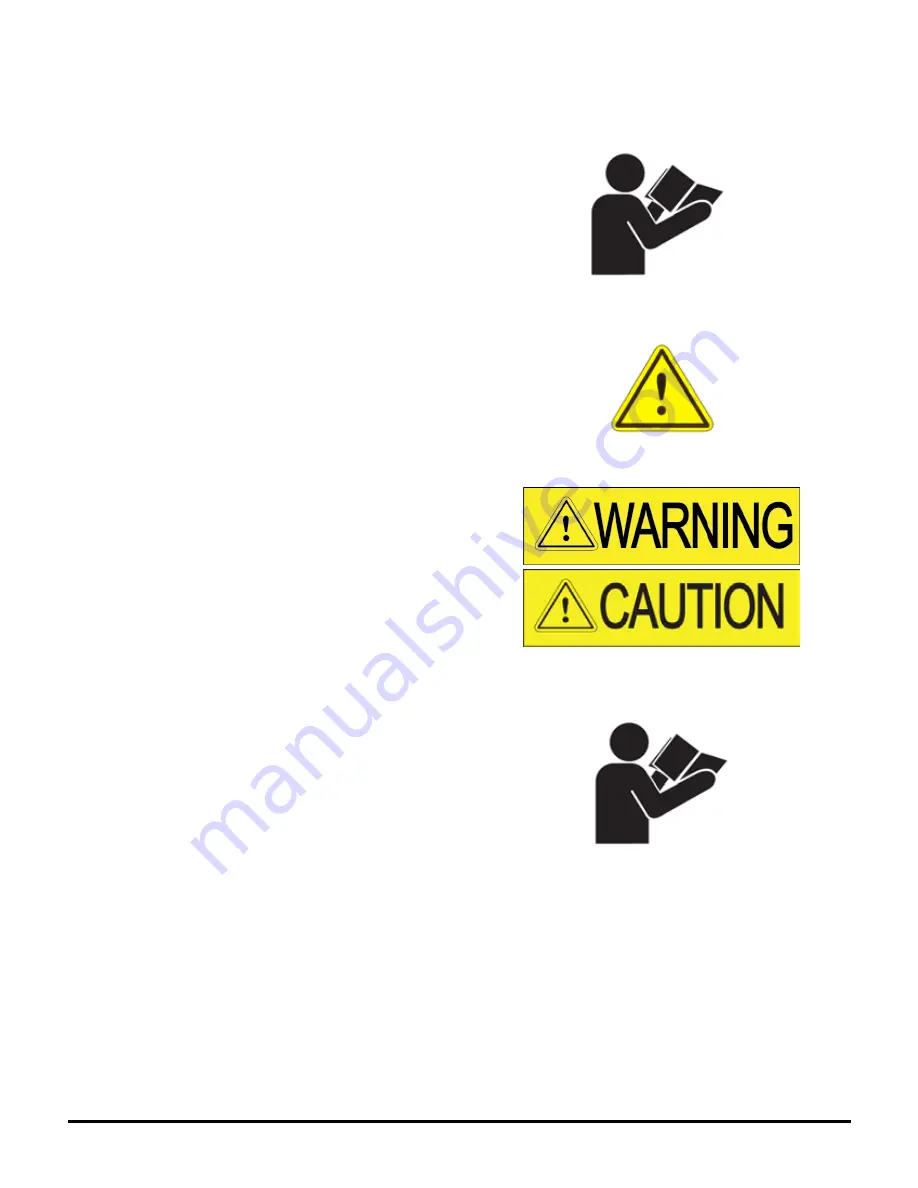
5
0 Safety
0.1 Instructions
0.1.1
IMPORTANT
: Read through this instruction
manual thoroughly and familiarize yourself with the
machine before removing these components. Do not skip
steps or perform them out of order.
This instruction manual explains the proper procedure
for preparing the combine and removing the Factory
Components in order to install the Redekop MAV
Chopper.
0.2 Recognize Safety Information
0.2.1
This is a safety-alert symbol. When you see this
symbol on your straw chopper or in this manual, be alert
to the potential for personal injury.
Follow recommended precautions and safe operating
practices.
0.3 Understand Signal Words
0.3.1
A signal word - DANGER, WARNING, or
CAUTION - is used with the safety-alert symbol.
DANGER identifies the most serious hazards.
WARNING or CAUTION safety signs are located near
specific hazards or precautionary areas in this manual.
0.4 Follow Safety Instructions
0.4.1
Carefully read all safety messages in this manual
and on your machine. Keep safety signs in good
condition. Replace missing or damaged safety signs. Be
sure new equipment components and repair parts include
the current safety signs. Replacement safety signs are
available from your dealer.
There can be additional safety information contained on
parts and components sourced from suppliers that is not
reproduced in this manual.
Learn how to operate the machine and how to use
controls properly. Do not let anyone operate without
instruction.
Keep your machine in proper working condition.
Unauthorized modifications to the machine may impair
the function and/or safety and affect the machine’s life.
If you do not understand any part of this manual and
need assistance, contact your dealer.