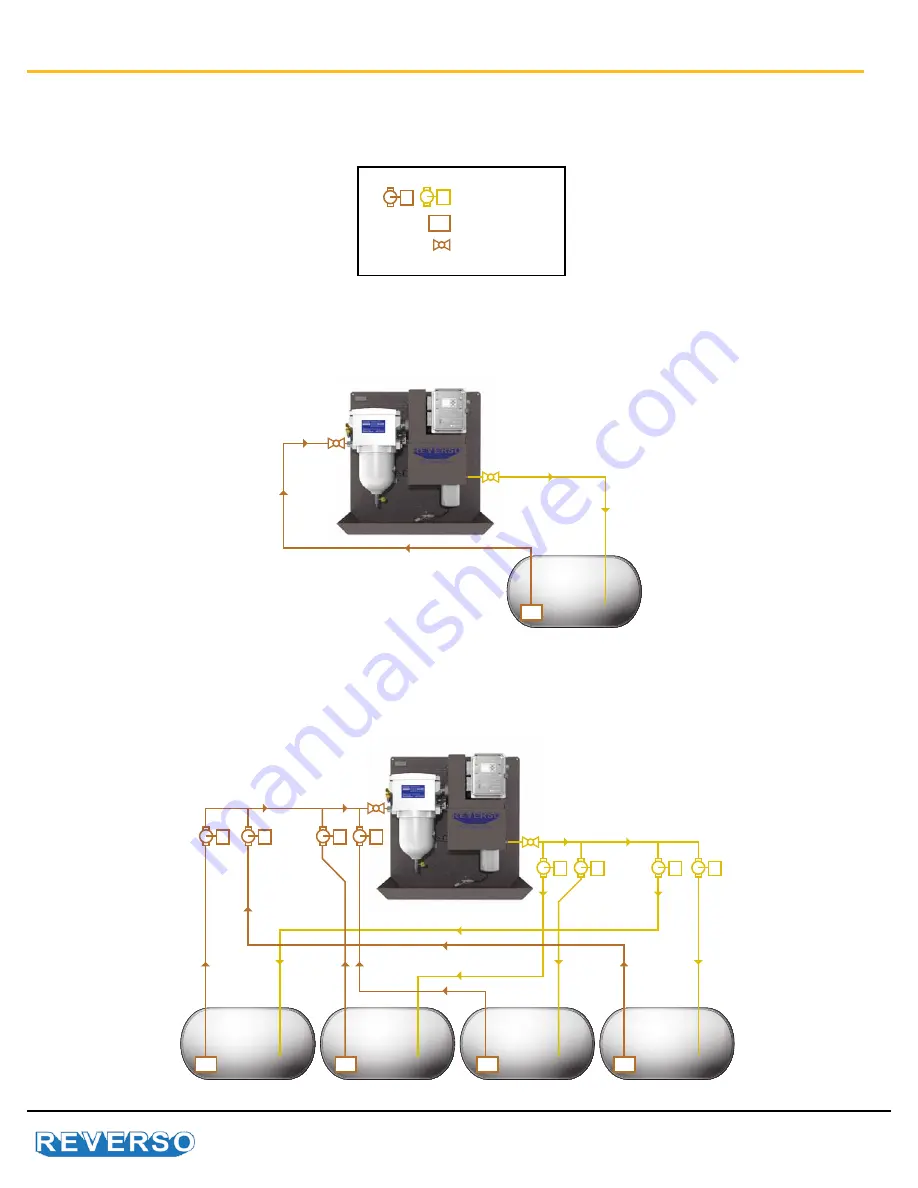
10
Reverso Pumps, Inc. www.reversopumps.com | [email protected] | Ph: (954) 522-0882
Tank Diagrams
Diag. 2
Hoses, piping, solenoid valves and foot valves shown in the diagrams below are not provided with the system and
must be provided by the user/contractor, unless agreed upon otherwise.
Single Tank Diagram
Fuel
Tank
FV
Fuel
Tank
#
1
Fuel
Tank
#
2
Fuel
Tank
#
3
Fuel
Tank
#
4
S
S
S
S
S
S
S
S
FV
FV
FV
FV
S
S
FV
Solenoid valve
Foot valve
Ball valve
Fuel
Tank
#
1
Fuel
Tank
#
2
Fuel
Tank
#
3
Fuel
Tank
#
4
S
S
S
S
S
S
S
S
FV
FV
FV
FV
S
S
FV
Solenoid valve
Foot valve
Ball valve
Requires Advanced Control (Touchscreen)
Diag. 3
Multiple Tank Diagram