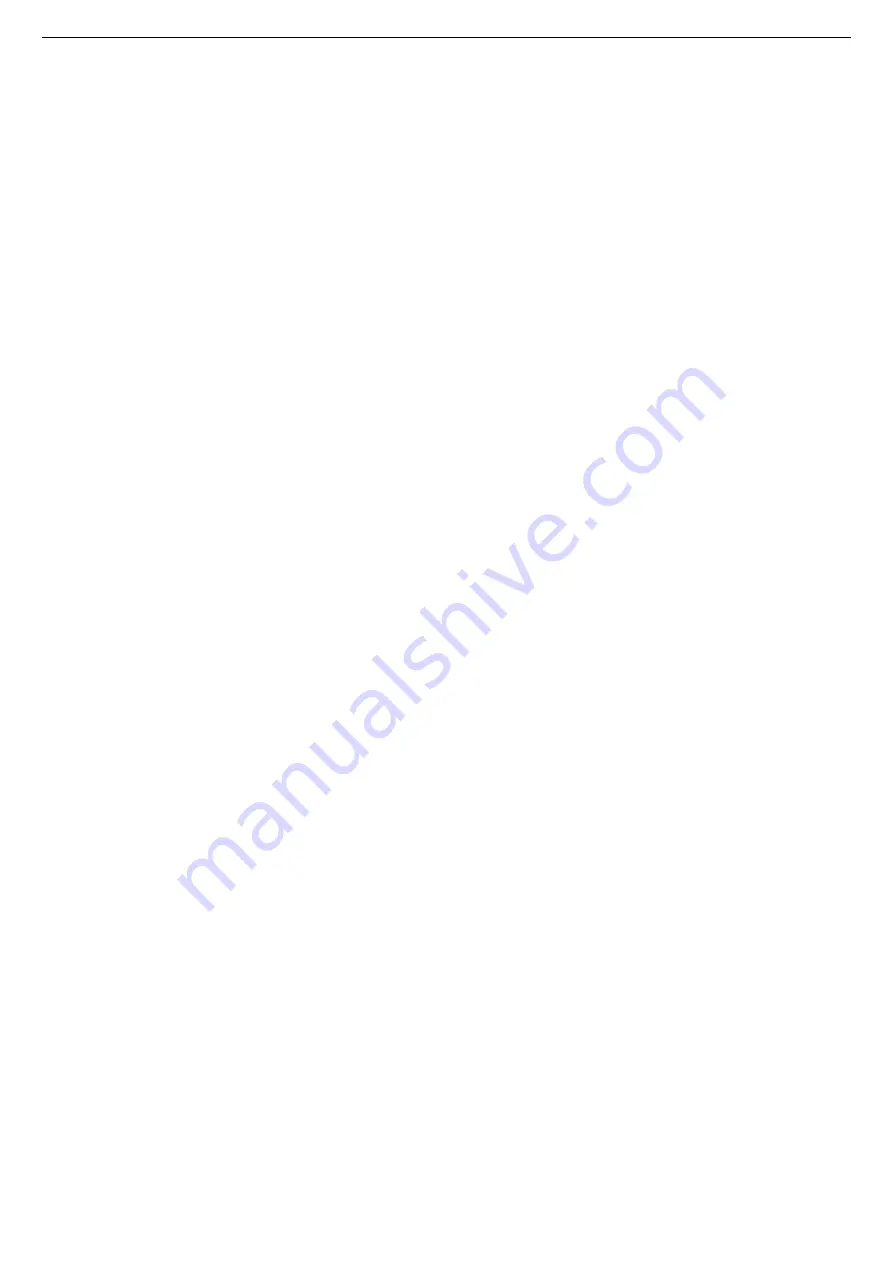
Version Number: RBM2000P-20210517A1
22
Note:
1. Please strictly follow the picture instructions to connect, otherwise it will not be possible to solder.
2. Aluminum welding wire supports 1.2mm(AL-Mg or AL-Si).
3. The machine can install 5kg(11lb) and 1kg(2.2lb) wire reels.
4. The machine comes with a 0.5kg(1.1lb) 5356AL-Mg welding wire or 1kg
(
2.2lb
)
Flux-cored wire.
5. Support welding material is aluminum.
6. The diameter of the welding wire, the groove of the wire feed wheel and the aperture of the contact tip
must match.
7. The pressure roller of the wire feeding structure should not be too tight or too loose, which will cause the
wire feeding to be unstable.
8. The installation of the wire feeding reel should not be too loose or too tight, which will cause the welding
wire of the wire reel to spring off and the wire feeding is too slow.
Possible problems
1) There is no response when turning on the power, please check the plug connection.
2) There is no response when turning on the power, please open the cover and check whether the internal
connecting wires are loose.
3) The wire feeding is unstable. Please check the wire feeding reel and the wire feeding pressure roller, and
the welding gun should not be wound. Pay attention that the diameter of the welding wire matches the wire
feeding wheel groove and contact tip.
4) No wire feeding, please confirm that the working mode is MIG state, please confirm that the welding gun is
connected well, press the gun switch or no wire feeding, please contact us.
5) During the welding process, if the time exceeds 3 minutes, over-current protection may occur. You need to
stop working for a few minutes, let the machine cool for a period of time, and automatically recover. If the air
cools for more than 10 minutes, the machine does not automatically recover, please shut down and restart.
6) If you have any questions, please contact us at.