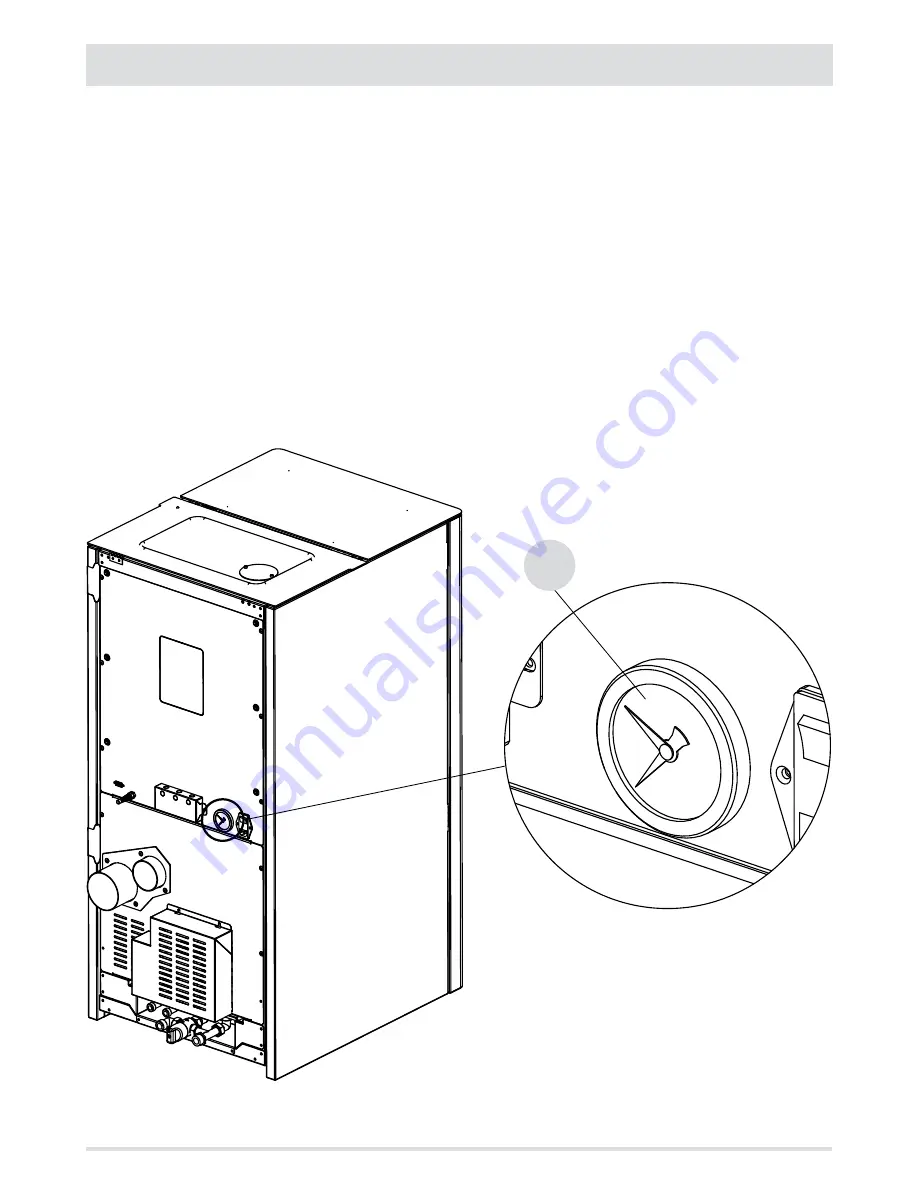
m
34
6-HYDRAULIC CONNECTION
PRESSURE GAUGE
The gauge of the boiler “m” is one of the key tools, which is used to check that appliance is operating smoothly. The pressure gauge of the
boiler is used to measure the pressure, i.e. the difference between the internal pressure and the atmospheric pressure. Generally, the ideal
pressure for a boiler is between 1.5 and 2 bar, above or below which malfunctions occur in the heating system or in the supply of domestic
hot water. The pressure adjustments are made through the vent valve “G” at the top of the boiler (see instructions on the previous page).
Low boiler pressure
When the pressure of the boiler is too low, and therefore it is indicated on the pressure gauge as below 1.5 bar, the heating does not work
well, hot water does not arrive or the boiler is blocked. The main reasons that lower the pressure are:
• Temperature too low, which causes the condensation to form
• Air in the pipes
• A fault in the 3-way valve
High boiler pressure
If the pressure is high, that is the boiler pressure gauge marks more than 2 bar, the energy efficiency of the boiler decreased, which means
that the consumption increases.