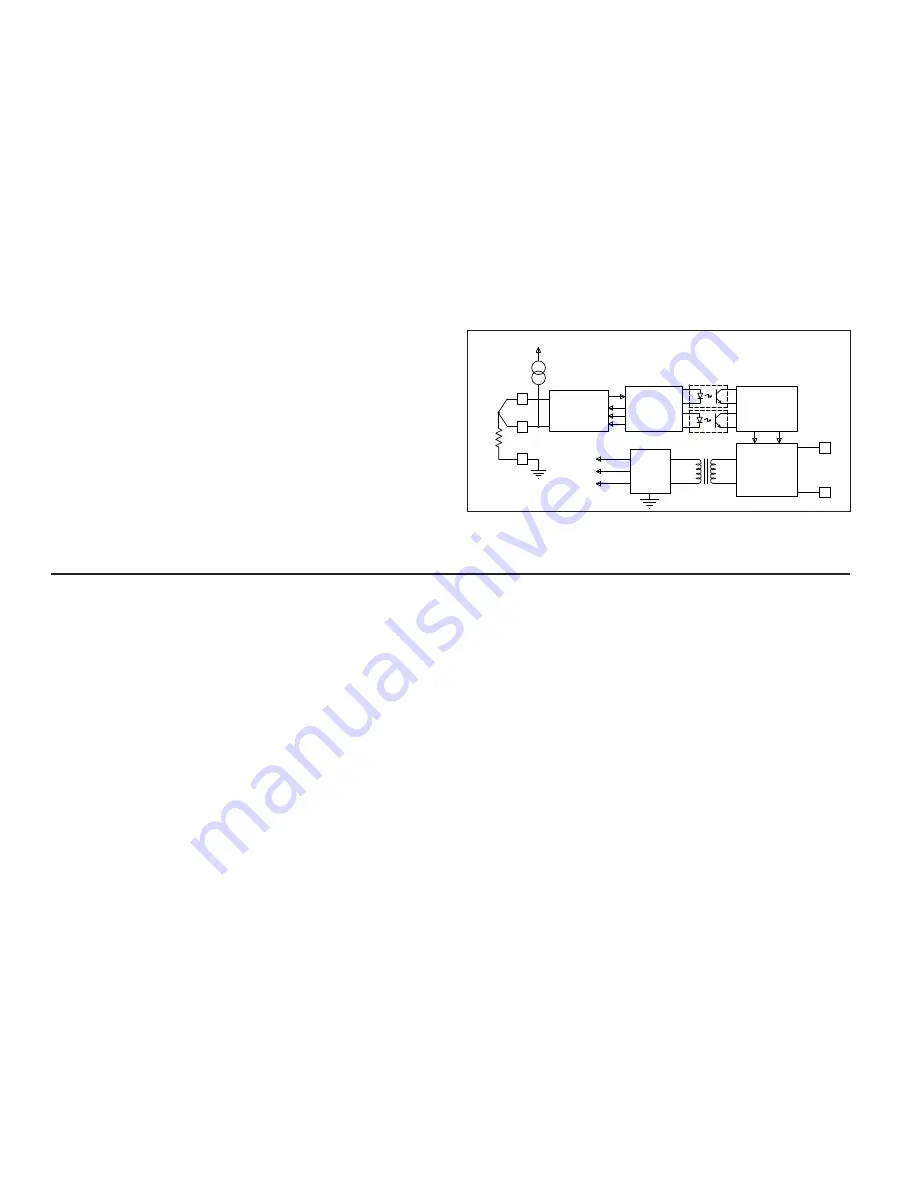
FUNCTION DESCRIPTIONS
Open Sensor Detection
The output can be set to go Upscale or Downscale for the detection of an
open sensor. The Upscale setting makes the output go to 22.5 mA (nominal).
The Downscale setting makes the output go to 3.5 mA (nominal). This setting
is always active, so changes in the setting are effective immediately.
Calibration Malfunction
If the unit has scaling problems (current remains at 3.5 mA nominal), check
the voltage between the RTD- Input (-) and TEST pad (+) [located next to the
DIP switches on the side of the unit]. For normal operation the voltage is 0 V
(nominal). If the voltage is +3 V(nominal), a problem occurred storing
information in the E
2
PROM. When this happens, perform a Basic Calibration
and then a Field Calibration. Turn off power for 5 seconds. Turn on power and
check the voltage between the TEST pad (+) and RTD- Input (-). If the voltage
is still +3 V(nominal), contact the factory.
EMC INSTALLATION GUIDELINES
Although this unit is designed with a high degree of immunity to
ElectroMagnetic Interference (EMI), proper installation and wiring methods
must be followed to ensure compatibility in each application. The type of
electrical noise, source or coupling method into the unit may be different for
various installations. In extremely high EMI environments, additional measures
may be needed. For the purpose of EMC testing, both input and output lines on
the unit were connected with 25 feet (8 m) of cable. Cable length, routing and
shield termination are very important and can mean the difference between a
successful or a troublesome installation. Listed below are some EMC guidelines
for successful installation in an industrial environment.
1. Use shielded (screened) cables for all Signal and Control inputs. The shield
(screen) pigtail connection should be made as short as possible. The
connection point for the shield depends somewhat upon the application.
