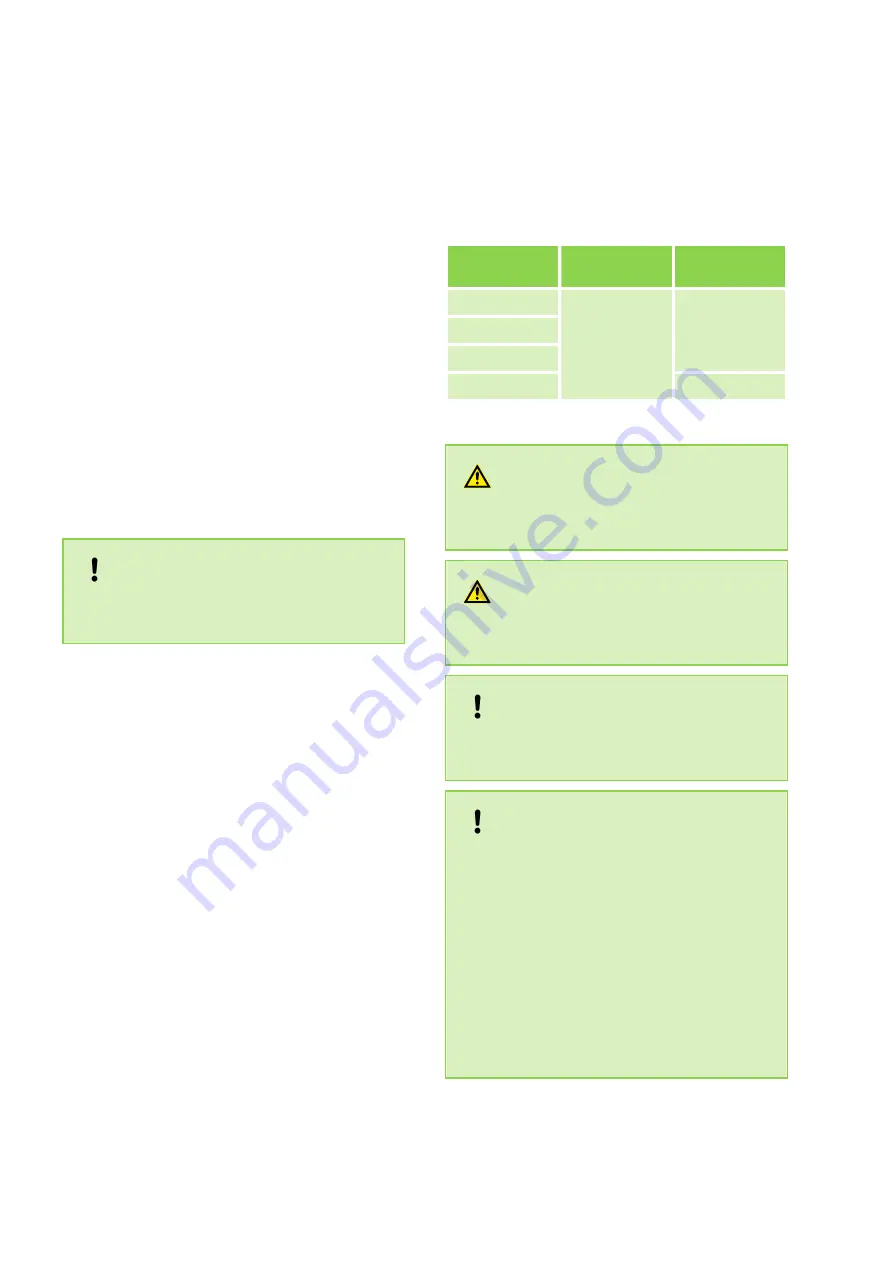
6.4
Leak testing
Once all the connections have been made, the
pressure gauge station is attached to the Schrader
valve as follows (if fitted):
red = small valve = high pressure
blue = large valve = suction pressure
Once the connection has been made successfully,
the leak test is carried out with dry nitrogen.
Leak testing involves spraying a leak detection
spray onto the connections. If bubbles are visible,
the connections have not been made properly. In
that case, tighten the connection or, if necessary,
create a new flange.
After completing a successful leak test, the excess
pressure in the refrigerant piping is removed and a
vacuum pump with an absolute final partial pres-
sure of min. 10 mbar is used to remove all of the
air and empty the pipes. Any moisture present in
the pipes will also be removed.
NOTICE!
A vacuum of at least 20 mbar must be pro-
duced!
The time required to generate the vacuum is
dependent on the final pressure pipe volume of the
indoor units and the length of the refrigerant piping.
However, the process will take at least
60
minutes
. Once any foreign gases and humidity
have been completely extracted from the system,
the valves on the pressure gauge station are
closed and the valves on the outdoor unit are
opened as described in the "Commissioning" sec-
tion.
6.5
Adding refrigerant
The units contain a basic quantity of refrigerant. In
addition, an additional amount of refrigerant must
be added for refrigerant piping lengths exceeding 5
metres per circuit. Refer to the following chart:
Up to and
incl. 5m
From 5m to
max. length
RVT 262
0 g/m
20 g/m
RVT 352
RVT 522
RVT 682
40 g/m
CAUTION!
Wear protective clothing when handling refrig-
erant.
DANGER!
Only refrigerant in a liquid state may be used to
fill the cooling cycle!
NOTICE!
Check the overheating to determine the refrig-
erant fill quantity.
NOTICE!
The escape of refrigerant contributes to cli-
matic change. In the event of escape, refrig-
erant with a low greenhouse potential has a
lesser impact on global warming than those
with a high greenhouse potential. This device
contains refrigerant with a greenhouse poten-
tial of 1975. That means the escape of 1 kg of
this refrigerant has an effect on global warming
that is 1975 times greater than 1 kg CO
2
,
based on 100 years. Do not conduct any work
on the refrigerant circuit or dismantle the
device - always enlist the help of qualified
experts.
REMKO RVT-ARCTIC-WP
36
Summary of Contents for RVT 262
Page 66: ...REMKO RVT ARCTIC WP 66...
Page 67: ......