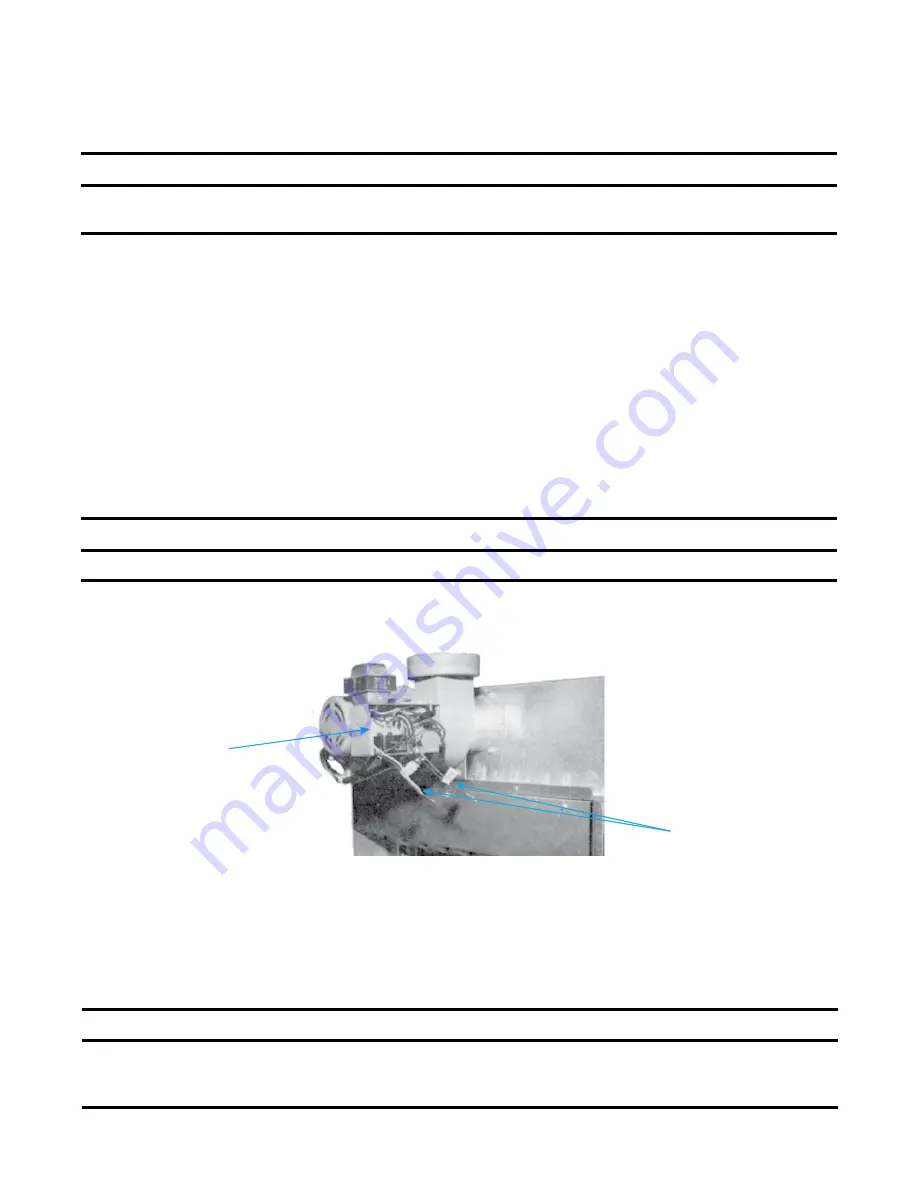
36
I-EEDU (02-21) 150492-A
FIELD-INSTALLED OPTIONS—CONTINUED
Thermostat Installation
⚠ CAUTION ⚠
If applicable, ensure that the thermostat has an adequate VA rating for the total requirements. Add
the coil ratings of all relays and match the thermostat rating.
•
A thermostat is not standard equipment but is an installation requirement . Use either an optional thermostat available
with the heater or a field-supplied thermostat . Install according to the thermostat manufacturer’s instructions .
•
A 24-volt thermostat must be used to actuate low voltage gas controls . If line voltage from the thermostat to the
unit is desired, consult the factory representative .
•
Labeled thermostat leads are provided in the heater junction box for connection of thermostat wiring .
•
Thermostats should be located 5 feet (1 .5 meters) above the floor on an inside wall—not in the path of warm or
cold air currents and not in corners where air may be pocketed .
•
Do NOT install thermostat on cold air walls . For specific connection details, refer to instructions with the thermostat .
•
If more than one unit is cycled from one thermostat, separately-activated relays must be substituted at unit
thermostat connections .
•
If using a low voltage thermostat with a heat anticipator, set the anticipator at full load control amps .
Electrical Connections for Field-Installed Options
⚠ WARNING ⚠
If you turn OFF the electrical power supply, turn OFF the gas.
For field-installed options that require electrical connections in the electrical box (see
), refer to the instruction
sheet and wiring diagram provided in the option package .
Figure 27. Wiring Field-Installed Options
CONTROLS
Unit controls are described in the following paragraphs .
Combustion Air Proving Switch
⚠ DANGER ⚠
Safe operation of this unit requires proper venting flow. NEVER bypass combustion air proving
switch or attempt to operate the unit without the venter running and the proper flow in the vent
system. Hazardous conditions could result.
LINE VOLTAGE
CONNECTION TABS
ELECTRICAL BOX