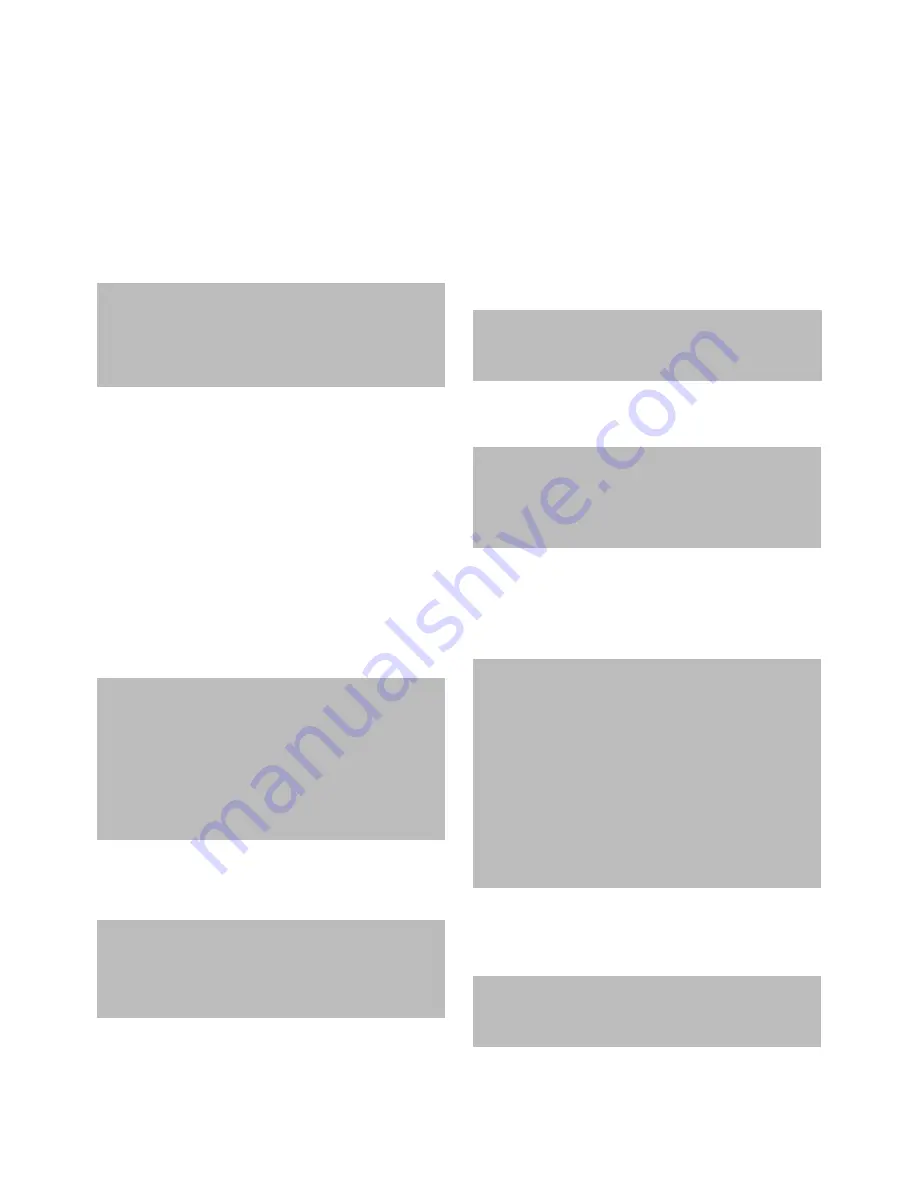
10
TILTING THE TABLE (FIG. 27)
NOTE:
The table arm and support (1)
has a threaded hole with a locking set
screw inserted for locking the table into a
predetermined 0o horizontal position.
1. TIGHTEN the nut (2) on the locking pin
in the clockwise direction to RELEASE
the pin from the table support.
2. LOOSEN the large hex head bevel
locking bolt (3) and move table to
desired position then retighten.
Maintenance
GENERAL MAINTENANCE
Frequently blow out dust and grit that
accumulates in the motor housing using
compressed air.
A coat of automotive paste wax applied to
the table and column will help to keep the
surface clean.
WARNING!
To prevent injury, be sure to
hold the table & table arm assembly, so it
will not swivel or tilt.
WARNING!
For your own safety, turn the
switch off and remove the plug from the
power source outlet before maintaining or
lubricating your drill press.
4. Tap the key wedge (4) lightly with a
plastic tipped hammer, until the chuck
and arbor fall out of the spindle.
NOTE:
Place one hand below the chuck to
catch it when it falls out.
BASIC OPERATION INSTRUCTIONS
To get the best results and minimize the
likelihood of personal injury, follow these
instructions for operating your drill press.
POSITIONING THE TABLE AND
WORKPIECE (FIG. 25, 26 )
1. Lock the table (1) to the column (2) at
a position so the tip of the drill bit (3) is
just above the top of the workpiece (4).
2. ALWAYS place BACK-UP MATERIAL
(scrap wood) on the table beneath the
workpiece. This will prevent splintering
or heavy burring on the underside of the
workpiece. To keep the back-up material
from spinning out of control, it MUST
contact the LEFT side of the column.
3. For small pieces that cannot be
clamped to the table, use a drill press
vise (optional accessory).
WARNING!
For your own safety, always
observe the SAFETY INSTRUCTIONS
listed on pages 4, 5 and 6 of this instruction
manual when operating the drill press.
WARNING!
To prevent the workpiece or
backup material from being torn from your
hands while drilling, you MUST position it
against the LEFT side of the column. If the
workpiece or the backup material is not
long enough to reach the column. Failure to
do this could result in personal injury.
WARNING!
When using a drill press vise, it
MUST be clamped or bolted to the table to
avoid injury from a spinning workpiece, or
damaged vise or bit parts.
WARNING!
ALWAYS use safety glasses.
Everyday eyeglasses are NOT safety
glasses. Also use face or dust mask if
cutting operation is dusty. ALWAYS WEAR
CERTIFIED SAFETY EQUIPMENT:
• ANSI Z87.1 eye protection (CAN/CSA
Z94.3),
• ANSI S12.6 (S3.19) hearing protection,
• NIOSH/OSHA/MSHA respiratory
protection.
WARNING!
To avoid shock or fire hazard,
if the power lead is worn or cut in any way,
replace it immediately.
Summary of Contents for DP3800RF
Page 1: ...1 GB 15 IN 381 MM DRILL PRESS DP3800RF INSTRUCTION MANUAL...
Page 2: ...2 CONTENTS GB P 1 11 The original instruction manual is in English...
Page 16: ...13 1 2 3 2 3 2 5 1 Fig 6 Fig 7 Fig 8 1 2 Fig 9 Fig 10 Fig 11 1 ON OFF SWITCH 3 1 2 5 7 6 4...
Page 18: ...15 Fig 18 Fig 19 Fig 21 Fig 22 Fig 23 Fig 20 2 1 3 3 2 1 5 4 6 3 2 1 1 3 2 12 13...
Page 19: ...16 Fig 24 Fig 25 Fig 26 Fig 27 1 4 2 3 3 4 1 2 3 2 1...
Page 21: ...18 Schematic MODEL DP3800RF MANUAL INSTRUCTION 36JG 2JPC 36JH...
Page 22: ...19 NOTES...
Page 23: ...20...
Page 24: ...21...