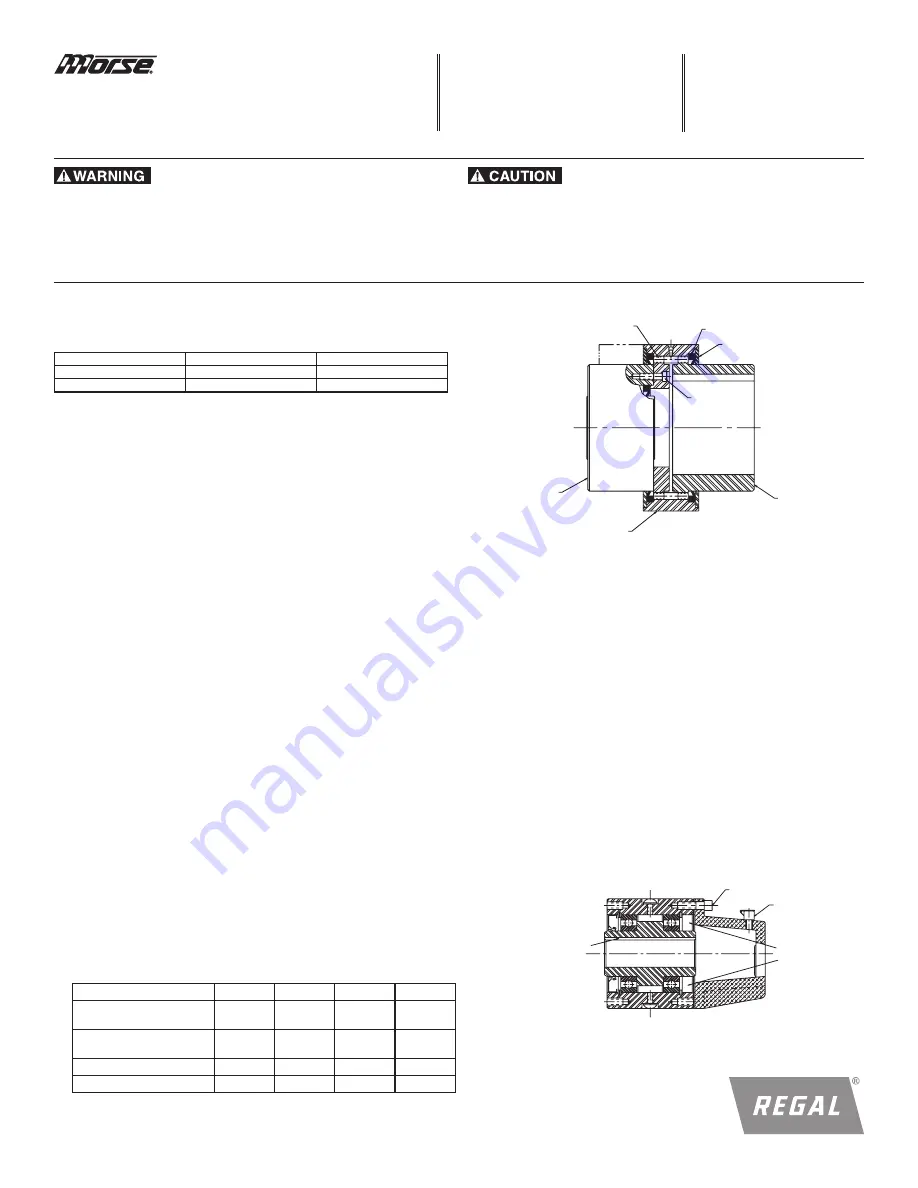
1
F O R M
“M” Series Clutches
Installation and Maintenance Instructions
for Models 750 – 1000
PN 654027, PS-740-0001
4146-002AE
Revised
October 2016
A. Preinstallation
1.
It is very important that the clutch fit the shaft properly. The following are
recommended shaft tolerances.
2.
On applications where a press fit is necessary, do not exceed .001 inch.
3.
Should a .001 inch maximum press fit be required, immerse clutch in hot,
clean oil (not to exceed 200° F.) for several minutes before mounting.
4.
