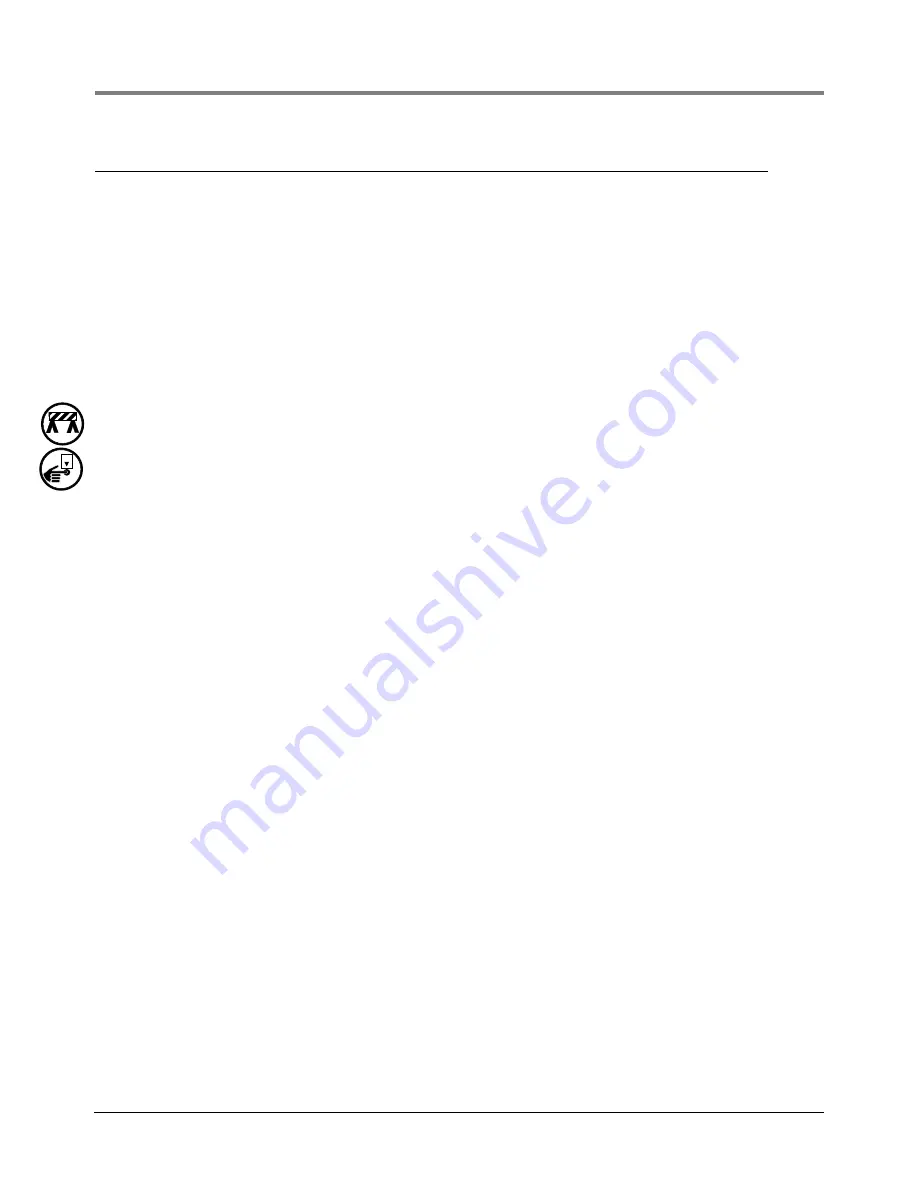
Installing A Red Jacket Submersible LPG Pump-Motor Unit
Gas Filling
28
Gas Filling
Gas Filling Requirements
• This procedure must be done by at least two duly trained technicians, one of whom is responsible for following
up the safety regulations and procedures.
• Gas filling and degassing of the installation has to be done with regard to the hazardous area zone of the
Autogas tank and filling point.
• All parts need to be checked to ensure they are installed correctly before the installation is placed in operation.
• During installation it is not allowed to have open fire or flammable materials within a radius of 15 meters (49
feet), or heated objects with surface temperature exceeding 300ºC (572ºF) or other sources of ignition.
• During fog or windless weather installation should be avoided, as gasses may not be able to evaporate quickly
enough.
• Working area should be fenced and electricity shut off.
• Two (2) portable powder extinguishers of at least 6 kg (13.2 lbs) should be present for immediate use.
Gas filling procedure
1.
Verify that the gas filling requirements above have been met. Make sure all fittings are tight to prevent leaks.
2.
Fill the tank and manifold with nitrogen until pressure reaches 100 kPa (14.7 psi). Relieve pressure until it
reduces to 15 kPa (2.1 psi).
3.
Repeat the filling with nitrogen until it reaches 100 kPa (14.7 psi). Relieve the pressure until it reduces to 15
kPa (2.1 psi).
4.
Fill the tank and manifold with LPG until it reaches 100 kPa (14.7 psi). Relieve the LPG pressure until it
reduces to 15 kPa (2.1 psi). Note: Pressurizing the LPG tank is only allowed through the vapor nozzle of the
tank truck.
5.
Fill the tank and manifold with LPG until it reaches 100 kPa (14.7 psi). Relieve the LPG pressure until it
reduces to 15 kPa (2.1 psi).
6.
Fill the tank and manifold with LPG until it reaches 100 kPa (14.7 psi). Relieve the LPG pressure until it
reduces to 15 kPa (2.1 psi).
7.
Fill the tank and manifold with LPG until it reaches 100 kPa (14.7 psi). Relieve the LPG pressure until it
reduces to 15 kPa (2.1 psi).
8.
After Step 7. , there is maximum 1.7% air in the gas mixture, of which the oxygen concentration can be
measured. The tank and manifold are now ready to be used and can be filled up to maximum 80%.
9.
Check the manifold fittings by applying a mix of water and soap on all the fittings.
10. The pipe lines of the installation and dispenser should now be tested and flushed with nitrogen.
OFF
Summary of Contents for LPG Premier
Page 38: ......
Page 39: ......
Page 40: ...For technical support sales or other assistance please visit www veeder com...