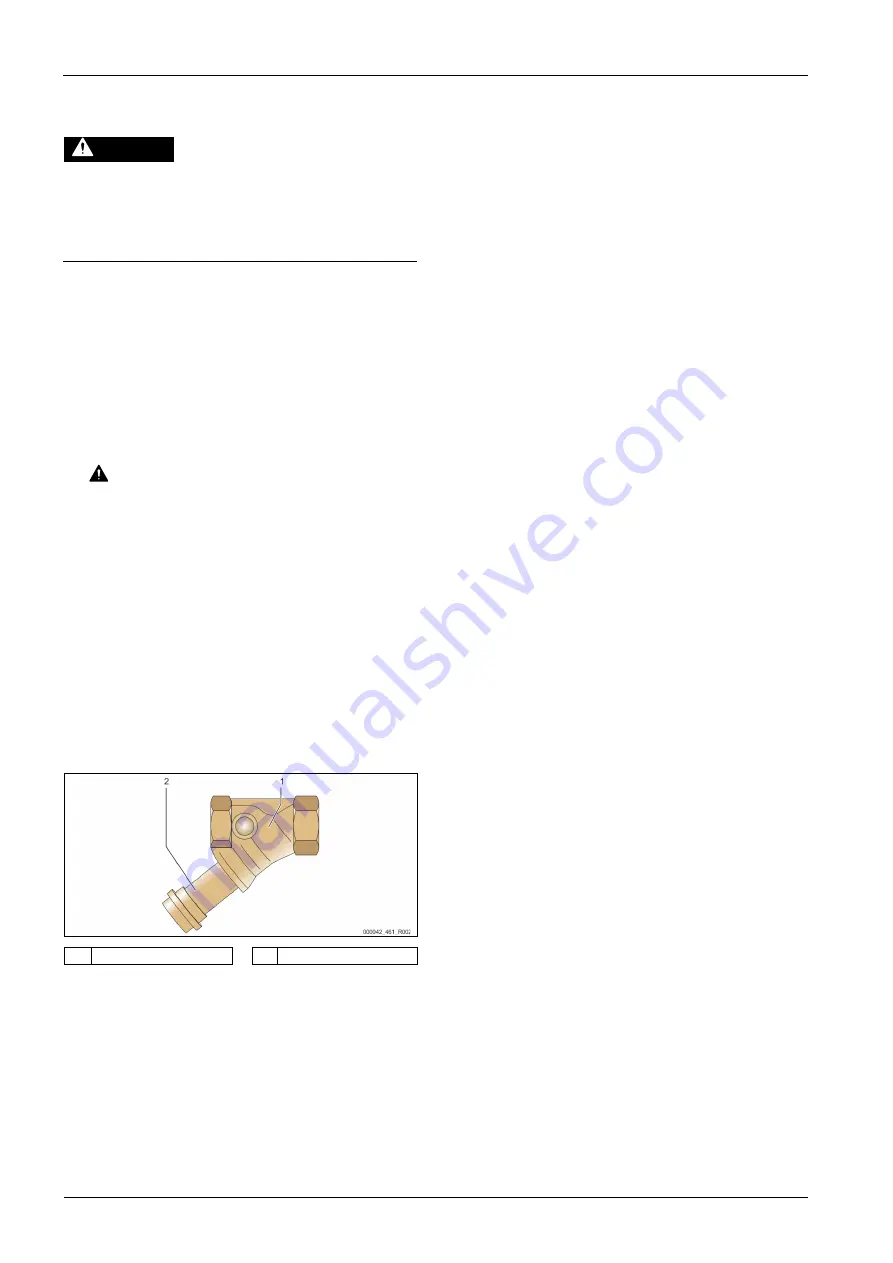
Maintenance
22 — English
— 03.09.2020 - Rev. A
11.3
Cleaning
11.3.1
Cleaning the tanks
CAUTION
Risk of injury due to pressurised liquid
Injuries can occur during maintenance work if the connections have been
installed incorrectly because condensate under pressure can suddenly
escape.
