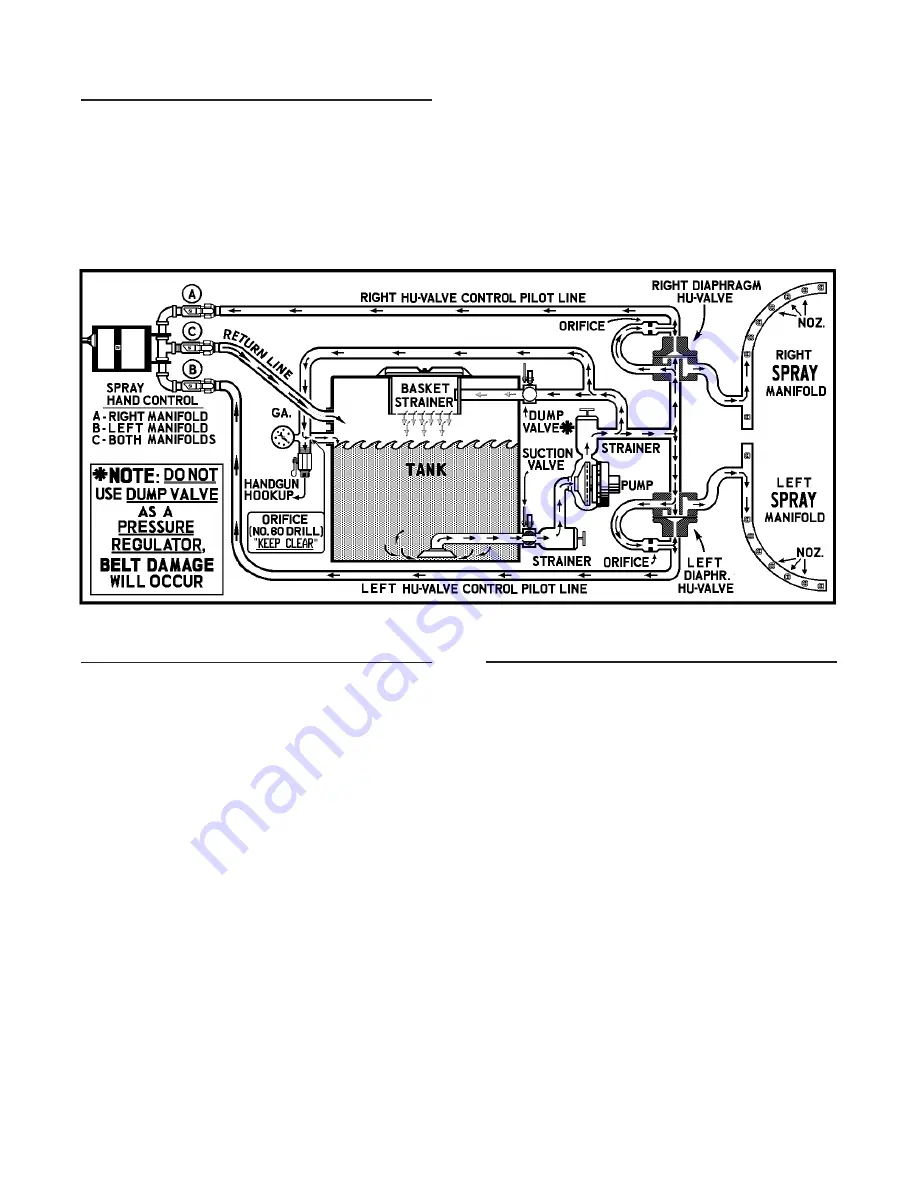
19
Pul-Blast
AR pump system
Read this manual completely before operating: follow all safety instructions.
troubleshooting: excessive pressure drop
Check the dump valve. When spraying, the dump valve
must be completely closed. Using the dump valve to con
-
trol spray pressure will result in early belt failure.
Check the tension of the pump drive belt: see the pump
maintenance section of this manual.
Check the suction and discharge strainers- clean screens.
troubleshooting: spray manifold will not spray
Check that there is liquid in the tank.
Check that pressure is adequate on pressure gauge. If
not, refer to the pressure drop section, above.
Check the hand control pilot line (manual controls) for
crimping. Bleed off air at the handgun hookup valve.
Check the hand control pilot line (manual controls) for
blockage. Some chemicals can build up in the line or
react with the hose lining. If this is a problem, replace
the 3/8” lines with 1/2” hose.
NOTE: Rinse spray system daily.
Check the handset return line (manual controls) for
crimping or blockage.
Check the handset valves (manual controls) for blockage.
If you have Hu-valve electric controls, check the spool
rotation (see appropriate parts page for HVC block as
-
sembly illustration). If the spool rotates easily by hand
but not by the motor, check the wiring.
troubleshooting: spray manifold will not shut off
Check Hu-valve orifice and tube for blockage.
Check Hu-valve for ruptured diaphragm.
If you have Hu-valve electric controls, check the spool
rotation (see appropriate parts page for HVC block as
-
sembly illustration). If the spool rotates easily by hand
but not by the motor, check the wiring.
If you have Hu-valve electric controls and the unit
continues to spray with HVC spools in the OFF position,
a blockage caused the valve control to slip, see the HVC
block parts page for repair instructions.