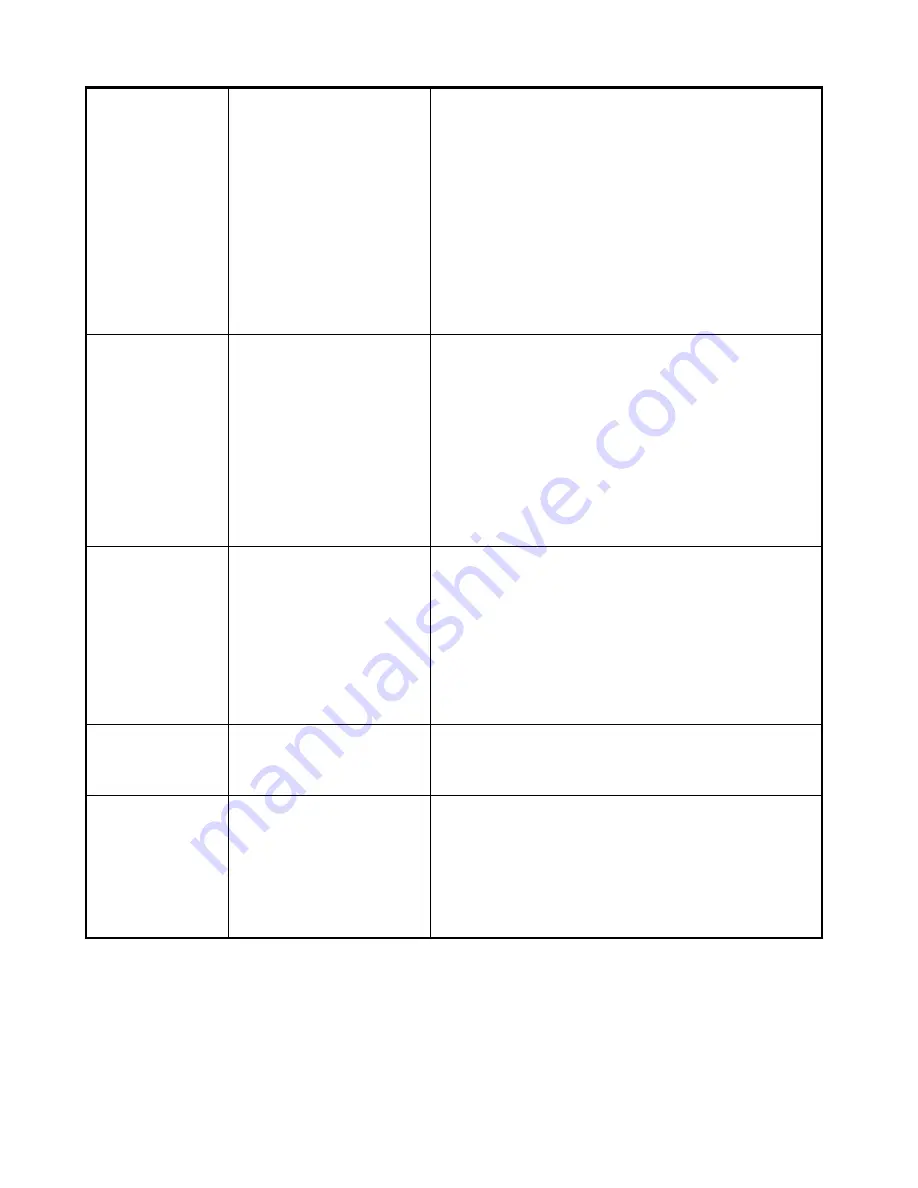
11
Saw operates
erratically
Leak in system.
Saw parts sticking or binding.
Dirt or contaminants in saw
parts.
Tighten fittings. Inspect all hoses for leaks as described in
Section 3.1.1. REPLACE A LEAKING HOSE
IMMEDIATELY. NEVER TRY TO REPAIR IT.
Check for dirt or gummy deposits. Clean parts.
Check for worn or damaged parts and replace as required.
Be sure flanges are clean and straight so blade will run true on
sides. See Chapter 4 for proper blade mounting procedure.
Disassemble saw and clean parts.
Saw operates slowly.
Insufficient flow.
Hydraulic fluid level low.
Hydraulic fluid viscosity too
heavy.
Saw parts loose.
Saw parts worn or damaged.
Refer to power source operator’s manual for proper
adjustment of flow.
Check fluid level. Fill to full mark. Check system for leaks.
Use fluid viscosity recommended. See Section 2.5.
Tighten component hardware.
Disassemble saw and replace worn or damaged parts.
Saw feels hot.
Power source heat exchanger
malfunctioning
Hydraulic fluid level low.
Hydraulic fluid dirty.
Excessive flow
Refer to power source operator’s manual.
Check fluid level. Fill to full mark. Check system for leaks.
Drain reservoir, flush and fill with clean fluid. Change filter.
Refer to power source operator’s manual for proper
adjustment of flow
Saw leaks hydraulic
fluid.
Saw parts loose.
Saw parts worn or damaged.
Tighten component hardware.
Disassemble saw and replace worn or damaged parts.
Saw control valve
sticks or works hard.
Check for dirt or gummy
deposits.
Misalignment or binding of
control linkage.
Valve parts damaged.
Clean parts.
Correct alignment, lubricate linkage joints, and replace
damaged parts.
Disassemble valve and replace damaged parts.