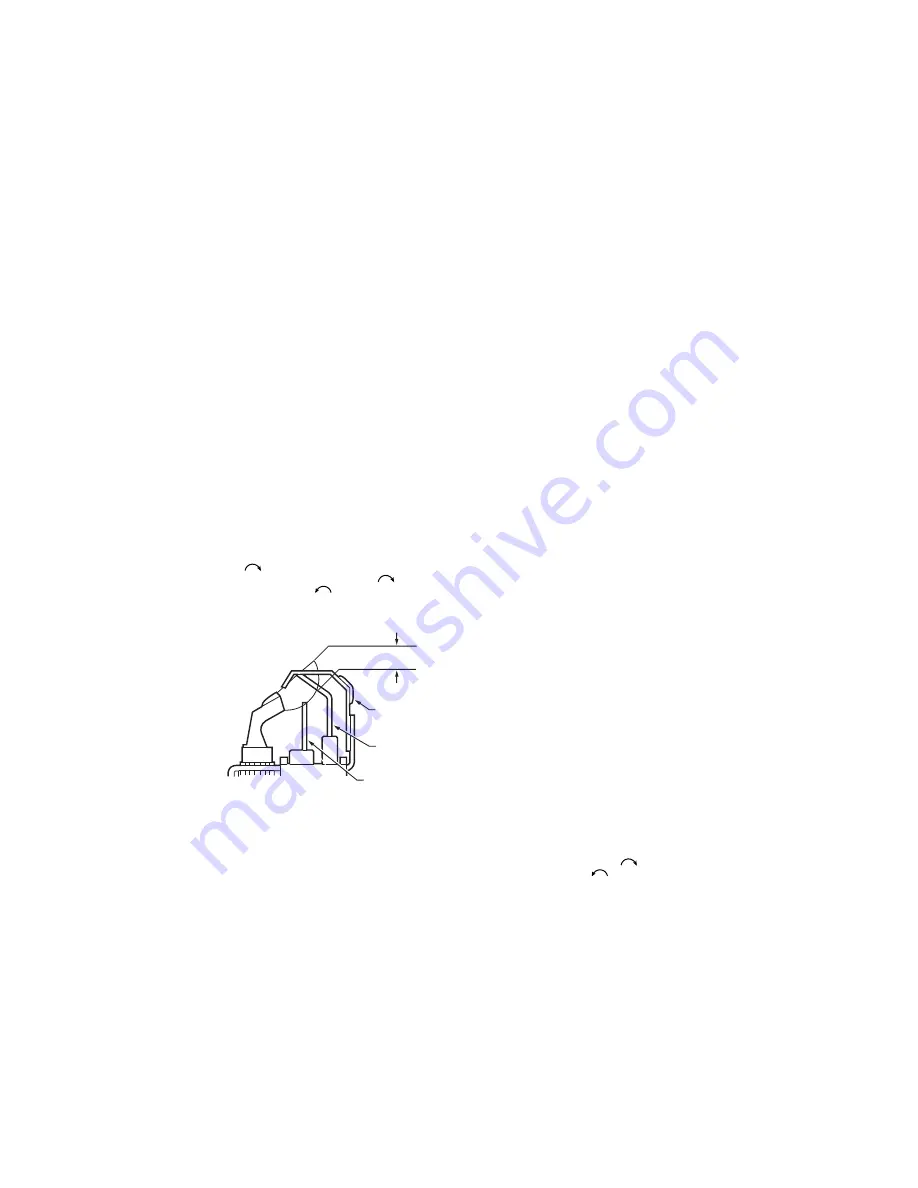
SV9440, SV9540, AND SV9640 SMARTVALVE™ SYSTEM CONTROLS
11
69-1227—02
Gas Leak Test
1.
Paint pipe connections upstream of the ignition
system control with rich soap and water solution.
Bubbles indicate a gas leak.
2.
If a leak is detected, tighten the pipe connections.
3.
Light the main burner. Stand clear of the main
burner while lighting to prevent injury caused from
hidden leaks that could cause flashback in the
appliance vestibule.
4.
With the main burner in operation, paint the pipe
joints (including adapters) and the control inlet and
outlet with rich soap and water solution.
5.
If another leak is detected, tighten the adapter
screws, joints, and pipe connections.
