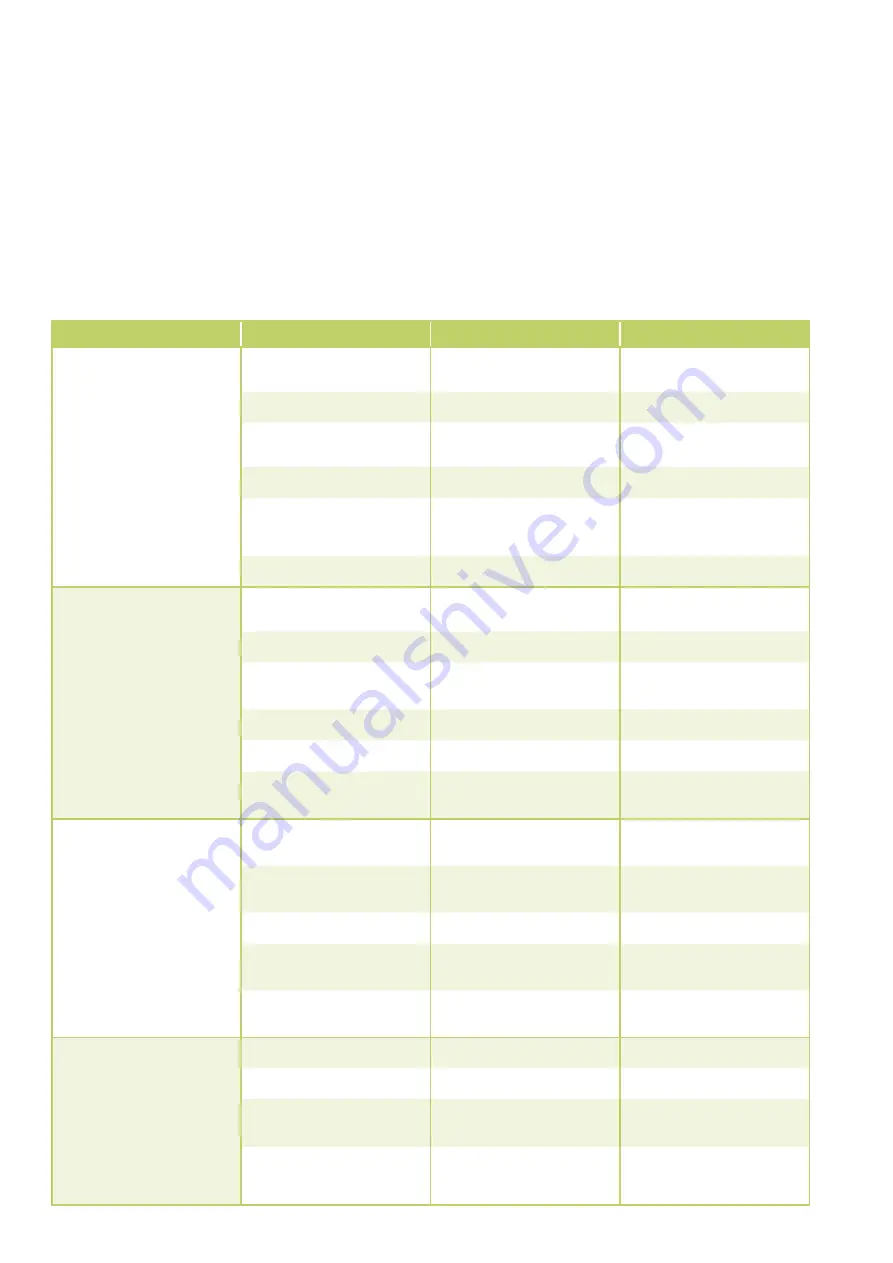
Troubleshooting and Customer service
The units and components are manufactured with the most up-do-date manufacturing methods and are checked
several times for proper function. However, should a functional problems occur, please check the function
according to the chart below. When all functional checks have been completed and the unit still does not work
properly, please contact your dealer!
Problem
Possible cause
Check
Remedy
The unit does not start or does
not turn off by itself.
Power failure, low voltage, main
fuse defective / main switch
turned off.
Are all other electrical devices
working?
Check voltage, possible wait until
turned on again.
Power line damaged.
Are all other electrical devices
working?
Repair by certified service center.
Waiting time after turn on too
short.
Have 5 minutes passed after
restart?
Plan for longer waiting period.
Operating temperature fallen
below / exceeded.
Do the fans on interior unit and
exterior unit work?
Observe temperature ranges of
interior unit and exterior unit.
Power surge due to thunderstorm. Were there any lightning strikes
nearby lately?
Shut off main fuse and turn on
again.
Inspection by certified service
center.
Problem of external condensation
pump.
Did the pump turn off due to a
problem?
Check or clean the pump, if
necessary.
The unit does not react to
remote control.
Transmission distance too large /
receiving problem.
Is there a signal sound on the
interior unit when pressing the
button?
Reduce the distance to less than
6 m and change location.
Remote control is defective.
Is the unit working in manual
operation?
Replace remote control.
Receiver and transmitter are
exposed to too much sun
exposure.
Is it working in shade?
Shade the transmitter and receiver.
Electromagnetic fields disrupt the
transmission.
Is it working after turning any
possible interfering sources off?
No signal transfer at simultaneous
operation of interfering sources.
Button of remote control stuck /
dual button control.
Does the “Send” symbol appear in
the display?
Release the button / press only
one button.
Batteries of remote control are
discharged.
Have new batteries been inserted?
Is the display incomplete?
Insert new batteries.
The unit works at reduced or
no cooling output.
Filter is dirty / air inlet / outlet
opening is blocked by debris.
Have the filters been cleaned?
Clean filters.
Windows and doors are open.
Heating or cooling load has
increased.
Have there been any
constructional / user changes?
Close windows and doors / install
additional systems.
No cooling operation is set.
Is the cooling symbol in the
display activated?
Correct the adjustment of the unit.
Fins of the exterior unit are
blocked by foreign matter.
Does the fan of the exterior unit
work? Are the evaporator fins
clear?
Check fan or winter regulation,
reduce air resistance.
Leaks in refrigerant circuit.
Is frost formation visible on
connections of the exterior unit?
Repair by certified service center.
Condensation discharge on unit.
Drain pipe of collector reservoir
plugged / damaged.
Is unrestricted condensation
discharge ensured?
Cleaning of drain pipe and
collector reservoir.
External condensation pump or
floater defective.
Is the catch pan full of water and
the pump is not working?
Have pump replaced by certified
service center.
Non-discharged condensation is in
the condensation line.
Is the condensation line routed
downward or not plugged?
Route the condensation line
downward or clean it.
Condensation cannot be
discharged.
Are the condensation lines clear
and routed downward? Does the
condensation pump and the floater
switch work?
Route the condensation line
downward or clean it. If the floater
switch or the condensation pump is
defective, have them replaced.
Functional problem
REMKO ATY
16
Summary of Contents for ATY 260
Page 2: ......