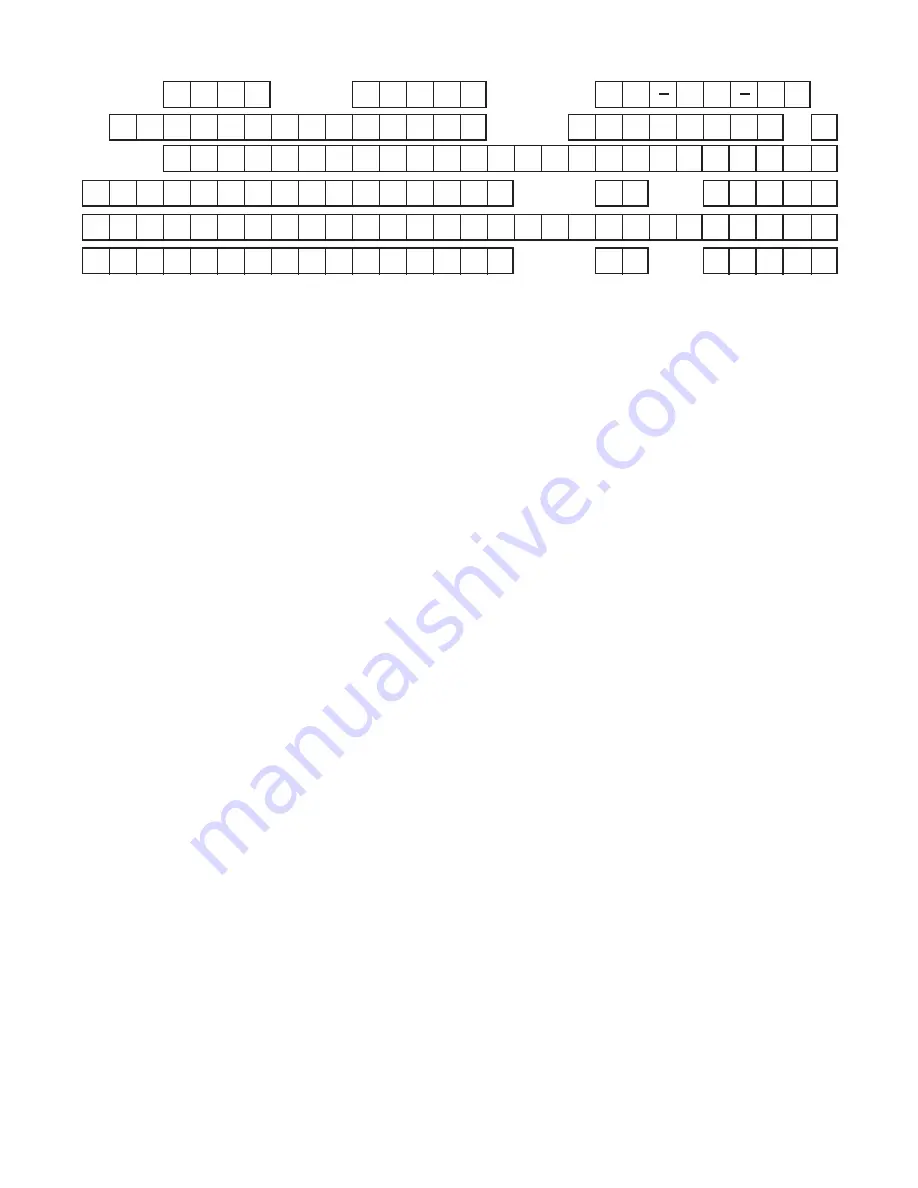
•
I have informed the Purchaser of this product of Warranty terms, provisions, and procedures that are applicable, reviewed the contents of the Operator’s Manual
including safety equipment, safe operation, and maintenance, reviewed the Safety Signs on implement (and tractor if possible), shown the AEM Mower Safety
Practices Video, and reviewed Purchaser’s responsibility to train his operators in safe operation.
•
IMPLEMENTS: I have explained that Deflectors, Chain Guards, or Solid Skirts must be maintained in good repair and installed except in areas where persons,
vehicles, livestock, or other property will not be endangered by thrown objects and where such safety equipment would prevent the mower’s reasonable performance
of its assigned task.
•
DRIVELINES: I have made certain that all driveline, gearbox, and other shields are in good repair and fastened securely in place to prevent injuries from
entanglement or thrown objects.
•
HYDRAULIC MACHINES: I have explained the necessity of using clean hydraulic oil, changing filters as instructed, stopping leaks, damage caused by
operating with over-heated oil, caring for hoses, using hoses of proper rating, the necessity of maintaining the specified operating pressure, and the potential hazard
of oil's penetrating the skin.
•
BOOM-TYPE or FOLDING-TYPE IMPLEMENTS: I have explained that it is not possible to guard against thrown objects when the head is lifted off ground
and that operator is responsible to watch out for persons in the area. I have explained that the lifted mower head or boom can contact overhead obstructions with
damage to cables and telephone lines and possible injury. I have explained that the extended head or boom or retracted boom can contact power lines with resulting
electrocution injury or death and that operator is responsible for keeping clear of such hazards.
Dealer’s Signature ___________________________________ Date ______________
I have been instructed on the paragraphs above, received and have been shown the AEM Mower Safety Practices Video and have been instructed in the contents
of the Operator’s Manual including safety signs, safety equipment, safe operation, maintenance, and the potential hazards of unauthorized alteration or modification
of the product. I have been informed of the warranty provisions and know that the warranty is not in effect until this form is received by Alamo Group.