To minimize critical stresses in the keyway area of the inner race, the clutch
keyways have a radius in the corners. A key designed to match this keyway
is furnished with each clutch. Use this key in mounting clutch on shaft, as
key must support full length of clutch inner race. A tight fit on key width is
necessary on indexing applications.
5.
Orient clutch as though in operating position and check for proper rotation. Oil
lubricated clutches should be mounted on horizontal shafts only. Refer vertical
shaft applications to factory.
B. Installation
1.
When mounting the clutch and key on the shaft, apply pressure to the end
face of the inner race only as bearing damage could result from pressure
being applied to the outer race. Note: Caution should be exercised in installing
the clutch to prevent damaging the seals.
2.
Since the key has a venting groove, make certain that the side of the key with
the groove is at the top of the clutch keyway.
3.
Secure clutch in position on shaft. Use lock washers, snap rings, collars,
adjacent components or similar items to hold clutch in position.
4.
Overrun (freewheel) the clutch by hand before subjecting to test operation.
Before using the clutch fill with proper lubricant. (Refer to the lubrication
section.)
5.
This additional step is applicable to the cam clutch coupling only:
a.
Never use the clutch as a coupling. When the connection of two shafts
is required in conjunction with a clutch, use a clutch-coupling.
b.
After mounting the clutch per the above steps, follow these steps to
correctly install the coupling.
1. Slide the ring assembly onto clutch.
2. Attach the plate gear to clutch using capscrews provided.
3. Place seal and retainer plate on hub gear.
4. Mount hub gear on shaft.
5. Position units to be connected allowing 11/16 inch between plate
gear and hub gear.
6. Align gears with straight edge or taper gauge. Align shafts as
accurately as possible to obtain the maximum service life from the
coupling.
7. Hand pack external gears with #1 or #2 ball bearing grease, forcing
some grease between the faces to provide a lubricant reservoir.
Repack these gears once a year.
8. Slide ring assembly over external gears and remove excess
lubricant.
9. Press in seal with flat object. Gently tap-in seal exercising care not
to damage.
10. Attach retainer plate with screws provided.
6.
This additional step is applicable only when oil reservoir is used with clutch.
a.
Reservoirs can only be used where the clutch outer race is held
stationary as in backstop applications.
b.
Clutches are shipped with oil seals in both ends of the clutch. Remove
the oil seal on the reservoir side with a screwdriver or similar instrument
being careful not to damage the clutch. Do this only after determining
the proper direction of rotation of the clutch. This seal should not be
reused because it is damaged by the removal process.
c.
Prior to mounting clutch on shaft, apply Permatex* or similar sealant to
clutch key and keyway. This prevents loss of oil through keyway.
d.
After mounting clutch on shaft per the above steps, attach reservoir to
the clutch end from which the seal has been removed, using capscrews
provided with reservoir. Position reservoir with oil fill on top side.
Clutch with Oil Reservoir
Remove
seal at
reservoir
end
Apply
Permatex
or
similar
sealant
Oil fill
Capscrews
Clutch Coupling
Seal
Retainer
plate
Hub gear
Ring assembly
Clutch
Capscrews
Plate gear
Nominal Diameter
Bore
Shaft
Over 2" to 4"
+ .0000 / -.0015"
-.0015 / -.0025"
4" to 6”
+ .0000 / -.0020"
-.0020 / -.0030"
Coupling Number
C-7.5
C-8
C-9
C-10
Maximum Angular
Misalignment
1/2°
1/2°
1/2°
1/2°
Maximum Parallel
Misalignment
.010"
.010"
.010"
.010"
Allowable End Float From
+1/4"
+1/4"
+1/4"
+1/4"
Nominal 11/16” Gap
-5/8"
-5/8"
-5/8"
-5/8"
Power Transmission Solutions
Regal Beloit America, Inc.
7120 New Buffington Road
Florence, KY 41042
Application Engineering: 800 626 2093
www.RegalPTS.com
• Periodic inspections should be performed. Failure to perform proper
maintenance can result in premature product failure and personal
injury.
• Read and follow all instructions carefully.
• Disconnect and lock-out power before installation and maintenance.
Working on or near energized equipment can result in severe injury or
death.
• Do not operate equipment without guards in place. Exposed
equipment can result in severe injury or death.