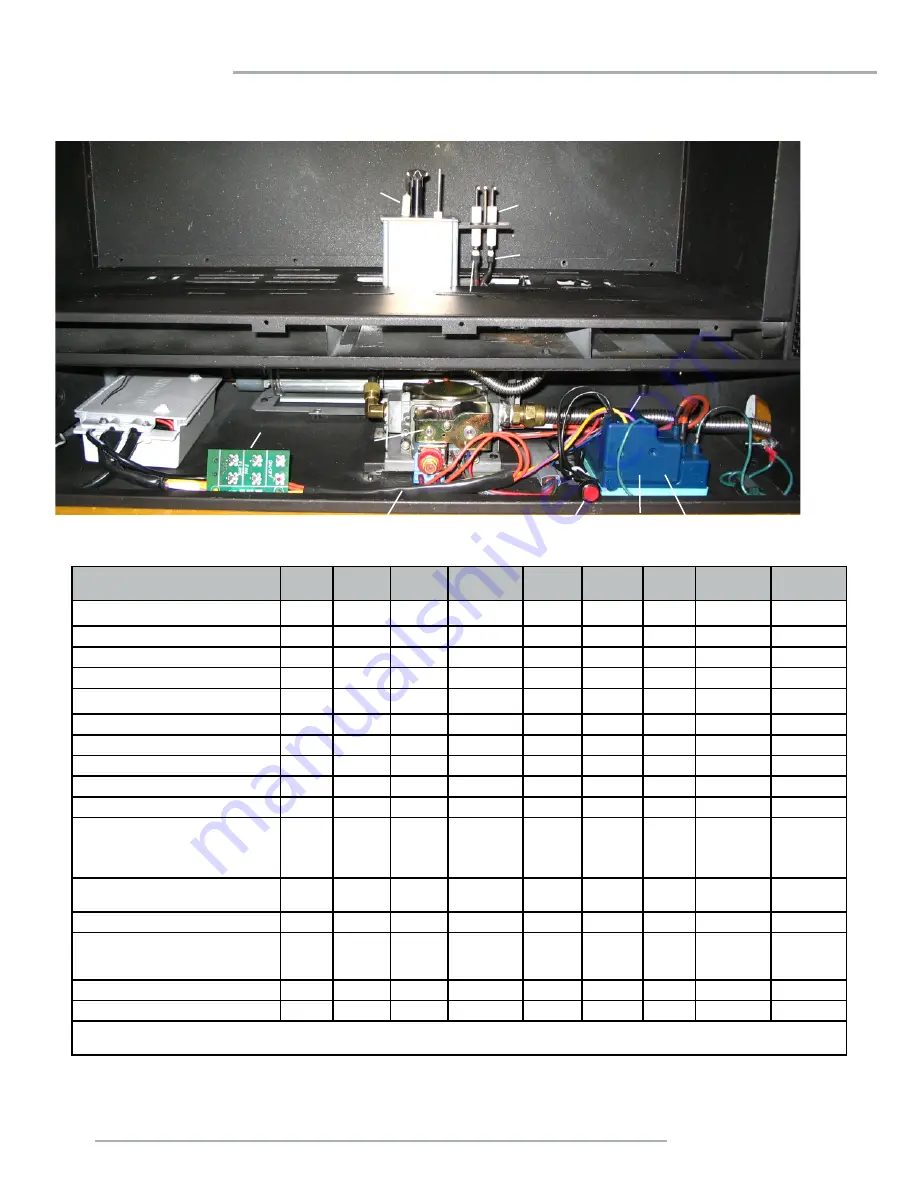
50
Regency GF900L-1 Gas Fireplace
PARTS LIST
parts list
ELECTRONIC COMPONENTS PARTS LIST
Note:
Depending on the model, the diagram below may not be exactly as shown - for reference purposes only.
910-936
910-082
910-088
910-089
910-084
910-101
910-526
910-080
910-521, 910-522, 910-523
910-912
910-083
911-121
910-514
FG38
FG39
PG33
PG36 /
PG36D
PG121/
PG131
GFI300L
IG34
GF900L/C
GF1500L
910-909
Fan Resistor
910-936
Intermittent Pilot
N/A
N/A
N/A
911-146
Intermittent Pilot
N/A
N/A
N/A
N/A
N/A
N/A
N/A
910-082
Direct Spark Ignitor
N/A
N/A
N/A
N/A
N/A
N/A
N/A
N/A
910-089
Flame Cable
N/A
N/A
N/A
N/A
N/A
N/A
N/A
N/A
910-088
Spark Cable
N/A
N/A
N/A
N/A
N/A
N/A
N/A
N/A
910-084
Control Box
N/A
N/A
N/A
911-101
Control Box
N/A
N/A
N/A
N/A
N/A
N/A
910-527
Manual Control Switch
N/A
N/A
N/A
N/A
N/A
N/A
910-080
Valve
910-521
Control Box Cable
(1)
910-522
Control Box Cable
(2)
910-523
Control Box Cable
(3)
910-525
Control Box Cable
(4)
*N/A
(2)
(1)
(1)
(3)
N/A
(2)
N/A
N/A
910-912
Ignition Module to Valve
Cable
N/A
N/A
911-183
Reset Switch
N/A
910-083
Ignition Module
(1)
911-121
Ignition Module
(2)
(1)
(2)
(2)
(2)
(2)
(2)
(2)
(2)
(2)
(2)
910-514
Jumper Wire
N/A
910-935
Manual Control Switch
N/A
N/A
N/A
N/A
N/A
**Note:
The Control Box Cable wires for the FG38 come separately: 910-502, 910-505, 910-506, 910-507, 910-509
911-183