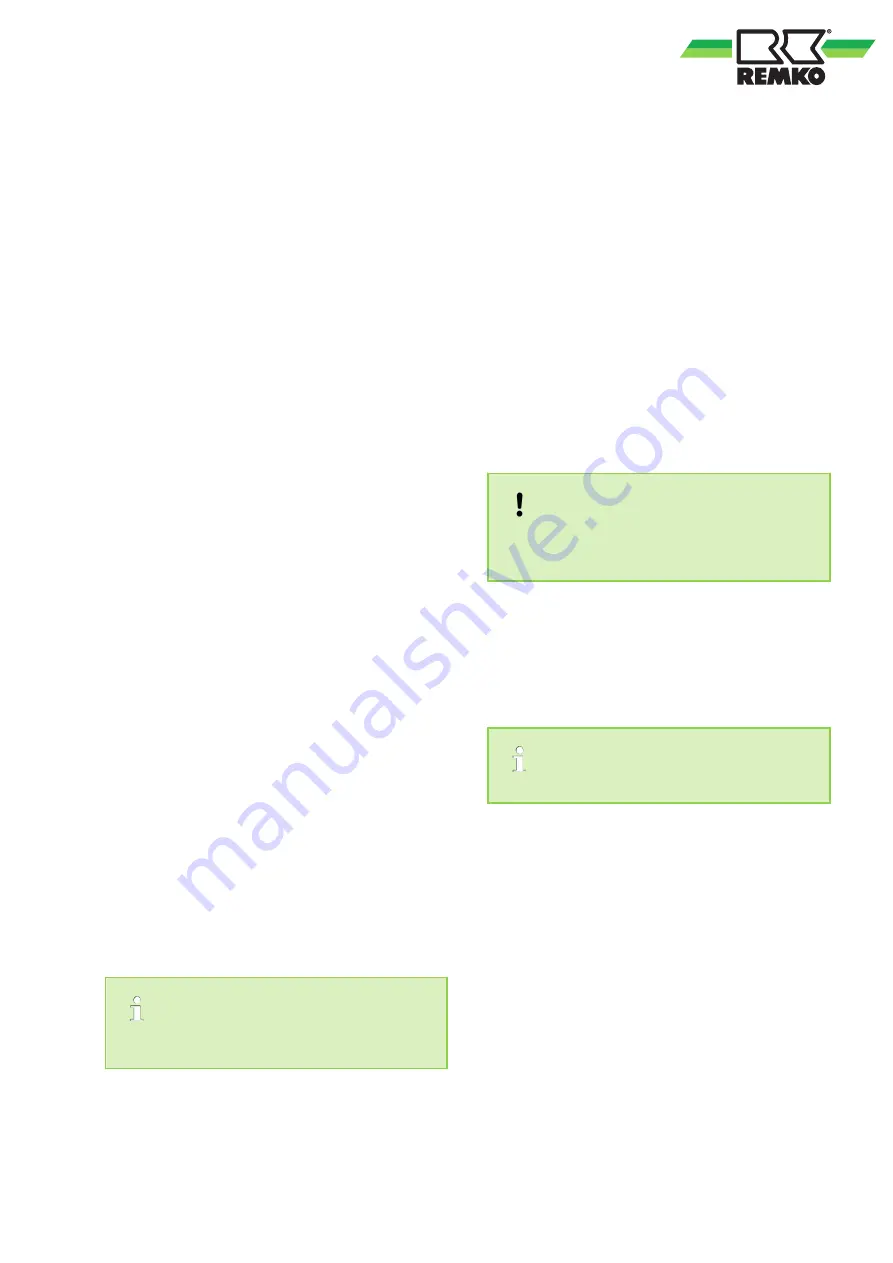
2-conductor system for cooling and heating
As the 2-conductor system must cool and heat
equally, for reasons of convection during winter
operation, a valve assembly is stipulated for all
installation methods for this system operation to
avoid undesirable heat emission.
4-conductor system for cooling and heating
As the 4-conductor system must cool and heat
equally, two valve assemblies are stipulated for this
system operation for the cooling and heating reg-
ister.
Connection of the medium pipings
n
The connection of the lines on-site takes place
on the rear or underside of the unit.
n
For the purpose of servicing, connections must
be equipped with shut-off valves and the
medium flow rate adjusted using valves for
hydronic balancing.
n
Additional automatic bleed valves are to be
provided in the supply and return flow at the
installation’s highest point.
n
The medium pipings may not exert any struc-
tural load on the unit.
n
The line connections may not generate any
thermal or mechanical stresses on the unit. If
necessary, cool the piping or support with the
second tool.
Necessary system components
Valve assembly for 2 or 4-conductor systems
(accessory)
In 2 or 4-conductor systems, cold or warm medium
is fed through the heat exchanger(s) into the unit
and cold or warm air can be discharged. Regula-
tion is provided by a 3-way valve assembly. It con-
sists of the electrically actuated valve head and the
valve body. If the head is electrically activated, it
actuates the body, which routes the medium into
the register. If the temperature is reached, the
head is switched off and the medium is fed past
the heat exchanger through the bypass. The
bypass serves to ensure the minimum medium
flow rate for the chiller.
The time between being fully open and fully
closed can be approx. three minutes.
Valves for hydronic balancing
The calculated individual pressure losses in the
pipeline network layout for each individual unit are
adjusted to the entire system with hydronic bal-
ancing valves to be provided by the customer. The
nominal flow rates for the medium adjust to the
values needed as a consequence of the pressure
loss.
Anti-freeze protection (accessories)
A water glycol mix is generally used as the medium
for a cold water system. Depending on the glycol
type and quantity used, the viscosity changes, the
pressure loss increases and the unit's cooling or
heating capacity reduces.
All system components must be approved for use
with glycol.
NOTICE!
The product and safety data sheets of the
glycol type used must be observed during use
and disposal.
Diaphragm expansion vessel (MAG)
To avoid pressure fluctuations during standstill
because of temperature changes, diaphragm
expansion vessels filled with nitrogen (moisture
neutral) must be integrated in the system.
No moisture can condense in the nitrogen filler.
Safety valve
Safety valves limit excess operating pressure due
to excess warming or overfilling of the operating
medium. The valve outlet requires unobstructed
draining into a drain line. Applicable local disposal
ordinances must be observed if glycol is used.
Automatic bleed valves
The unit has one or two manual bleed valves on
the collector pipe of the register. The unit can be
bled separately after the system has been filled.
Automatic bleed valves must also be installed at
the next highest point in the collective lines.
23