6.
Replace the part if a leak cannot be stopped.
Check and Adjust Pilot Flame
The pilot flame should envelop 3/8 to 1/2 in. (10 to
13 mm) of the tip of the flame rod. It should also be in
continual contact with the ground electrode. See Fig. 13.
If the pilot flame is small or lazy, or does not touch the
ground electrode, the inlet gas pressure may be too low,
or the pilot orifice may be partially clogged. Check and
repair as necessary. If the pilot flame is hard and noisy,
the inlet gas pressure may be too high. The ignition
system control has a pilot adjustment mechanism to
reduce the pilot flow if necessary. If pilot adjustment is
necessary, proceed as follows:
1.
Remove pilot adjustment cover screw. See Fig. 6.
2.
The pilot adjustment is shipped at the full pilot gas
flow rate. Turn the inner adjustment screw clock-
wise
if the inlet pressure is too high. Turn the
inner adjustment screw clockwise
to decrease
or counterclockwise
to increase pilot flame.
3.
Replace the cover screw after the adjustment to
prevent gas leakage.
Fig. 13. Proper flame adjustment.
CHECK AND ADJUST GAS INPUT
AND BURNER IGNITION
IMPORTANT
1. Do not exceed input rating stamped on appli-
ance nameplate, or manufacturer’s recom-
mended burner orifice pressure for size
orifice(s) used. Be sure primary air supply to
main burner is properly adjusted for complete
combustion. Follow appliance manufacturer
instructions.
2. IF CHECKING GAS INPUT BY CLOCKING GAS
METER: Make certain there is no gas flow
through the meter other than to the appliance
being checked. Other appliances must remain
off with the pilots extinguished (or deduct their
consumption from the meter reading). Convert
flow rate to Btuh as described in form 70-2602,
Gas Controls Handbook, and compare to Btuh
input rating on appliance nameplate.
3. IF CHECKING GAS INPUT WITH MANOMETER:
Make sure the ignition system control is in the
OFF position before removing outlet pressure
tap plug to connect manometer (pressure
gauge). Also move the ignition system control
switch to the OFF position when removing the
gauge and replacing the plug. Before removing
inlet pressure tap plug, shut off gas supply at
the manual valve in the gas piping to the appli-
ance or, for LP, at the tank. Also shut off gas
supply before disconnecting manometer and
replacing plug. Repeat Gas Leak Test at plug
with main burner operating.
NOTE:
Check the inlet pressure before adjusting the
pressure regulator.
Standard and Slow-Opening (H, K
and M) Models
1.
Carefully check the main burner lightoff. Make sure
that the main burner lights smoothly and that all
ports remain lit.
2.
Check the full rate manifold pressure listed on the
appliance nameplate. Ignition system control full
rate outlet pressure should match this rating.
3.
With main burner operating, check the ignition sys-
tem control flow rate using the meter clocking
method or check pressure using a manometer con-
nected to the outlet pressure tap on the ignition
system control. See Fig. 6.
4.
If necessary, adjust the pressure regulator to
match the appliance rating. See Table 7 and
Table 8 for factory-set nominal outlet pressure and
adjustment range.
a. Remove the pressure regulator adjustment cap
screw.
b. Using a screwdriver, turn the inner adjustment
screw (Fig. 6) clockwise
to increase or
counterclockwise
to decrease the gas
pressure to the burner.
c. Always replace the cap screw and tighten
firmly to prevent gas leakage.
5.
If the desired outlet pressure or flow rate cannot be
achieved by adjusting the ignition system control,
check the ignition system control inlet pressure
using a manometer at the inlet pressure tap of the
ignition system control. If the inlet pressure is in
the nominal range (see Table 7 and Table 8),
replace the ignition system control. Otherwise, take
the necessary steps to provide proper gas pressure
to the control.
PROPER FLAME
ADJUSTMENT
HOT SURFACE
IGNITER
FLAME ROD
M3350C
GROUND
ELECTRODE
3/8 TO 1/2 IN.
(10 TO 13 MM)
NOTE: GROUND ELECTRODE MUST NOT TOUCH FLAME
ROD (.050 IN. MINIMUM CLEARANCE). BEND GROUND
ELECTRODE IF NECESSARY. DO NOT BEND FLAME ROD.