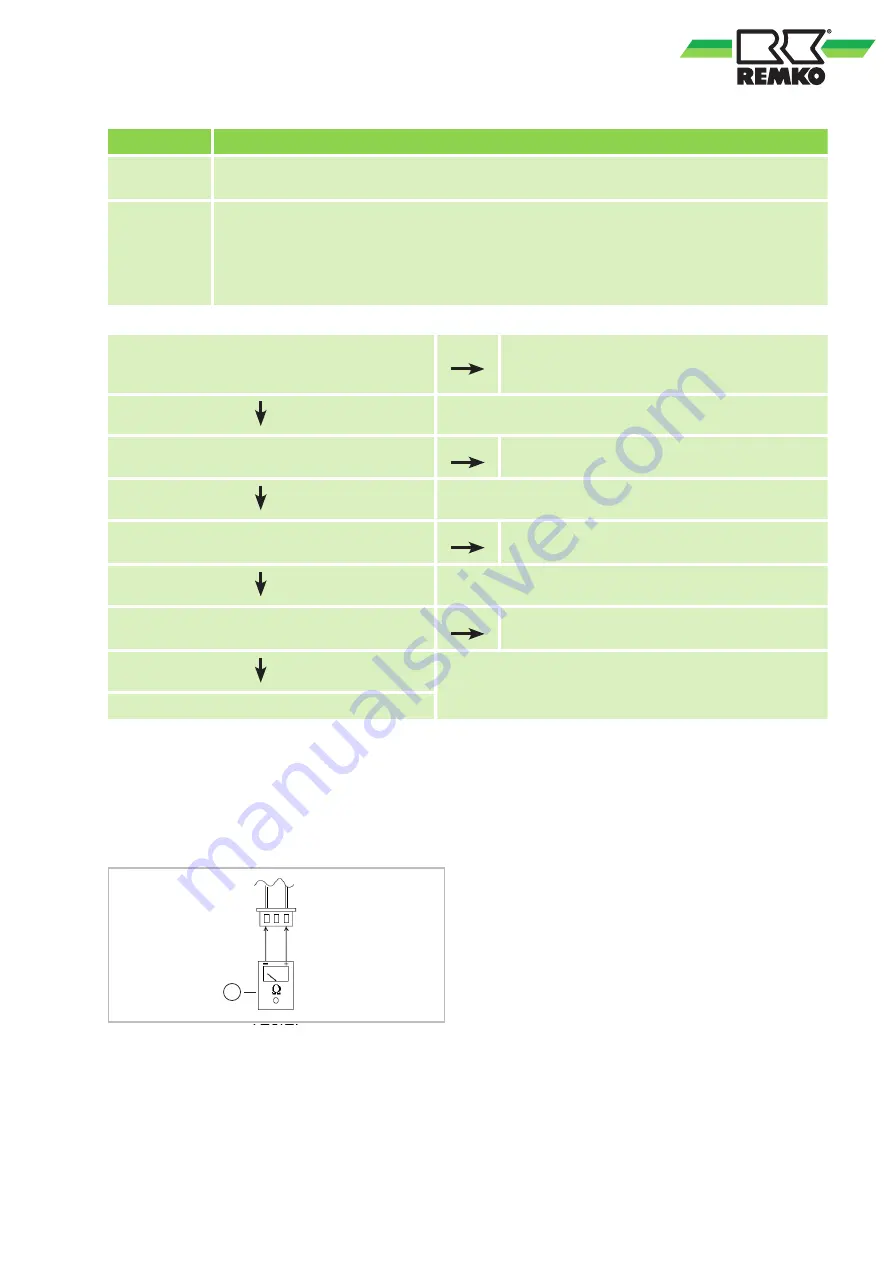
Error code:
P4
Reason:
Safety shutdown of inverter controller. Internal system monitoring triggered (e.g. communi-
cation problem between board and compressor, the compressor speed is not OK)
Cause:
n
Faulty electrical connections
n
Inverter regulation on board defective
n
Condenser fan motor defective
n
Compressor defective
n
Control board defective
Check the electrical connection between the
control board and compressor. Are these cor-
rectly implemented?
YES
Establish a proper connection.
NO
Check the inverter controller. Is this functional?
NO
Replace the control board.
YES
Check the condenser fan motor. Is it OK?
NO
Follow the instructions for troubleshooting fault
F5
YES
Check the winding resistances of the com-
pressor. Are they OK?
NO
Replace the compressor
YES
Replace the control boards of the outdoor unit.
Check individual components
Check the temperature probes
Disconnect the temperature probe from the control
board and measure the resistance on the plug's
contacts.
1
Fig. 46: Check temperature probes
1: Multimeter
49