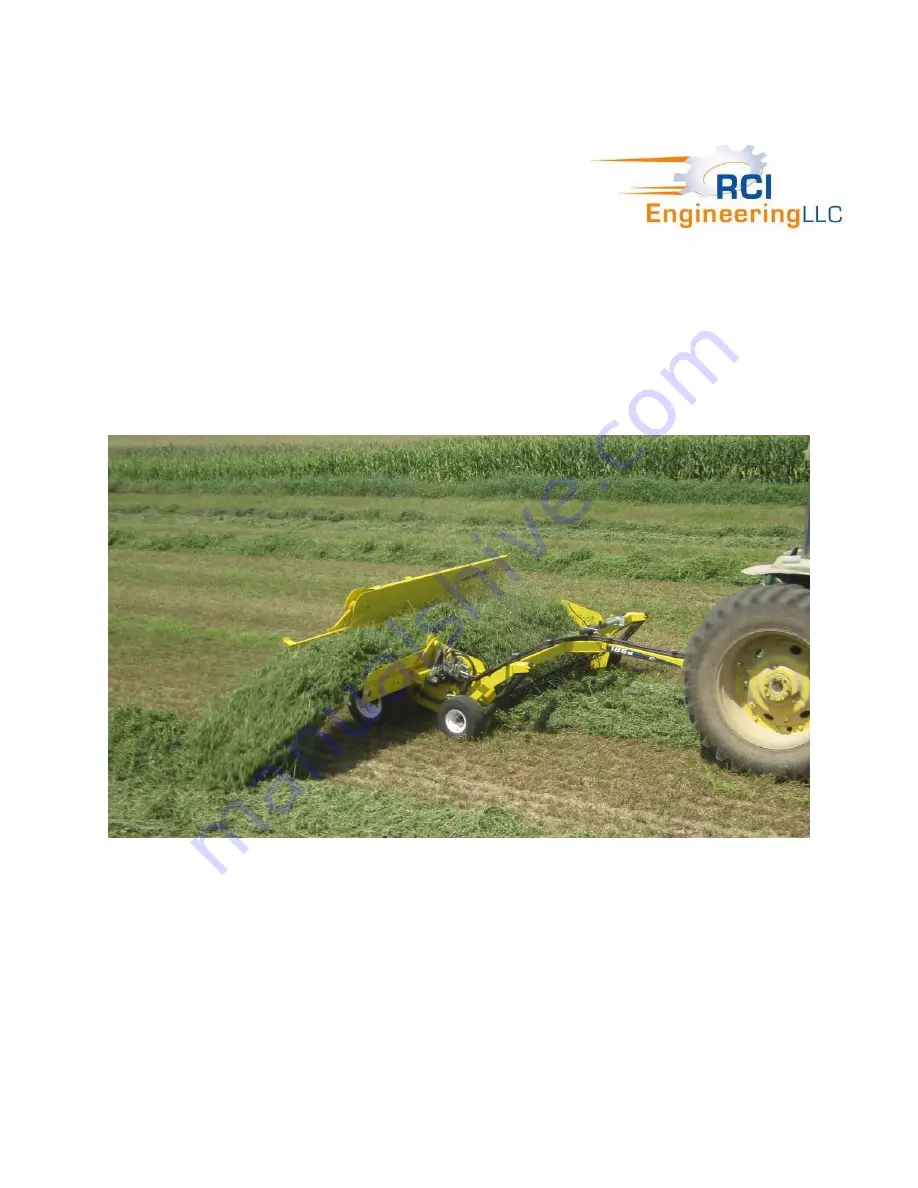
0
186M Windrow Merger
Operator Manual
Includes operating, adjustment, maintenance, technical,
repair parts and safety instructions for the 186M Windrow Merger.
Please retain this document for future reference. Keep this manual available for reference to the
operator at all times. Do not allow anyone to operate this implement without reading and fully
understanding this operator manual. Never allow children to operate on or near any equipment at
any time.
RCI Engineering LLC
RC130102 Rev B 1Nov2017
www.RCIengineering.com
Copyright © 2017 by RCI Engineering LLC
Summary of Contents for 186M
Page 8: ...7 This Page Intentionally Left Blank ...
Page 10: ...9 This Page Intentionally Left Blank ...
Page 16: ...15 This Page Intentionally Left Blank ...
Page 32: ...31 This Page Intentionally Left Blank ...
Page 34: ...33 This Page Intentionally Left Blank ...
Page 35: ...34 Hydraulic Functional Schematic ...
Page 36: ...35 This Page Intentionally Left Blank ...
Page 37: ...36 Bolt and Screw Torque Values ...
Page 38: ...37 This Page Intentionally Left Blank ...
Page 40: ...39 This Page Intentionally Left Blank ...
Page 42: ...41 Hitch And Wheel Components ...
Page 44: ...43 Hitch Pivot Components ...
Page 46: ...45 Pickup Components ...
Page 48: ...47 This Page Intentionally Left Blank ...
Page 50: ...49 Conveyor Components ...
Page 52: ...51 Extension Components ...
Page 54: ...53 Long Extension Components Optional ...
Page 56: ...55 Windguard Components ...
Page 58: ...57 Motor and Manifold Components ...
Page 60: ...59 ...
Page 62: ...61 Decals Left ...
Page 64: ...63 Decals Right ...
Page 66: ...65 Decals Back ...
Page 68: ...67 This Page Intentionally Left Blank ...