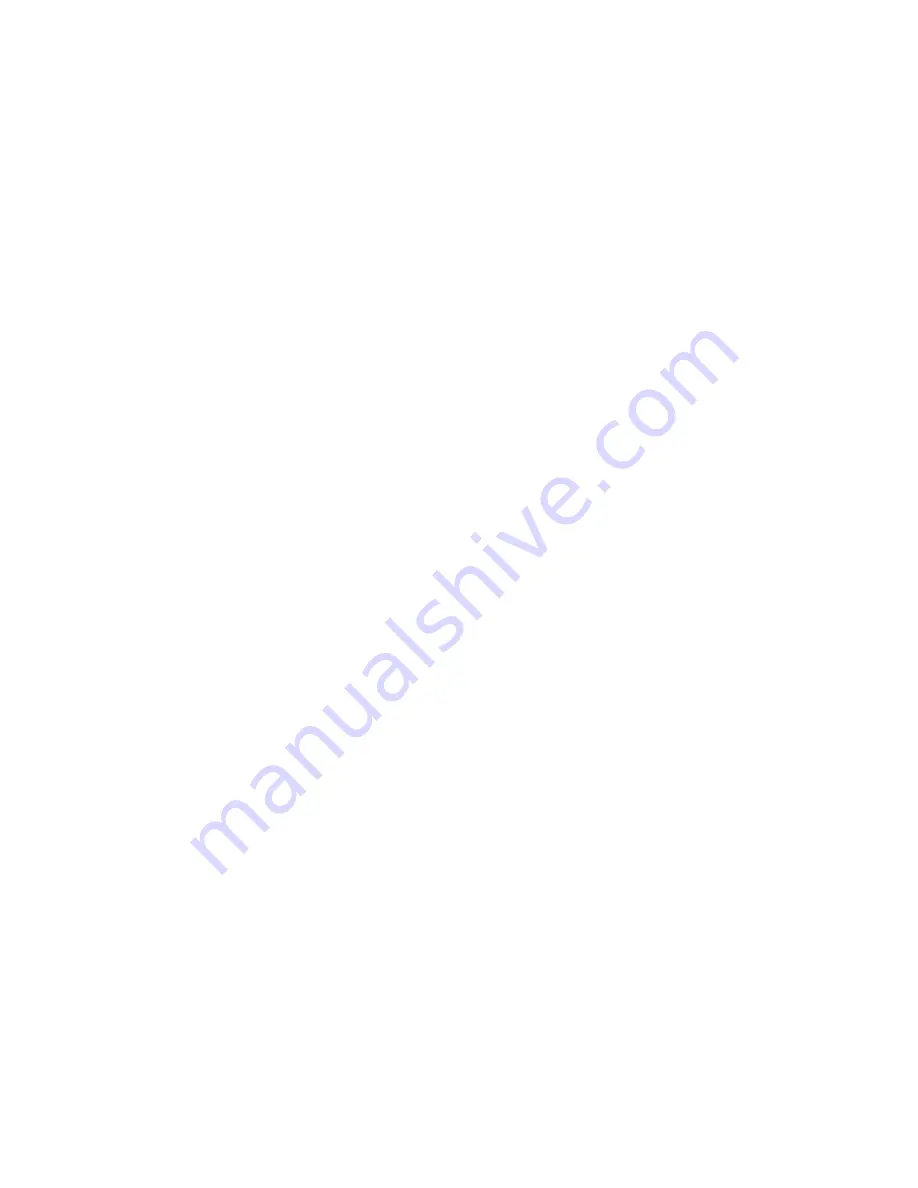
11
Preventive Maintenance Schedule
WARNING: Preventative maintenance should ONLY be
performed by a qualified service agency in accordance with
the procedures listed in the heater Installation and Operating
Instruction Manual.
The following procedures
are recommended and are good
practice for all XPak installations.
Daily
1. Check gauges, monitors and indicators.
2. Check instrument and equipment settings.
Monthly
1. Check flue, vent, stack, or outlet dampers.
Semi-Annually
1. Recalibrate all indicating and recording gauges.
2. Check flame failure detection system components.
3. Check piping and wiring of all interlocks and shutoff valves.
Annually
1. Test flame failure detection system.
2. Test high limit and operating temperature.
3. Check flame sensor.
4. Conduct a combustion test at full fire. Carbon dioxide
should be 8.5% at full fire for natural gas, and 10.0% for
propane gas. Carbon monoxide should be < 130 ppm.
5. Check for leaks at all valve fittings using a soapy water
solution (while heater is operating). Test other operating
parts of all safety shut-off and control valves and increase
or decrease settings (depending on the type of control)
until the safety circuit opens. Reset to original setting
after each dev
ice is tested.
6. Perform leakage test on gas valves.
7. Test air switch in accordance with manufacturer’s
instructions. (Turn panel switch to the “On” position until
blower is proven, then turn the switch to “Off”).
8. The combustion blower motor does not require lubrication
for proper operation. DO NOT attempt to oil the motor or
damage may occur.
As Required
1. Check drip leg and gas strainers.
2. Check flame failure detection system.
3. Check igniter.
4. Check flame signal strength.
5. Test safety/safety relief valves in accordance with ASME
Heater and Pressure Vessel Code Section IV.
6. Alarm 91 (AL91) the main heat exchanger need cleaning