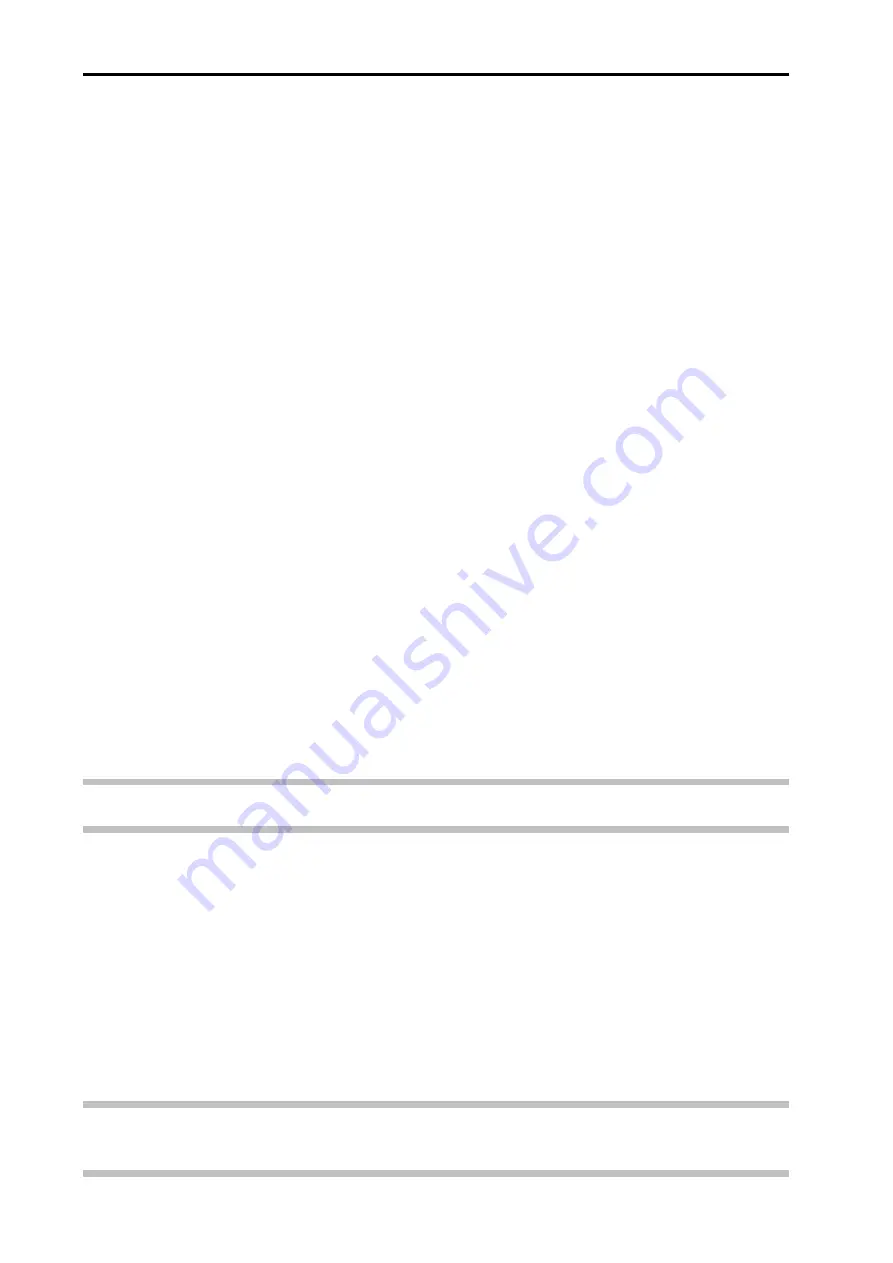
28
Definitions
4.5 I
2
t Time
The amount of time for which peak motor current is allowed to flow. If this is exceeded a fault is software
generated to protect against motor over heating. Continuous current, or anything less, will be allowed to
flow for unlimited time without fault.
4.6
IET Time
This is the
current error time limit and will occur if there is a break in the loop after the DSP (e.g. no motor
power or motor not connected) or if the current servo is badly tuned. This is a software generated fault that
protects against excessive servo error in the current loop.
4.7
Overshoot (per axis)
The overshoot will be computed in absolute terms i.e.
Overshoot = max value of read position – Steady State Position.
4.8
Following error (per axis, already existing)
Following Error (t) = Read position (t) – Demand position (t)
Typical Following Error = Following Error (mid_time) averaged over 10 readings.
4.9
Steady state error (per axis)
Steady State Error = absolute value (mean(last 10 points of read position) – Target position).
NOTE:
This includes the RMS noise.
4.10 Settling time (per axis)
The settling time is the time difference between the theoretical time to get to HOLD and the time measured
to get to HOLD.
4.11 Tunnelling error (for the 3D move)
The tunnelling error is the maximum distance between the two curves (real and demand) and is the
distance between the point read (measured) and its projection on the demand vector.
NOTE:
The distance between two points in space is the modulus of the vector formed by these two points
(direction is not relevant here).