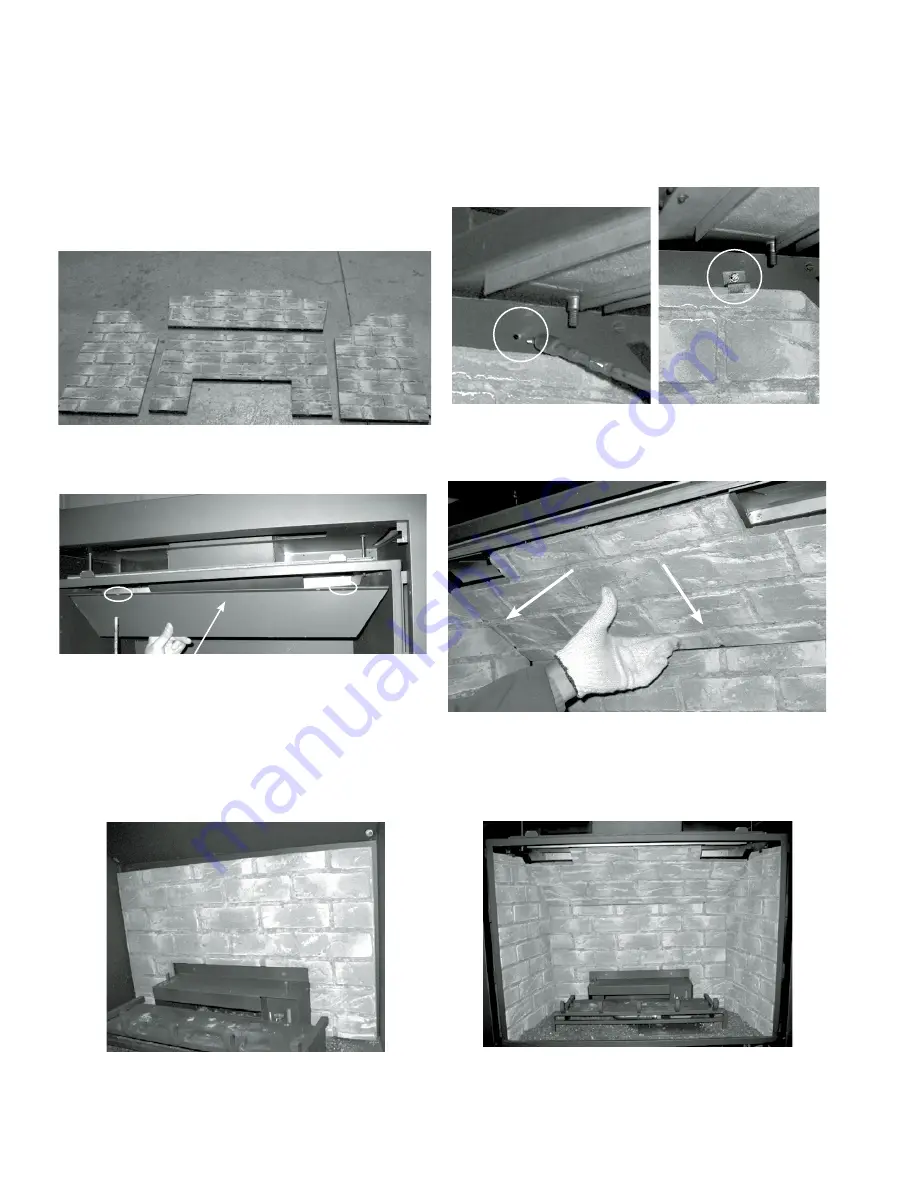
Bellavista
®
B36XTCE-10 Gas Fireplace
|
41
|
41
installation
918-774
09/02/08
1
B36X/XT
BRICK PANEL INSTALLATION
Dangerous operating conditions may occur if the panels are broken.
Handle with care. DO NOT FORCE INTO POSITION.
1)
Unwrap the Brick Panels from the protective wrapping.
2) Ensure that the logs are not in the unit.
3)
Remove the heat defl ector (if installed) by removing the 2 screws
securing the heat defl ector from the top of the fi rebox.
4)
Install the back brick panel fi rst - use caution when clearing the
burner assembly and rear log tray so the panel is not damaged.
Note:
Ensure that an equal space (gap) is maintained on both
the right and left side - when installing the back panel.
5)
Remove the hex head screw on the upper left side of the fi rebox
wall.
Position left brick panel in place and secure with the brick panel clip
and screw.
6)
Slide top brick panel under left and back brick panel, use care not
to damage panel.
7)
Right brick panel is installed last, follow the same procedure as for
left panel (see step 5).
Left Panel
Right Panel
Back Panel
Top Panel
Back Panel Installed
Final Brick Panel Installation
Heat defl ector
8)
Reinstall top heat defl ector (reverse Step 3).
BRICK PANEL INSTALLATION