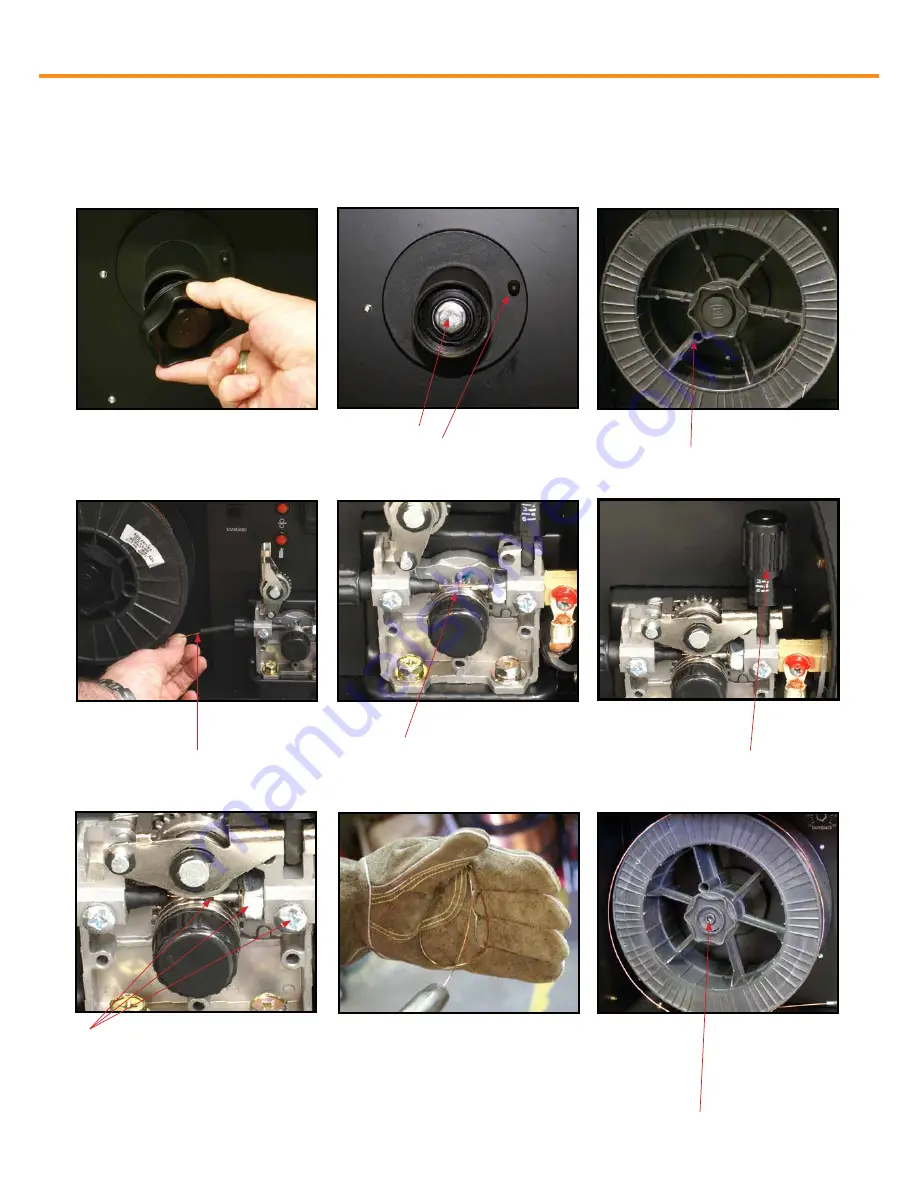
17
Wire Installation and Set Up Guide
Again the importance of smooth consistent wire feeding during MIG welding cannot be emphasized enough.
The correct installation of the wire spool and the wire into the wire feed unit is critical to achieving an even
and consistent wire feed. A high percentage of faults with mig welders emanate from poor set up of the wire
into the wire feeder. The guide below will assist in the correct setup of your wire feeder.
(1) Remove the spool retaining nut.
(3) Fit the wire spool onto the spool holder
fitting the locating pin into the location hole
on the spool. Replace the spool retaining
nut tightly
(2) Note the tension spring adjuster
and spool locating pin.
(7) Check that the wire passes through
the centre of the outlet guide tube without
touching the sides. Loosen the locking
screw and then loosen the outlet guide
tube retaining nut too make adjustment if
required. Carefully retighten the locking nut
and screw to hold the new position.
NOTE: MIG 180-145 not geared
(4) Snip the wire carefully, be sure to hold the
wire to prevent the spool uncoiling. Carefully
feed the wire into the inlet guide tube of the
wire feed unit.
(5) Feed the wire through the drive roller and
into the outlet guide tube of the wire feeder.
NOTE: MIG 180-145 not geared
(6) Lock down the top pressure roller and
apply a medium amount of pressure us-
ing the tension adjustment knob
NOTE: MIG 180-145not geared
(8) A simple check for the correct drive tension
is to bend the end of the wire over hold it about
4in
from your hand and let it run into your hand, it
should coil round in your hand without stopping
and slipping at the drive rollers, increase the
tension if it slips.
(8) The weight and speed of the wire spool
turning creates an inertia that can cause the
spool to run on and the wire loop over the
side of the spool and tangle. if this happens
increase the pressure on the tension spring
inside the spool holder assembly using the
tension adjustment screw.