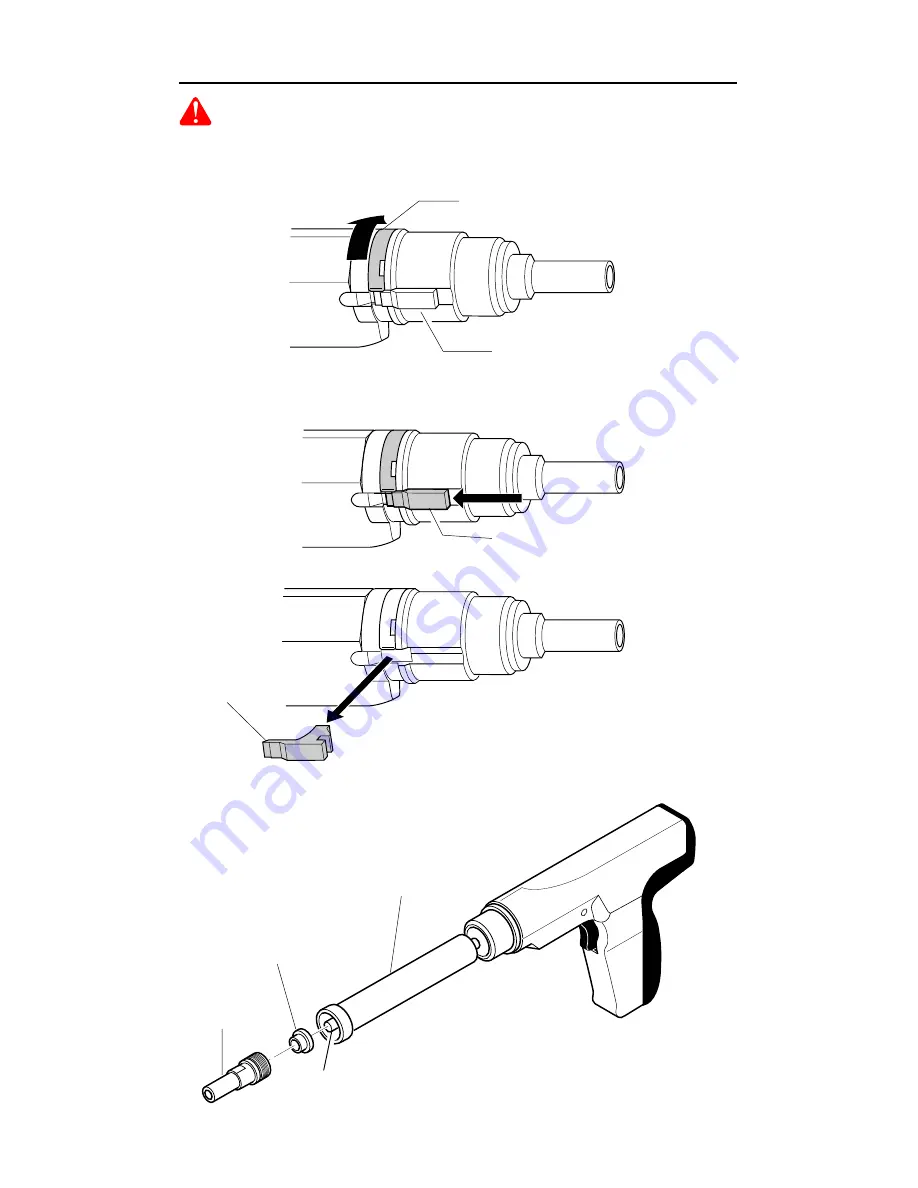
18
105635
Tool Disassembly
Figure 2 - Removing Stop
Stop
A. REMOVING BARREL ASSEMBLY
1. Using screwdriver, lift end of annular spring and rotate spring until stop is
uncovered (see Figure 1).
Annular Spring
WARNING: Always unload a powder actuated tool before disassembling,
replacing barrel, cleaning, or assembling.
Stop
3. Pull barrel assembly out of housing.
4. Unscrew muzzle cap.
5. Pull buffer out of muzzle cap (see Figure 3).
Figure 3 - Separating Barrel Assembly from Housing
Stop
Muzzle Cap
Buffer
Barrel
Piston
Figure 1 - Rotating Annular Spring to Uncover Stop
2. Push stop towards rear of tool and remove (see Figure 2).