X N 9 0 8 X N 9 0 8 X N 9 0 8 X N 9 0 8 X N 9 0 8...
Page 57: ...X N 9 0 8 X N 9 0 8 X N 9 0 8 X N 9 0 8 X N 9 0 8 X N 9 0 8...
Page 58: ...X N 9 0 8 X N 9 0 8 X N 9 0 8 X N 9 0 8 X N 9 0 8 X N 9 0 8...
Page 59: ......