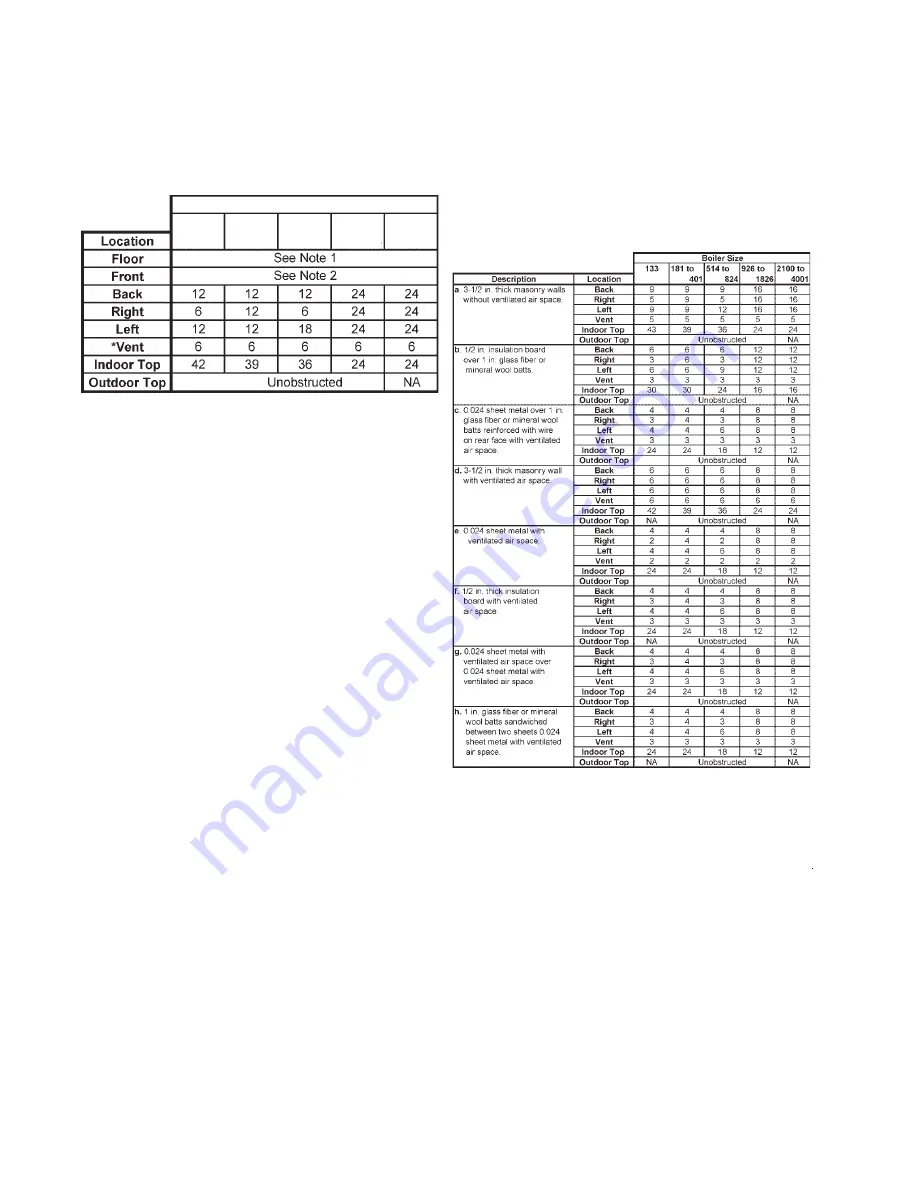
REDUCTION OF CLEARANCES TO PROTECTED
SURFACES
CLEARANCES
CLEARANCES FROM COMBUSTIBLE SURFACES
(All dimensions are in inches)
Note: The boiler shall be installed in a space large in
comparison to the size of the boiler. Large space is
defined as having a volume at least sixteen (16) times
the total volume of the boiler.
Note 1:
Combustible floor shield is required when boiler is to be
installed on a combustible surface. (See ordering infor-
mation on pg. 4.)
Note 2:
Servicing Clearances: Provide at least 24" (Models
133-1826), 48" (Models 2100-4001) in front of unit for
removal and servicing of the Controls & Burner Tray.
Provide at least 18" on side opposite water connections
for deliming of Heat Exchanger Tubes.
*Vent includes factory-supplied drafthood and does not
include field-supplied vent systems above the draft-
hood. On Models 2100-4001 drafthood is built into
boiler.
6
Derived from National Fuel Gas Code, Table 6.2.3(a)
Derived from National Fuel Gas Code, Table 6.2.3(b)
MODEL
133
181 to
401
514 to
824
926 to
1826
2100 to
4001