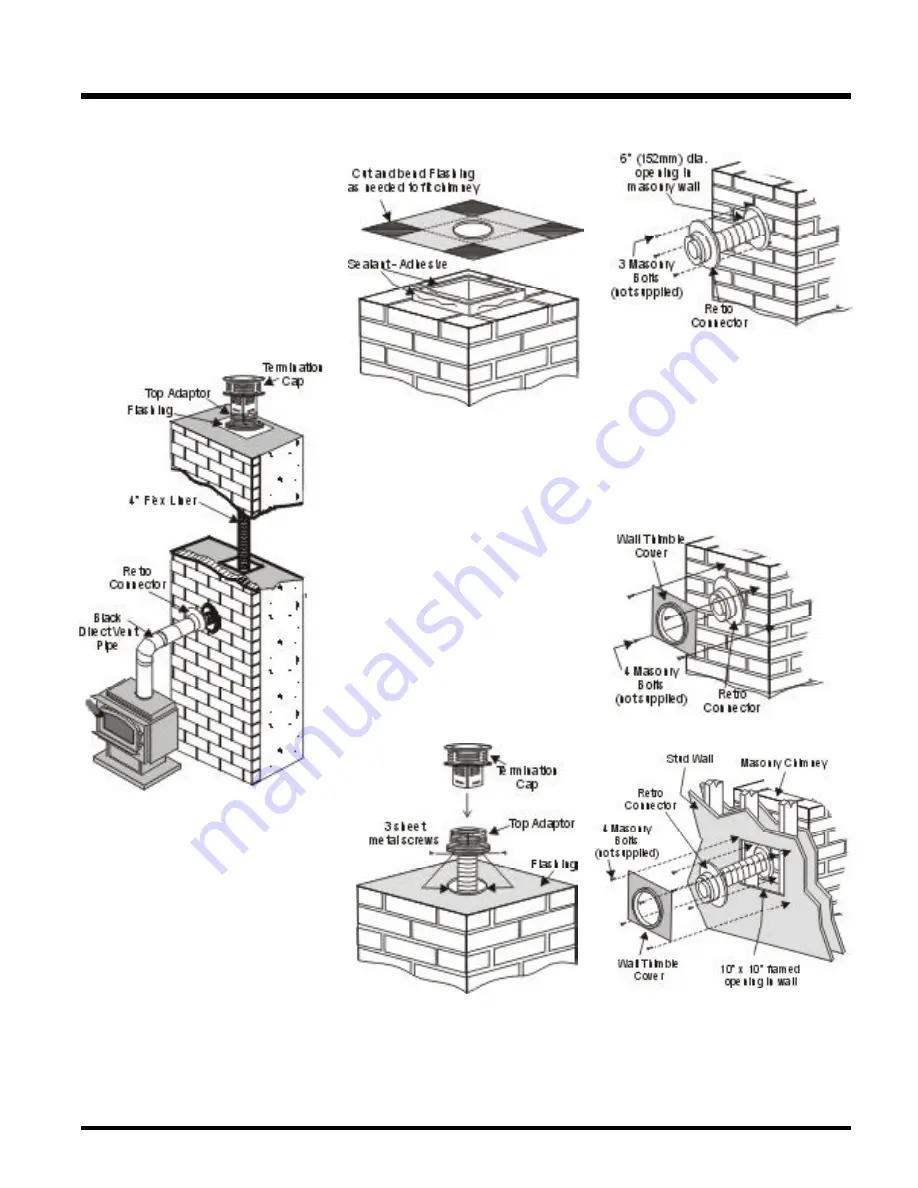
Regency CLASSIC C34-2 Direct Vent Freestanding Gas Heater
23
INSTALLATION
7) The connection between the appliance and
the Retro Connector may be completed with
sections of black direct vent pipe, together
with an adjustable length.
Converting a Masonry Chimney
Important: The existing masonry flue
opening needs to have an area of at least
a 36 sq. in. to insure proper intake/ex-
haust flow.
1) Before cutting any holes, assemble the
desired sections of black direct vent pipe to
determine the center of the masonry pene-
tration.
Diagram 6
2) Once the center point of the penetration has
been determined, cut a 6" (152mm) dia. hole
in the masonry. Be careful, if the hole is too
large, the Retro Connector might not mount
properly, and if the hole is too small, then the
appliance might starve for intake air. If there
is a frame wall in front of the masonry wall,
cut and frame a 10" (254mm) clear square
opening in the wall (centered around the 6"
(152mm) masonry opening). If there is sheet
rock only (no studs) in front of the masonry,
the 10" (254mm) clear opening is still need-
ed, but does not need to be framed. This
allows the Retro Connector to mount direct-
ly on the masonry and provide clearance to
the combustibles. Diagram 11.
3) Secure the Flashing (Part # 705C) to the top
of the masonry chimney using a bead of
non-hardening sealant-adhesive. IF the
Flashing is larger than the top of the chim-
ney, then cut and fold flashing as needed
to fit chimney. Diagram 7.
Diagram 7
4) To determine the length of flex required,
measure from 3" (76mm) above the top of
the Flashing down to the level of the open-
ing. Add to this measurement the distance
from the center of the chimney to out through
the wall. Cut a piece of 4" flex to this length
(the flex should already be extended to its
nominal length).
5) Connect the 4" flex liner to the Top Adaptor
(Part # 985K) using 3 sheet metal screws.
Diagram 2.
6) Feed the 4" flex liner through the Flashing
into the chimney. Continue to feed the liner
out through the opening in the masonry wall.
7) Secure the Top Adaptor to the Flashing. Use
3 sheet metal screws through the side of the
adaptor into the flange on the Flashing
(diagram 8). Twist lock the Termination Cap
(Part # 980 or 991) on to the Top Adaptor.
and the mounting holes line up with the
masonry wall.
Diagram 8
Diagram 9
9) Slide the Wall Thimble Cover (Part # 940)
over the Retro Connector and secure with
masonry bolts. Diagram 10. If you have a
framed wall in front of the masonry, use
wood screws to mount the Wall Thimble
Cover to the framed wall, over the Retro
Connector and the 10" (254mm) square
framed opening. Diagram 11. If needed, add
a section of direct vent pipe to the Retro
Connector in order to extend through the
opening in the Wall Thimble Cover.
Diagram 10
8) Attach the flex to the Retro Connector. Use
3 sheet metal screws to attach the flex liner
to the Connector. Diagram 9. Mount the
Retro Connector to the masonry wall using
masonry bolts. Re-drill larger holes on con-
nector as needed. Be careful to insure that
the connector is centered in the opening
10) The connection between the appliance and
the Retro Connector may be completed
with a section of black direct vent pipe,
together with an adjustable length pipe
section.
Diagram 11