•
Ensure proper connections for the draining of condensate.
•
Wear suitable personal protective equipment (safety gloves and safety
goggles, for example).
Regularly clean the primary vessel and the secondary vessels to remove
condensate. The cleaning intervals depend on the local operational conditions.
Vessels with replaceable diaphragm
1.
Close the cap valve in front of the vessels.
2.
Record the displayed level value at the controller and empty the vessel of
water and compressed air.
3.
Switch off the main switch and withdraw the mains plug.
4.
Open the drain taps at the vessels and drain the condensate.
–
If more than 5 litres of water or condensate are discharged, you must
check the vessel.
•
Check the diaphragm for rupture.
•
Check the vessel interior walls for corrosion damage.
CAUTION – Risk of injury caused by escaping pressurised liquid.
Injuries can occur during maintenance work if the connections have been
installed incorrectly because condensate under pressure can suddenly
escape.
5.
Close the vessels' drain taps.
6.
Connect the mains plug and switch on the main switch.
7.
Open the cap valve of the vessels and secure against unauthorised
"closing".
8.
Fill water and compressed air into the vessels until the recorded level value
is reached.
Maintenance is completed.
Note!
Check the installation location of the vessels for sufficient ventilation if
the vessel interior wall are damaged by corrosion, see chapter 7.2
"Preparatory work" on page 9
11.3.2
Cleaning the dirt trap
Regularly clean the "ST" dirt trap. The cleaning intervals depend on the local
operational conditions.
1
"ST" dirt trap
2
Dirt trap insert
1.
Switch to Stop mode.
–
Press
"
Stop
"
on the controller's operator panel.
2.
Close the ball valves upstream and downstream of the "ST" (1) dirt trap.
3.
Slowly unscrew the dirt trap insert (2) from the dirt trap in order for the
residual pressure to escape from the pipeline segment.
4.
Pull the mesh from the dirt trap insert and rinse it with clear water. Use a
soft brush for cleaning.
5.
Re-insert the mesh into the dirt trap insert, check the gasket for damage,
and screw the dirt trap insert back into the housing of the "ST" (1) dirt trap.
6.
Re-open the ball valves upstream and downstream of the "ST" (1) dirt trap.
7.
Switch to Automatic mode.
–
Press "Auto" on the controller's operator panel.
Note!
Clean all other installed dirt traps (in the Reflex Fillset, for example).
11.4
Inspection
11.4.1
Pressure-bearing components
Comply with all applicable national regulations for the operation of pressure
equipment. De-pressurise all pressurised components prior to inspection (see
disassembly information).
11.4.2
Inspection prior to commissioning
In Germany, follow the Industrial Safety Regulation
[Betriebssicherheitsverordnung] Section 15 and Section 15 (3) in particular.
11.4.3
Inspection intervals
Recommended maximum inspection intervals for operation in Germany
pursuant to Section 16 of the Industrial Safety Regulation
[Betriebssicherheitsverordnung] and the vessel classification of the device in
diagram 2 of the Directive 2014/68/EC, applicable in strict compliance with the
Reflex Installation, Operation and Maintenance Manual.
External inspection:
No requirement according to Annex 2, Section 4, 5.8.
Internal inspection:
Maximum interval according to Annex 2, Section 4, 5 and 6; if necessary, suitable
replacement actions are to be taken (such as wall thickness measurement and
comparison with the design specification which may be requested from the
manufacturer).
Strength test:
Maximum interval according to Annex 2, Section 4, 5 and 6.
Furthermore, compliance with Section 16 of the Industrial Safety Regulation and
Section 16 (1) in particular, in conjunction with Annex 2, Section 4, 6.6 and
Annex 2, Section 4, 5.8, must be ensured.
The actual intervals must be specified by the operating company based on a
safety evaluation taking into consideration the actual operating conditions,
experience with the mode of operation and charging material and the applicable
national regulations for the operation of pressure equipment.
Cooke Industries - Phone: +64 9 579 2185 Email: [email protected] Web: www.cookeindustries.co.nz