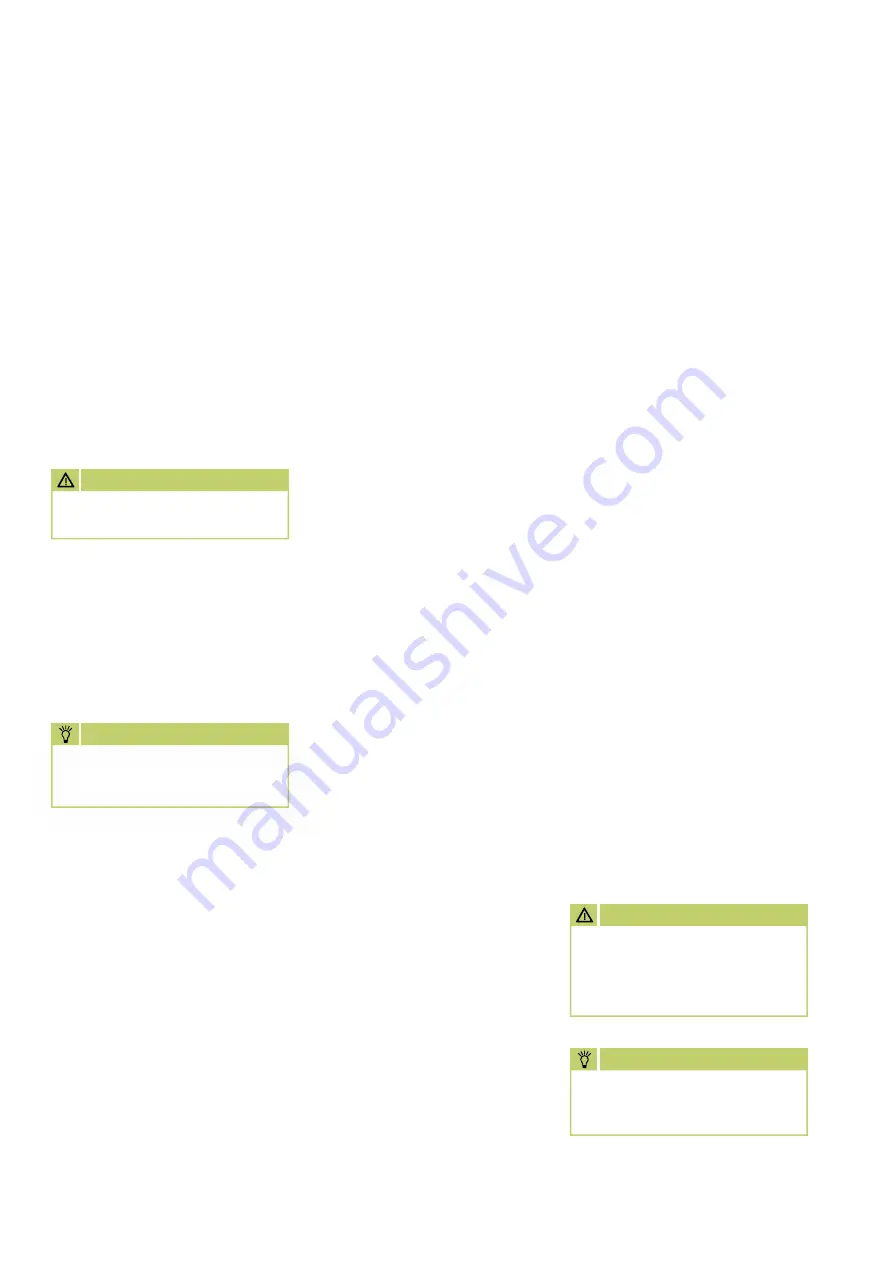
10
REMKO PWW
Care and maintenance
The units are virtually mainte-
nance-free in normal operation.
However, to ensure trouble-free
operation, they should be in-
spected regularly and cleaned if
necessary.
Important precautions to be
taken before carrying out any
maintenance:
■
The units must be disconnected
from the supply in all poles and
locked to prevent unauthorised
reconnection.
■
Wait for the fan to stop.
■
Shut-off the water circuit and
lock to prevent unauthorised
opening.
■
Allow the fin heat exchanger to
cool down.
Cleaning agents
■
The units must be cleaned only
dry or with a moist cloth and a
small amount of soap solution if
necessary.
■
Under no circumstances use
high-pressure cleaners or steam
jet equipment.
■
Do not use caustic or solvent-
containing cleaning agents.
■
Only suitable cleaning agents
must be used to remove heavy
fouling.
AttENtiON
It does not suffice to switch off
the unit only via the switch!
NOtE
The fan impeller and alumini-
um fins must not be damaged
or bent.
Cleaning the units
■
Clean all air inlets and air outlet
fins.
■
Clean the fan impeller. If ne-
cessary, remove the motor or
protection grille.
■
Clean the heat exchanger fins
either by blowing out, suction
or with a soft brush.
■
Remove heavy fouling on the
fan and aluminium fins with a
soap solution.
Repair
Fan replacement
1. Disconnect the electrical con-
nection of the motor.
2. Remove the protection grille
with fan from the housing.
3. Remove the protection grille
from the fan motor.
4. Carefully refit the new fan in
reverse order.
5. Check the fan impeller for
smooth operation and freedom
of movement with respect to
the fan housing.
6. Re-establish the electrical con-
nection of the motor correctly.
Replacement of
fin heat exchanger
1. Disconnect the electrical con-
nection of the unit.
2. Shut-off the water-sided unit
connection.
3. Drain the fin heat exchanger
completely and disconnect the
heating medium connections.
4. Remove any fitted air inlet and
air outlet accessories and re-
move the unit from the bracket
(support).
5. Remove the rear wall (support
plate) together with the fan.
6. Loosen the fin heat exchanger
fastening screws and remove
the heat exchanger towards the
air inlet side.
7. Fit the new heat exchanger and
reassemble the unit in reverse
order including accessories.
8. Re-establish electrical connec-
tions.
Checks after repairs:
■
The fan impeller must rotate
freely in the fan housing
■
The distance between the fan
impeller and fan housing must
be the same
■
The fan motor must rotate in
the direction of the arrow and
connected in correct phase
■
All screw connections must be
checked for tightness
AttENtiON
After completing all work on
the units, an electrical safety
test must be carried out in
accordance with VDE 0701.
NOtE
Repair and maintenance work
must only be carried out by
authorised specialists.