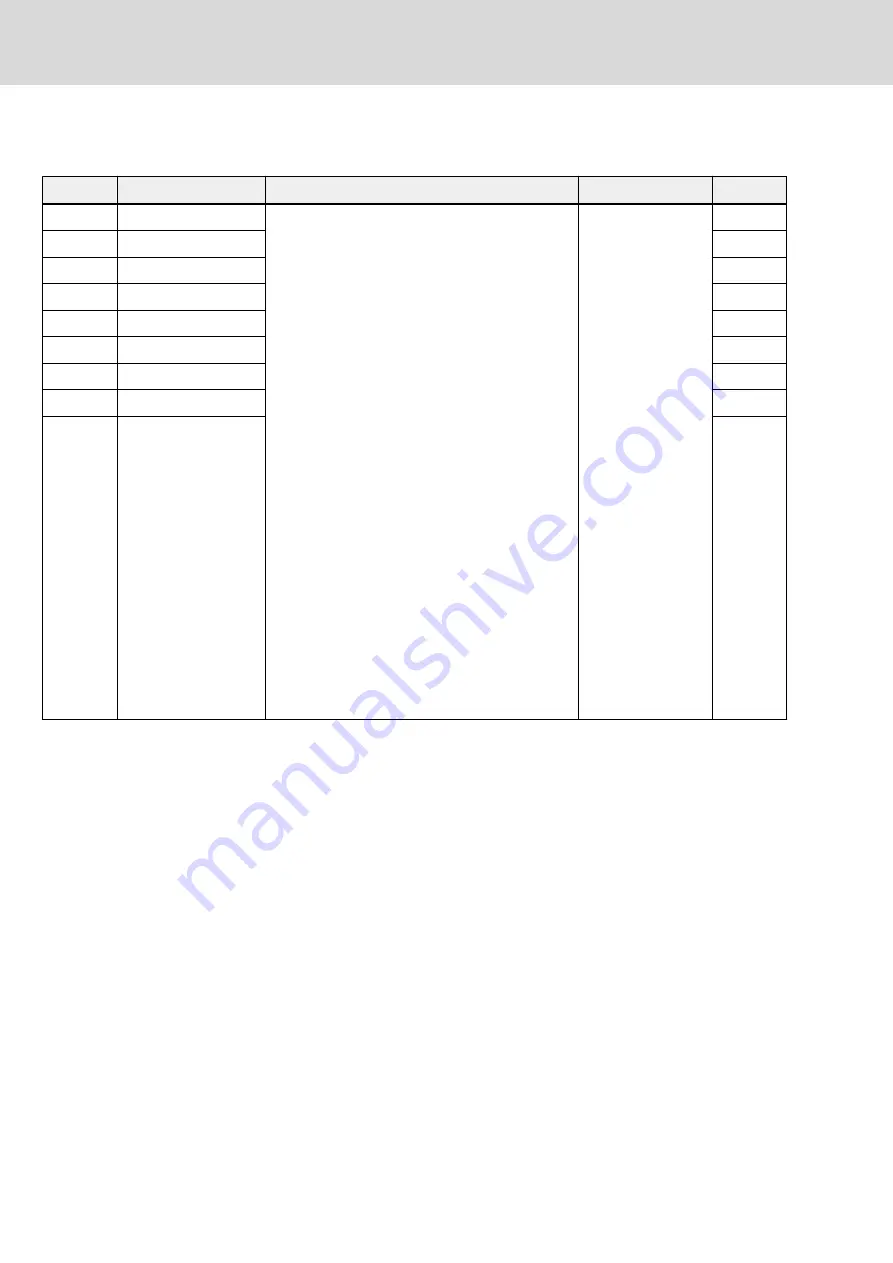
7.5.8
Sensor Monitoring
Code
Name
Setting range
Default
Attri.
F2.16
X1 input
0: No function assigned from ASF
1: Pressure command selection bit0
2: Pressure command selection bit1
3: p/Q parameter selection
4: Reserved
5: Master / slave mode switch
6: Oil filter warning
7: Oil level warning
8: Oil temperature warning
9: Oil filter error
10: Oil level error
11: Oil temperature error
12: Oil level / temperature error
13: Oil filter warning inverse
14: Oil level warning inverse
15: Oil filter error inverse
16: Oil level / temperature error inverse
17: Reserved
18: Reserved
19: Reserved
20: Pressure drop compensation trigger
21: Pressure overshoot compensation trigger
Stop
F2.17
X2 input
Stop
F2.18
X3 input
Stop
F2.19
X4 input
Stop
F2.20
X5 input
Stop
F2.21
EX1 input
Stop
F2.22
EX2 input
Stop
F2.23
EX3 input
Stop
F2.24
EX4 input
Stop
Tab. 7-29:
Parameter list of sensor monitoring
There are different sensors used for monitoring the hydraulic system, and
there are also corresponding options for digital input to be selected, see op‐
tion 6...16 in the table above. Most of these options can be clarified by name,
the others are described below:
''6: Oil filter warning'' and ''9: Oil filter error'' for oil filter warning and error sen‐
sor. These signals will be automatically delayed by F4.50, that means a true
signal lasted longer than [F4.50] seconds will be acknowledged.
''12: Oil level / temperature error'', for oil level and temperature error sensor.
Both oil level and temperature can be connected parallel to one digital input,
since oil warning comes earlier than error, the warning information will help
controller to determine if it is an ''oil level error'', ''oil temperature error'' or
even ''oil level or temperature error'' if both or no warning is available.
''13: Oil level warning inverse'' and ''14: Oil level / temperature error inverse''
are inversed evaluation from ''7: Oil level warning'' and ''12: Oil level / temper‐
ature error'', i.e. true signal for no warning, and false signal for warning. Sig‐
nal has been inversed for wire broken monitoring.
All warning and error information are presented by d0.88 and d0.89, see
chapter 7.10.8 "Monitoring Parameter" on page 143
Bosch Rexroth AG
DOK-SYTROX-FCP5020****-IT01-EN-P
116/201
Frequency-controlled pump drive system Sytronix FcP 5020
Commissioning of Sytronix FcP 5020 System