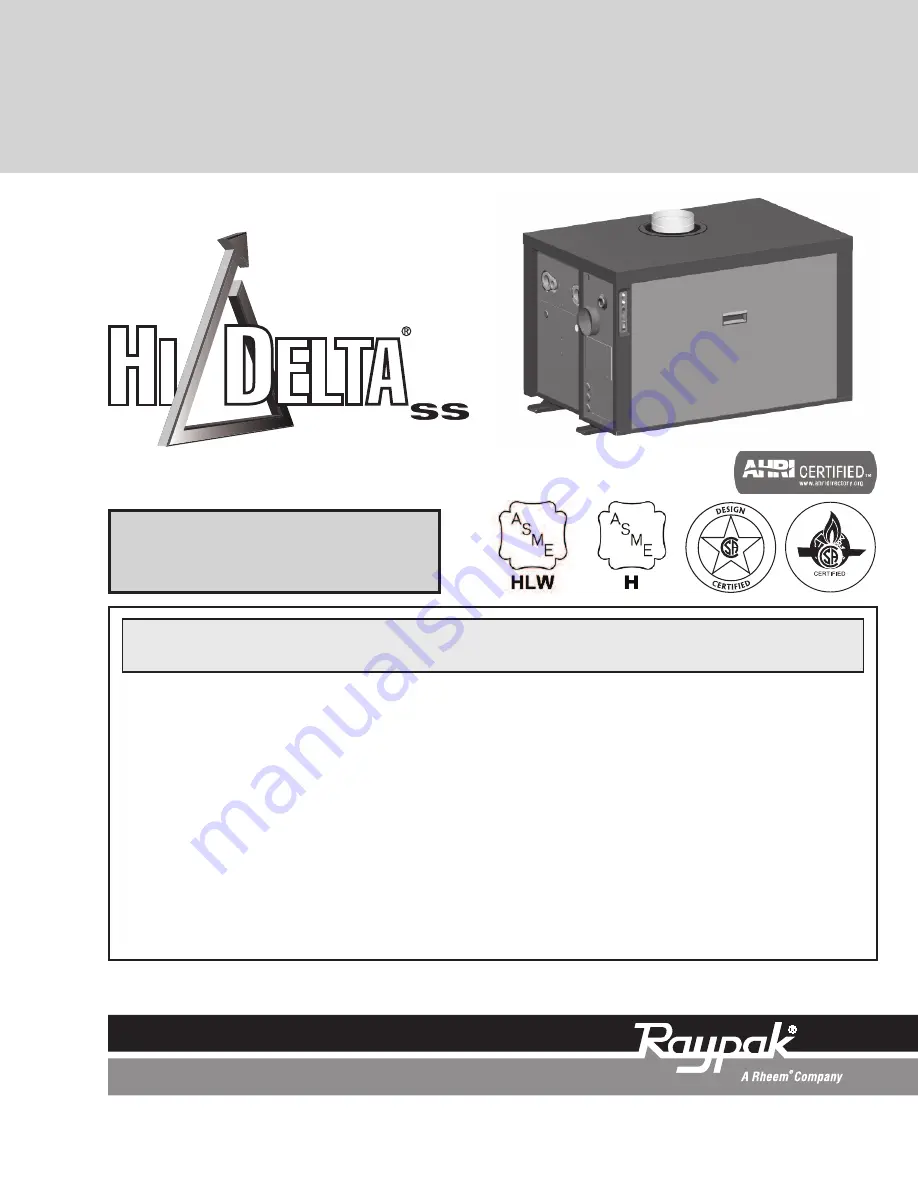
INSTALLATION & OPERATING
INSTRUCTIONS
CATALOG NO. 1000.52D
Effective: 10-15-15
Replaces: 09-14-12
P/N 241356 Rev. 5
WARNING:
If these instructions are not followed exactly, a fire or explosion may
result causing property damage, personal injury or death
.
FOR YOUR SAFETY:
Do not store or use gasoline or other flammable vapors and
liquids or other combustible materials in the vicinity of this or any other appliance. To
do so may result in an explosion or fire.
WHAT TO DO IF YOU SMELL GAS:
• Do not try to light any appliance.
• Do not touch any electrical switch; do not use any phone in your building.
• Immediately call your gas supplier from a neighbor's phone. Follow the gas
supplier's instructions.
• If you cannot reach your gas supplier, call the fire department.
Installation and service must be performed by a qualified installer, service agency or
the gas supplier.
This manual should be maintained in legible condition and kept adjacent to the heater or in another safe place for
future reference.
Models
HD101–HD401
Types H & WH
®
Summary of Contents for HI DELTA HD401
Page 36: ...36 WIRING DIAGRAM MODELS HD101 HD151 TYPE WH...
Page 37: ...37 WIRING DIAGRAM MODELS HD101 HD151 TYPE H...
Page 38: ...38 WIRING DIAGRAM MODELS HD201 HD401 TYPE WH...
Page 39: ...39 WIRING DIAGRAM MODELS HD201 HD401 TYPE H...
Page 50: ...50...
Page 51: ...51...