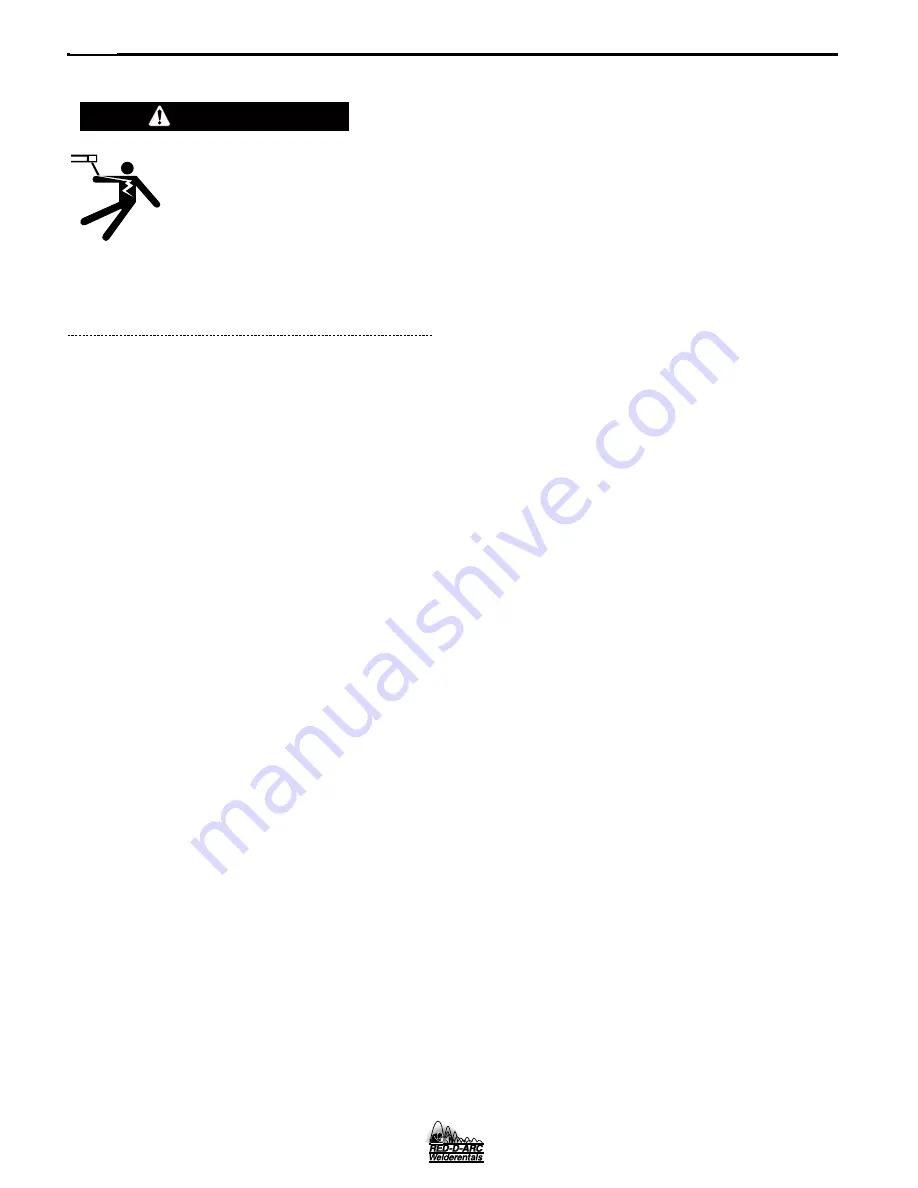
D-1
D-1
MAINTENANCE
3. If using optional adjustable slip-on nozzles, see
Table D.2 in this section.
•
Be sure the nozzle insulator is fully screwed
onto the gun tube and does not block the gas
holes in the diffuser.
•
Slip the appropriate gas nozzle onto the nozzle
insulator. Either a standard .50" (12.7 mm) or
optional .62" (15.9 mm) I.D. slip-on gas nozzle
may be used and should be selected based on
the welding application.
Adjust the gas nozzle as appropriate for the
GMAW process to be used. Typically, the con-
tact tip end should be flush to .12" (3.2 mm)
extended for the short-circuiting transfer
process and .12" (3.2 mm) recessed for spray
transfer.
GUN TUBES AND NOZZLES
1. Replace worn contact tips as required.
2. Remove spatter from inside of gas nozzle and from
tip after each 10 minutes of arc time or as required.
GUN CABLE CLEANING
To help prevent feeding problems, clean cable liner
after using approximately 300 pounds (136 kg) of
electrode. Remove the cable from the wire feeder and
lay it out straight on the floor. Remove the contact tip
from the gun. Using an air hose and only partial pres-
sure, gently blow out the cable liner from the gas dif-
fuser end.
Excessive pressure at the start may cause the dirt
to form a plug.
Flex the cable over its entire length and again blow
out the cable. Repeat this procedure until no further
dirt comes out. If this has been done and feed prob-
lems are experienced, try liner replacement, and refer
to trouble shooting section on rough wire feeding.
SAFETY PRECAUTIONS
ELECTRIC SHOCK can kill.
•
Have an electrician install and
service this equipment.
•
Turn the input power off at the
fuse box before working on
equipment
•
Do not touch electrically hot
parts.
GENERAL MAINTENANCE
In extremely dusty locations, dirt may clog the air pas-
sages causing the welder to run hot. Blow dirt out of
the welder with low-pressure air at regular intervals to
eliminate excessive dirt and dust build-up on internal
parts.
The fan motors have sealed ball bearings which
require no service.
DRIVE ROLLS AND GUIDE PLATES
After every coil of wire, inspect the wire drive mecha-
nism. Clean it as necessary by blowing with low pres-
sure compressed air. Do not use solvents for cleaning
the idle roll because it may wash the lubricant out of
the bearing. All drive rolls are stamped with the wire
sizes they will feed. If a wire size other than that
stamped on the roll is used, the drive roll must be
changed.
For instructions on replacing or changing drive roll,
see
“
Wire Drive Rolls
”
in Operation section.
CONTACT TIP AND GAS NOZZLE
INSTALLATION
1. Choose the correct size contact tip for the elec-
trode being used (wire size is stenciled on the side
of the contact tip) and screw it snugly into the gas
diffuser.
2. Screw the appropriate fixed gas nozzle fully onto
the diffuser. Either the standard .50" (12.7 mm)
flush nozzle or other optional flush or recessed
(spray arc) nozzle sizes may be used. (See Table
D.2 in this section.)
WARNING
PM 255
Summary of Contents for PM 255
Page 31: ...F 2 F 2 DIMENSION PRINT 3 00F M19231 PM 255...
Page 32: ...NOTES PM 255...
Page 33: ...NOTES PM 255...
Page 34: ...NOTES PM 255...