I understand the Implement Guarding statements above and the potential hazards of operating without such guards. I understand that the operator is responsible for
the safety of others in the area. I have examined the product and accept it as being complete and in satisfactory condition with all required guards.
Purchaser’s Signature ___________________________________ Date ______________
Servis-Rhino Model
Serial No.
Purchase Date
M.I.
First Name
Purchaser
Last Name
Street & No., RFD,
Box, &/or Apt. No.
State or
Province
State or
Province
ZIP
ZIP
City
City
Dealer
MONTH
DAY
YEAR
SERVIS-RHINO
®
WARRANTY REGISTRATION INFORMATION
TEAR •
TEAR •
TEAR •
TEAR •
TEAR •
TEAR •
TEAR •
TEAR •
TEAR •
TEAR •
TEAR •
TEAR •
TEAR •
TEAR •
TEAR •
TEAR •
TEAR •
TEAR •
TEAR •
TEAR •
TEAR •
TEAR •
TEAR •
TEAR •
TEAR
Purchaser's Signature _________________________ Date __________ Dealer's Signature ________________________ Date __________
PRE-DELIVERY SERVICE
CHECK AND ADJUST OR LUBRICATE AS REQUIRED
See Operator’s Manual for Details
Inspection Performed - Warranty and Safety Procedures Explained - Installation Complete
LUBRICATION & HYDRAULICS
Gearboxes & Speed Increaser (Oil Levels)
Hydraulic Oil Level (External. Tank)
Tractor Hydraulic Oil Level
Hydraulic Hoses (No Kinks, Binds, or Leaks)
Hydraulic Hose Connections are Tight (No Leaks)
MOWER
Spindle And Motor Bolts Properly Torqued
Spindle Housing Bearings are lubricated
Blade Carrier Bolts Properly Torqued / Retaining Pin In Place
Mower Cutting Height And Level Adjusted
Belt Alignment And Tension Adjusted
Driveline Clutch (Torque Limiter) (Adjust And Run In)
All Hardware Properly Torqued
Tire Air Pressure / Lug Nuts (Correct Torque)
Wheel Bearings (Check, Grease, And Preload)
ATTACHMENTS & INSTALLATION
Thrown Object Deflectors Front And Rear
Correct Blade Rotation Direction
Wing transport locks and latches
Mower head transport support bracket
All Bolts - Pins And Nuts (Proper Torque)
MOWER TO TRACTOR CONNECTION
Draw Bar Length (Check And Set)
Axle Height (Adjusted)
Cutting Height (Adjust)
Mount Kit Pre-Operation Check Complete
Mower Wing (Adjust Level With The Center)
Mower Wing (Check For Proper Raising Operation)
Pull Type Hitch (Height Adjustment)
Mounting Hardware Properly Torqued
SAFETY ITEMS
Protective Shields (Operation And Installation)
S.M.V. Emblem (Installed)
Neutral Safety & Cut - Off Switches work properly
Safety Decals (Installed in good condition)
Operator’s Manual (Supplied in Canister)
AEM Mower Safety Manual (Supplied in Canister)
AEM Mower Safety Video has been shown to Purchaser _________
Pur. Intitials
AEM Mower Safety Video has been presented to Purchaser ________
Pur. Intitials
1. PRINT FIRMLY. 2. REMOVE WHITE COPY FOR CUSTOMER RECORDS. 3. REMOVE YELLOW COPY FOR DEALERS RECORDS. 4. MAIL LAST CARD POSTAGE FREE.
DEALER COPY
Summary of Contents for DM112
Page 7: ...SAFETY SECTION Safety Section 1 1...
Page 17: ...SAFETY Safety Section 1 11 DM 07 02 2004 Alamo Group Inc NOTES...
Page 23: ...SAFETY Safety Section 1 17 DM 07 02 2004 Alamo Group Inc 22 D103 26 2458315 27 00776481...
Page 25: ......
Page 26: ......
Page 27: ......
Page 28: ......
Page 29: ......
Page 30: ......
Page 31: ......
Page 32: ......
Page 33: ......
Page 34: ......
Page 35: ......
Page 36: ......
Page 37: ......
Page 38: ......
Page 39: ......
Page 40: ......
Page 41: ......
Page 42: ......
Page 43: ......
Page 44: ......
Page 45: ......
Page 46: ......
Page 47: ......
Page 48: ......
Page 49: ......
Page 50: ......
Page 51: ......
Page 52: ......
Page 53: ......
Page 54: ......
Page 55: ......
Page 56: ......
Page 57: ......
Page 58: ......
Page 59: ......
Page 60: ......
Page 61: ......
Page 62: ......
Page 63: ......
Page 64: ......
Page 65: ......
Page 66: ......
Page 67: ......
Page 68: ......
Page 69: ...Introduction Section 2 1 INTRODUCTION SECTION...
Page 71: ...ASSEMBLY SECTION Assembly Section 3 1...
Page 77: ...OPERATION SECTION Operation Section 4 1...
Page 88: ......
Page 89: ...MAINTENANCE SECTION Maintenance Section 5 1...
Page 97: ......
Page 100: ...DISC MOWER OM 07 02 Printed U S A 4909WC DM82 DM95 DM112 DM124 Disc Mower DISC MOWER...
Page 103: ......
Page 105: ......