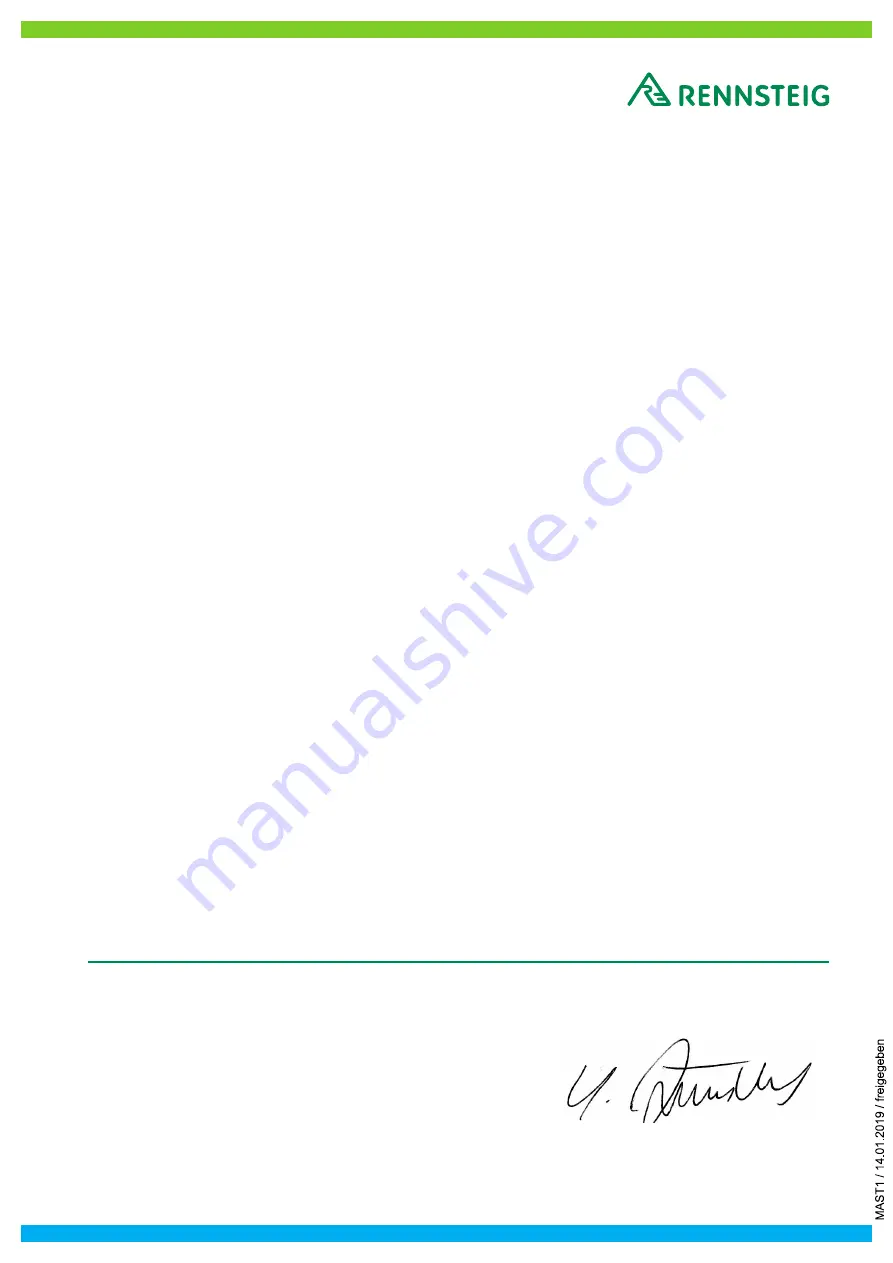
Owner‘s Manual Crimping Machine CM 25-1.3
Rev.: 2016-05-31
15 / 15
10. EU-Declaration of Conformity according to EU Guidelines for Machines
2006/42/EG, Appendix II
The construction of the Crimping Machine
Type:
CM
25-1.3
No.:
Year of Construction:
Was developed, constructed and manufactured in compliance with the EU- Guidelines for Machines
2006/42/EG with sole responsibility:
Company:
Rennsteig Werkzeuge GmbH
An der Koppel 1
98547
Viernau
Responsible person in charge of documentation: Klaus Bamberger
The following EU-guidelines and harmonized standards were applied:
•
Machine Guideline 2006/42/EG
•
RoHS-Guideline 2011/65/EU
•
DIN EN 12100:2010 Safety of Machines – General Principles of Design– Risk Assessment
and Risk Reduction
•
DIN EN ISO 13857:2008 Safety of Machines – Safety distances to prevent upper and lower
extremities from entering hazardous zones
•
EN ISO 13849-1:2008/AC:2009 Safety of Machines – Safety-related Parts of the Control
System- Part 1: General Principles of Design
•
EN ISO 13849-2:2012 Safety of Machines – Safety-related Parts of the Control System - Part
2: Validation
•
DIN EN ISO 4414:2011-04 Fluid Technology - General Rules and Safety-related Regulations
concerning Pneumatic Systems and Parts thereof (ISO 4414:2010); German Version EN ISO
4414:2010
Hereby we declare that this delivery includes the entire above described machine.
Viernau, the
________________________________
CEO Herr Sascha Zmiskol