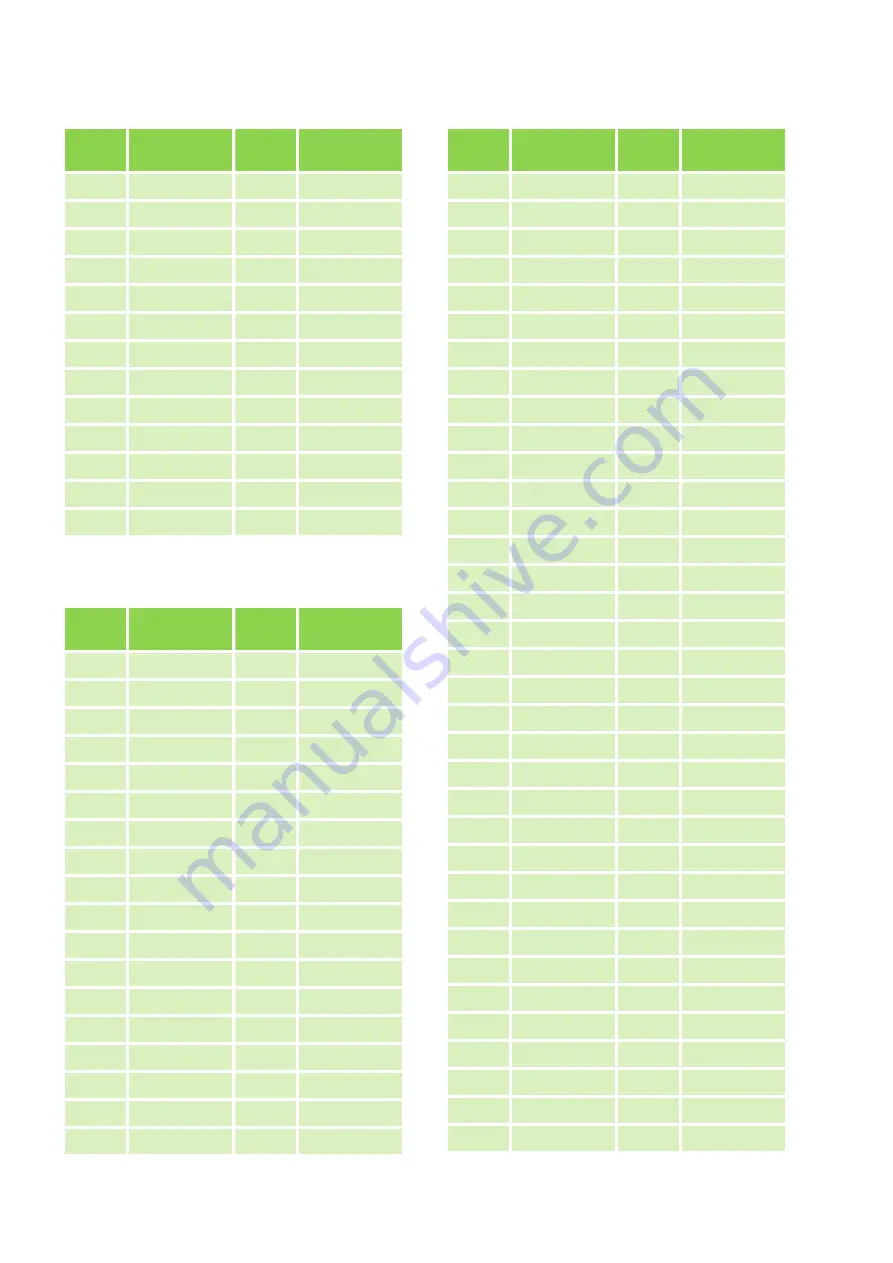
Temp.
(°C)
Resistance
(k
W
)
Temp.
(°C)
Resistance
(k
W
)
114
0.42
127
0.30
115
0.41
128
0.29
116
0.40
129
0.28
117
0.39
130
0.28
118
0.38
131
0.27
119
0.37
132
0.26
120
0.36
133
0.26
121
0.35
134
0.25
122
0.34
135
0.25
123
0.33
136
0.24
124
0.32
137
0.23
125
0.32
138
0.23
126
0.31
139
0.22
Probe T5
Temp.
(°C)
Resistance
(k
W
)
Temp.
(°C)
Resistance
(k
W
)
-20
542.7
-2
200.7
-19
511.9
-1
190.5
-18
483.0
0
180.9
-17
455.9
1
171.9
-16
430.5
2
163.3
-15
406.7
3
155.2
-14
384.3
4
147.6
-13
363.3
5
140.4
-12
343.6
6
133.5
-11
325.1
7
127.1
-10
307.7
8
121.0
-9
291.3
9
115.2
-8
275.9
10
109.8
-7
261.4
11
104.6
-6
247.8
12
99.69
-5
234.9
13
95.05
-4
222.8
14
90.66
-3
211.4
15
86.49
Temp.
(°C)
Resistance
(k
W
)
Temp.
(°C)
Resistance
(k
W
)
16
82.54
51
18.96
17
78.79
52
18.26
18
75.24
53
17.58
19
71.86
54
16.94
20
68.66
55
16.32
21
65.62
56
15.73
22
62.73
57
15.16
23
59.98
58
14.62
24
57.37
59
14.09
25
54.89
60
13.59
26
52.53
61
13.11
27
50.28
62
12.65
28
48.14
63
12.21
29
46.11
64
11.79
30
44.17
65
11.38
31
42.33
66
10.99
32
40.57
67
10.61
33
38.89
68
10.25
34
37.30
69
9.90
35
35.78
70
9.57
36
34.32
71
9.25
37
32.94
72
8.94
38
31.62
73
8.64
39
30.36
74
8.36
40
29.15
75
8.08
41
28.00
76
7.82
42
26.90
77
7.57
43
25.86
78
7.32
44
24.85
79
7.09
45
23.89
80
6.86
46
22.89
81
6.64
47
22.10
82
6.43
48
21.26
83
6.23
49
20.46
84
6.03
50
19.69
85
5.84
REMKO ML series
58