Listed below are the recommended methods of connecting the shield, in order
of their effectiveness.
a. Connect the shield only at the rail where the unit is mounted to earth
ground (protective earth).
b. Connect the shield to earth ground at both ends of the cable, usually when
the noise source frequency is above 1 MHz.
c. Connect the shield to common of the unit and leave the other end of the
shield unconnected and insulated from earth ground.
2. Never run Signal or Control cables in the same conduit or raceway with AC
power lines, conductors feeding motors, solenoids, SCR controls, and
heaters, etc. The cables should be run in metal conduit that is properly
grounded. This is especially useful in applications where cable runs are long
and portable two-way radios are used in close proximity or if the installation
is near a commercial radio transmitter.
3. Signal or Control cables within an enclosure should be routed as far away as
possible from contactors, control relays, transformers, and other noisy
components.
4. In extremely high EMI environments, the use of external EMI suppression
devices, such as ferrite suppression cores, is effective. Install them on Signal
and Control cables as close to the unit as possible. Loop the cable through the
core several times or use multiple cores on each cable for additional
protection. Install line filters on the power input cable to the unit to suppress
power line interference. Install them near the power entry point of the
enclosure. The following EMI suppression devices (or equivalent) are
recommended:
Ferrite Suppression Cores for signal and control cables:
Fair-Rite # 0443167251 (RLC #FCOR0000)
TDK # ZCAT3035-1330A
Steward #28B2029-0A0
Line Filters for input power cables:
Schaffner # FN610-1/07 (RLC #LFIL0000)
Schaffner # FN670-1.8/07
Corcom #1VR3
Note: Reference manufacturer’s instructions when installing a line filter.
5. Long cable runs are more susceptible to EMI pickup than short cable runs.
Therefore, keep cable runs as short as possible.
2
SPECIFICATIONS (Cont’d)
5.
SENSOR BREAK DETECTION
: Upscale to 22.5 mA (nominal) or
Downscale to 3.6 mA (nominal) [selectable via DIP switch]
6.
RESPONSE TIME
: 400 msec (to within 99% of final value w/step input;
typically, response is limited to response time of probe.)
7.
DIELECTRIC WITHSTAND VOLTAGE:
1500 VAC for 1 minute
Working Voltage
: 50 VAC from input to output.
8.
CERTIFICATIONS AND COMPLIANCES
:
SAFETY
IEC 61010-1, EN 61010-1: Safety requirements for electrical equipment
for measurement, control, and laboratory use, Part 1.
ELECTROMAGNETIC COMPATIBILITY
Notes:
1. This device was designed for installation in an enclosure. To avoid
electrostatic discharge, precautions should be taken when the device is
mounted outside an enclosure. When working in an enclosure, (ex.
making adjustments, setting switches etc.) typical anti-static precautions
should be observed before touching the device.
2. Self-recoverable loss of performance during EMI disturbance at 10 V/m:
Analog output signal may deviate during EMI disturbance.
For operation without loss of performance:
Unit is mounted in a metal enclosure (Buckeye SM7013-0 or equivalent).
I/O and power cables are routed in metal conduit connected to earth
ground.
9.
ENVIRONMENTAL CONDITIONS:
Operating Temperature Range
: -25°C to 75°C (-13°F to 167°F)
Storage Temperature Range
: -40°C to 85°C (-40°F to 185°F)
Vibration according to IEC 68-2-6
: Operational 5 to 150 Hz in X, Y, Z
direction for 1.5 hours, 2 g’s.
Shock according to IEC 68-2-27
: Operational 30 g’s, 11 msec in 3 directions
Temperature Coefficient
: ± 0.01% of input range per °C
Altitude
: Up to 2000 meters.
10.
MOUNTING:
Universal mounting foot for attachment to standard DIN
style mounting rails, including top hat (T) profile rail according to EN50022 -
35 x 7.5 and 35 x 15, and G profile rail according to EN50035 - G32.
11.
CONNECTION:
Compression type terminal block
12.
CONSTRUCTION:
High impact green plastic case
13.
WEIGHT:
2.7 oz (76.54 g)
Immunity to EN 50082-2
Power frequency magnetic fields EN 61000-4-8 Level 4; 30 A/m
Electrostatic discharge
EN 61000-4-2 Level 2; 4 Kv contact
1
Level 3; 8 Kv air
Electromagnetic RF fields
EN 61000-4-3 Level 3; 10 V/m
2
80 MHz - 1 GHz
Fast transients (burst)
EN 61000-4-4 Level 4; 2 Kv I/O
Level 3; 2 Kv power
RF conducted interference
EN 61000-4-6 Level 3; 10 V/rms
150 KHz - 80 MHz
Emissions to EN 50081-2
RF interference
EN 55011
Enclosure class A
LOOP
POWER
CIRCUITRY
4
5
CIRCUITRY
CONTROL
PWM
POWER
SUPPLY
4V
3V
1.7V
CIRCUITRY
PROCESS
CONVERTER
A/D
2
1
3V
0.170mA
POWER/
OUTPUT
3
RTD
BLOCK DIAGRAM
AUDIN - 8, avenue de la malle - 51370 Saint Brice Courcelles - Tel : 03.26.04.20.21 - Fax : 03.26.04.28.20 - Web : http: www.audin.fr - Email : [email protected]