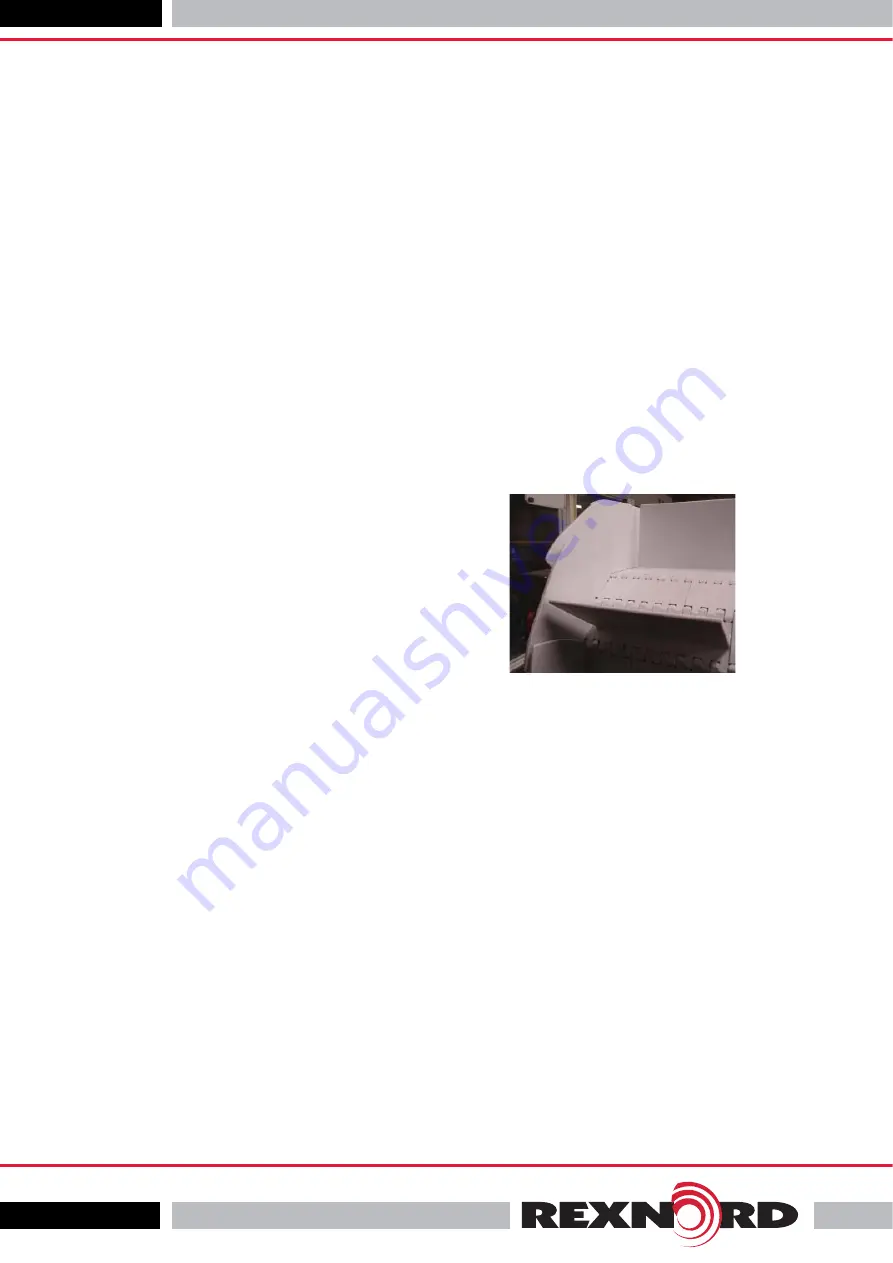
7
CURRENT SYSTEMS
•
Cleaning of the inclined conveyor is often not easy because of their
height. The chain rotates and passes the lowest point in the conveyor
and therefore can be cleaned. However, the static guides at the top of
the conveyor cannot be reached easily. This is an issue as there are
parts of the conveyor that actively touch the product. If the guides can
be opened up or removed for enhanced cleaning, they have to be ac
curately re-positioned prior to start-up, which again is time consuming
and needs to be done accurately.
The advantage of static guards is that they can be custom made to a desired height
to create the required capacity of the conveyor. In practice this means they can be
used to accompany up to a 6-inch high pusher attachment that are typically used on
plastic modular belt/chain, optimizing conveyor capacities.
Conventional two piece side guards
Two piece side guards are the conventional
system; they exist as loose parts that are con-
nected with the chain using the chain connec-
tion pin. Although this system eliminates the
installation and cost issues of static guides
there are still some disadvantages:
•
Due to their connection with the chain, a pin-hinge construction, sideguards
are not very stable and the top of the sideguards can move to the left and the
right rather easily. This makes the conveyor design for chains with convention
al side guards more complicated. Every construction element that could
cause the side guards to jam during operation should be addressed thus re
quiring more chain clearance through out the system.
•
As a standard the conventional side guards often are not positioned directly
against the pusher. This is done to avoid jamming between the sideguards
and the pusher when for-fl exing around a sprocket and fl exing back when
entering the conveyor return. If an opening between the pusher and side
guard is allowed, product is not properly retained.
•
Conventional side guards have a clear orientation in relation to the direction
of chain travel. This is because they are located in an angled overlapped posi
tion. If they are set to retain the product in an optimum way, they are more
sensitive to jamming in the conveyor frame. If they are set not to jam (oppo
site overlap), product can get caught in between them.
Summary of Contents for MatTop
Page 13: ...13 NOTES ...