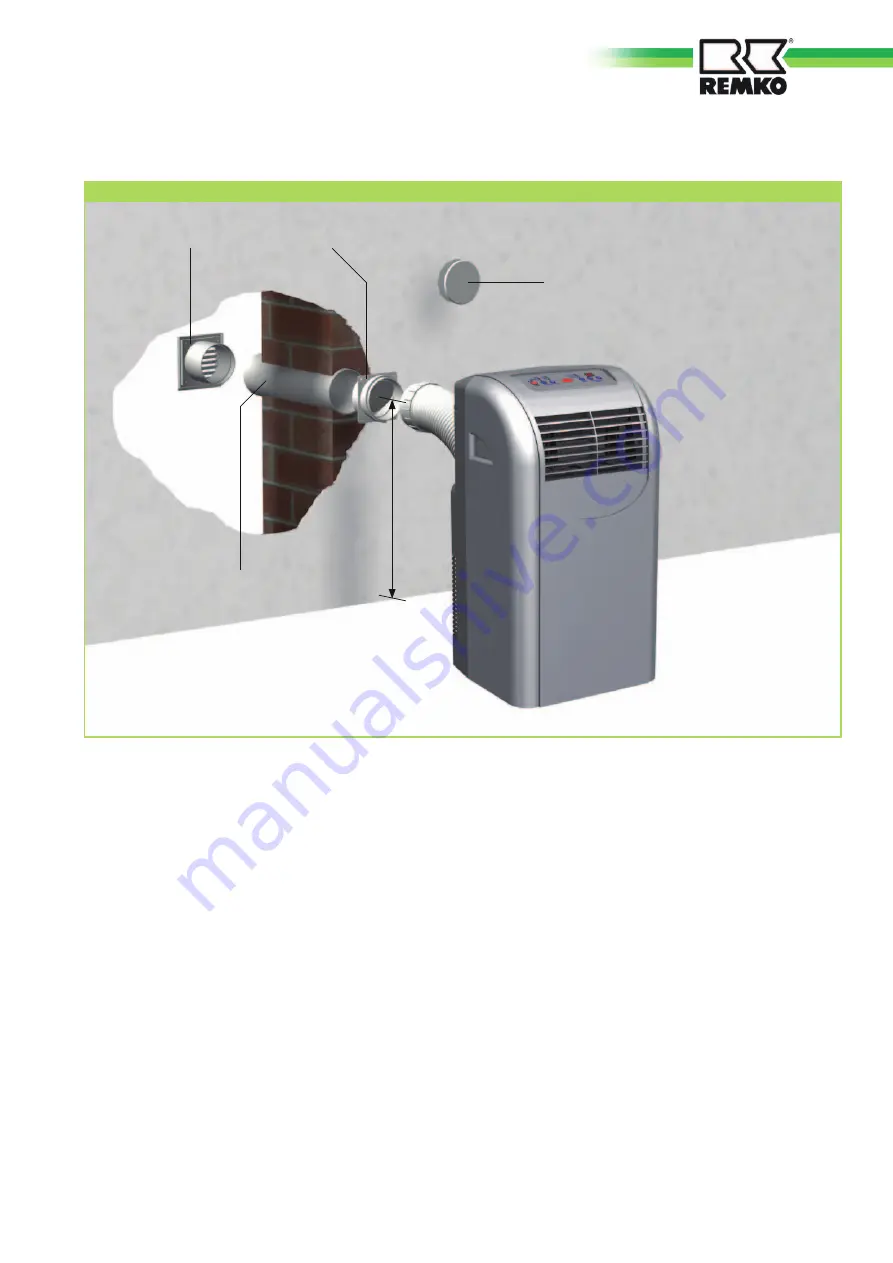
Installation scheme of the wall through (optional)
Installation Instructions
1. Create a core hole in the out-
side wall (max.- wall thickness
of 480 mm) with a diameter of
at least 135 mm.
Note possible supply lines in
this area!
2. Insert the telescopic pipe in the
created wall opening so that is
the outer pipe (large diameter)
on the inside wall.
To prevent cold bridges, insu-
late the telescopic pipe with
suitable insulating material.
3. Wall the telescopic pipe into the
core hole in such a way that it is
flush to both sides of the wall.
4. Mount the protection grill on
the outside of the wall with 4
screws (make sure it is protect-
ed from rain).
5. Fix the trap to the inside and
mount it with 4 screws..
The “top“ label on the trap
must be legible from the inside!
6. When taking the device out
of service, for example, at the
beginning of winter, close the
opening of the trap using the
sealing cap to prevent air circu-
lation.
Sealing cap
Trap
Protection grill
Telescopic pipe
min. 400 mm
Installation example
11