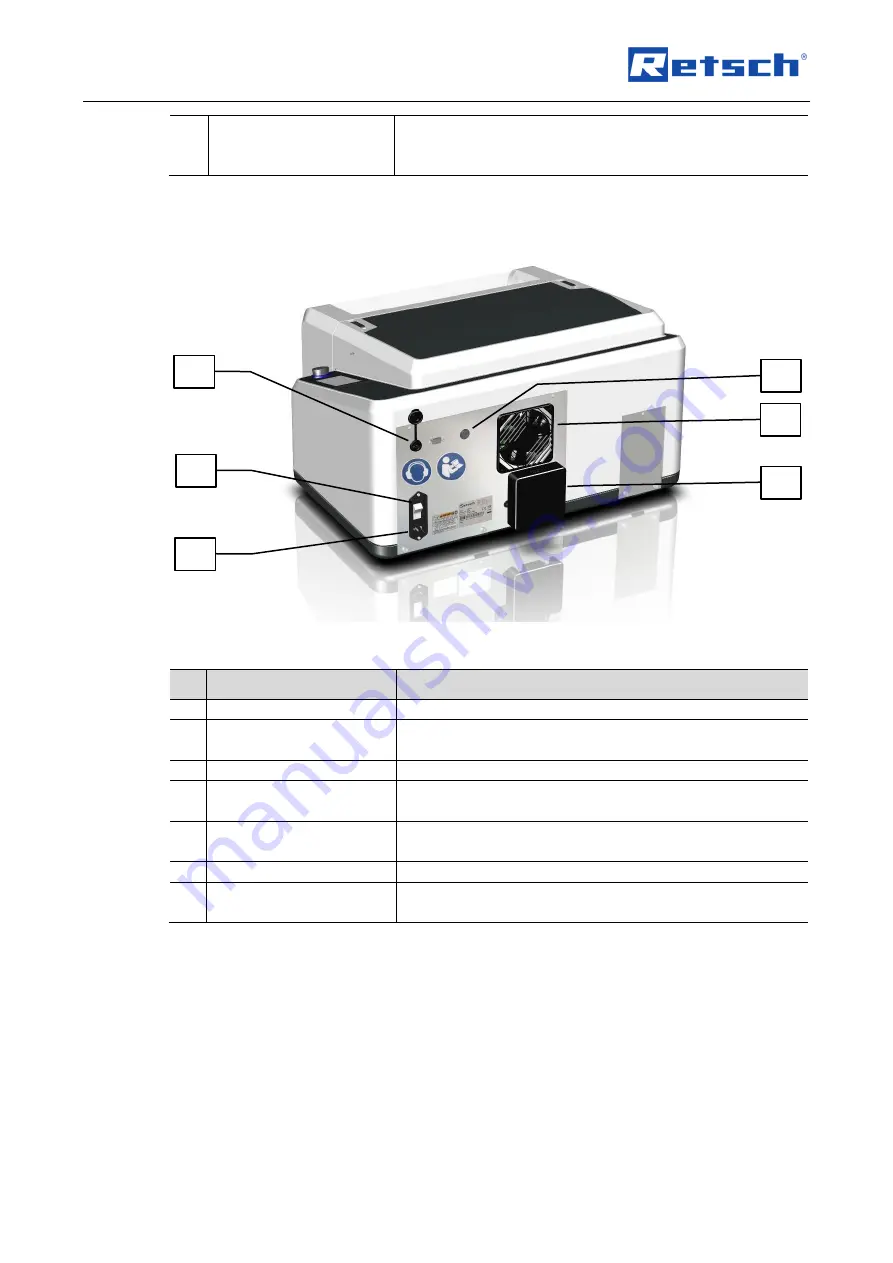
The Mixer Mill MM 500 nano
19
KO Direction of rotation of
the locking wheel:
open the clamps
Opens the clamps, thereby enabling the grinding jar to be
removed.
3.3.3 Back
Fig. 6:
Back of the device
Component
Function
K
USB interface
To update the operating software.
I
Main switch
To switch the device on or off using the motor protection
circuit breaker.
M
Appliance socket
Connection for the mains lead.
U
RS232 interface
To connect the GrindControl (optional
temperature/pressure measurement system).
J
Interface for Retschbox
To connect the Retschbox (optional
Wi-Fi module).
GL Housing fan
To conduct waste heat.
RB Retschbox
Optional equipment. Among other things permits remote
control of the device.
K
I
M
J
GL
RB
Summary of Contents for Mixer Mill MM 500 nano
Page 2: ...2 Copyright Copyright by Retsch GmbH Retsch Allee 1 5 42781 Haan Germany...
Page 5: ...5 10 1 Returning for repair and maintenance 85 11 Accessories 87 12 Disposal 88 13 Index 90...
Page 6: ...Notes on the manual 6...
Page 76: ...Device control 76 Image 53 MyRetsch QR code to access the web portal Image 54 QR code...
Page 89: ...Disposal 89...
Page 94: ......
Page 95: ...Copyright Copyright by Retsch GmbH Retsch Allee 1 5 42781 Haan Germany...